اگر از فولاد کربندار محافظت نشود در بسیاری از محیطها زنگ میزند. به همین علت از روشهای زیادی برای اصلاح فولاد و انواع فلزات کمک گرفته میشود تا از خوردگی آن جلوگیری کنند.
دو راه حل استفاده از فولاد ضد زنگ و گالوانیزهکردن فولاد جزو محبوبترین روشها برای این مشکل است. در حالی که هر دو فولاد در برابر زنگ زدگی و خوردگی مقاومت میکنند تفاوتهای مهمی نیز بین آنها وجود دارد.
در این مقاله قرار است درمورد آهن گالوانیزه و کاربرد و مزایای آن صحبت کنیم که در ادامه به این موارد بیشتر پرداخته شده است.
فهرست مطالب
- چرا از فرآیند گالوانیزه کردن استفاده میکنند؟
- روشهای مختلف برای گالوانیزه کردن
- 1) گالوانیزه گرم
- 2) پیش گالوانیزه کردن
- 3) الکترو گالوانیزه کردن
- 4) استخر مذاب گالوانیزه
- فولاد ضد زنگ چیست؟
- فولاد گالوانیزه چیست؟
- مقاومت فولاد ضد زنگ در برابر خوردگی
- مقاومت فولاد گالوانیزه در برابر خوردگی
- کاربرد فولاد ضد زنگ
- کاربرد فولاد گالوانیزه
- تفاوت فولاد ضد زنگ و فولاد گالوانیزه
گالوانیزه کردن روشی برای محافظت از میلگرد و مقاطع فولادی در برابر خوردگی است. این فرآیند شامل استفاده از یک پوشش نازک فلزِ روی (Zinc) بر روی فلزی پایه که ضخامت آن بیشتر از ضخامت لایه پوشش است، میباشد. این کار به محافظت از فلز در برابر عوامل محیطی کمک میکند.
دفعه بعد هنگامی که سوار اتومبیل شدید به تابلو علائم رانندگی در خیابان و تیر چراغها که به رنگ نقرهای هستند، نگاهی بیندازید. این رنگ نقرهای همان پوشش روی است و جهت حفاظت آنها در برابر عوامل جوی انجام شده است.
چرا از فرآیند گالوانیزه کردن استفاده میکنند؟
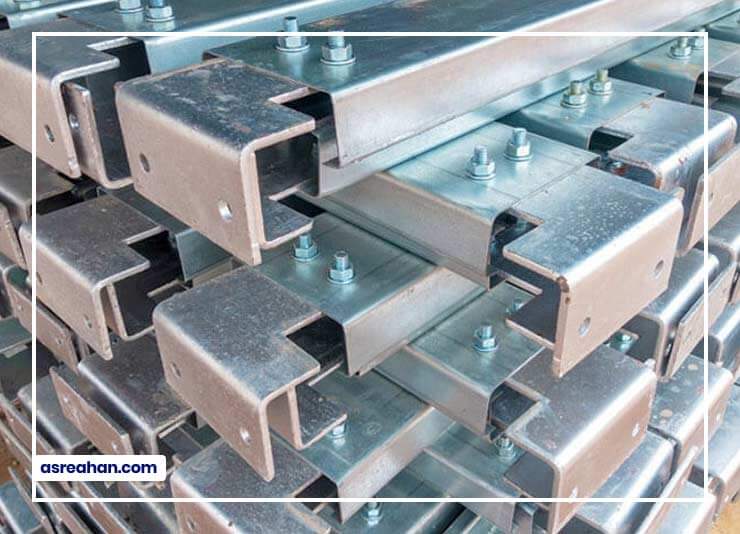
پاسخ به این سوال خیلی ساده است؛ گالوانیزهکردن فلز به آن خاصیت مقاومت در برابر خوردگی میبخشد. بدون محافظ و پوشش، فلز در معرض عناصر دیگر و رطوبت قرار میگیرد و به همین علت سریعتر اکسید شده و خورده میشود.
در گالوانیزه کردن، لایه فلز روی (Zn) از خوردگی فولاد توسط آب و رطوبت جلوگیری میکند؛ اما اگر فلز روی، عمیق خراش خورده شود فولاد زیرین در معرض خوردگی قرار میگیرد.
از طرفی گالوانیزه سازی میتواند از فلز در برابر خوردگی گالوانیک محافظت کند. خوردگی گالوانیک زمانی اتفاق میافتد که دو فلز از یک ترکیب الکتروشیمیایی متفاوت با یک الکترولیت مانند آب شور با یکدیگر در تماس باشند.
بسته به ساختار اتمی دو فلز، یک فلز آنُد با سرعت بیشتری فرسایش مییابد و کاتد با سرعت کمتری خورده میشود.
دلیل استفاده از روی برای گالوانیزه کردن این است که وقتی در تماس با انواع مختلفی از فلزات است، به آند بودن بیشتر علاقه دارد. از آنجا که پوشش فلز روی در تماس با فلز زیرین معمولا آند است، باعث کند شدن خوردگی فلز زیر و یا کاتد میشود.
فولاد گالوانیزه چیست؟
فولاد گالوانیزه یا آهن گالوانیزه نوعی فولاد است که توسط لایهای از فلز روی (Zinc) پوشانده شده است و به جلوگیری از زنگ زدگی فولاد زیرین کمک میکند.
این لایه معمولا کاملا نازک است و اغلب با میکرون اندازهگیری میشود. برای ساخت فولاد گالوانیزه معمولا لایه روی (Zinc) پس از ذوب، تصفیه و فرمدهی ورق به آن اضافه میشود.
روشهای مختلف برای گالوانیزه کردن
چندین فرآیند مختلف برای گالوانیزه سازی فلز وجود دارد که در ادامه به شرح آنها میپردازیم.
1) گالوانیزه گرم (Hot-Dip Galvanizing)
همان طور که از نام آن مشخص است این روش بر پایه عملیات حرارتی انجام میشود و شامل فرو بردن فلز فولاد یا هر فلز پایه در استخر مذاب روی (Zn) است.
ابتدا فلز پایه باید بهصورت مکانیکی، شیمیایی یا توسط هر دو روش تمیز شود تا اطمینان حاصل شود که میتوان بین فلز و پوشش روی با کیفیت بیشتری پیوند ایجاد کرد.
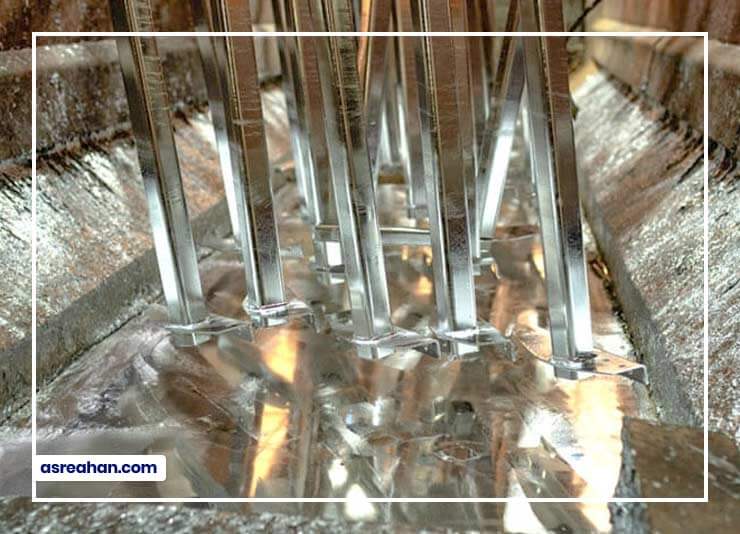
پس از تمیز کردن، فلز پایه از شر اکسیدهای باقی مانده از فرآیند تمیز کردن، خلاص میشود. در مرحلۀ بعد فلز پایه در یک وان مذاب فلز Zinc گرم، فرو رفته و یک پیوند متالوژی تشکیل میشود.
از مزایای این روش میتوان به اقتصادی بودن آن اشاره کرد؛ همچنین با استفاده از روش گالوانیزه گرم میتوان مقاطعی را که شکل پیچیدهتری دارند را گالوانیزه کرد. این روش در مقایسه با سایر روشهای گالوانیزه کردن، ممکن است در ارتباط با نوع فلز حالت ناسازگاری داشته باشد.
2) پیش گالوانیزه کردن (Pre-galvanizing)
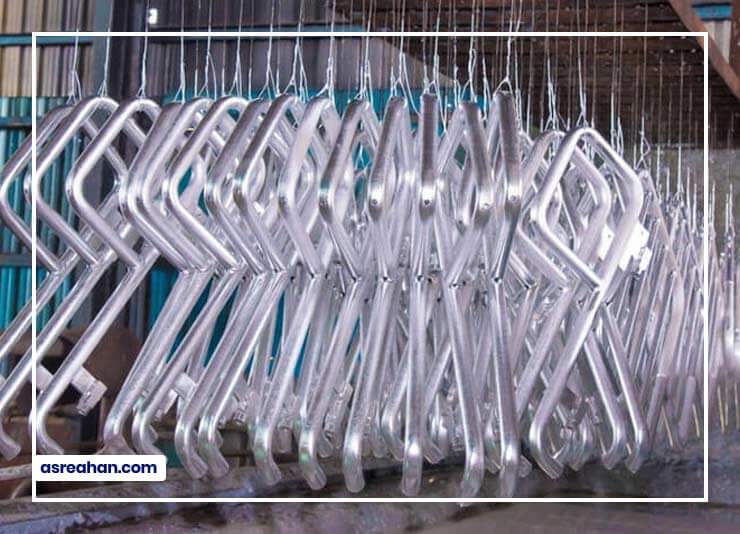
این روش بسیار شبیه به روش گالوانیزه گرم است با این تفاوت که در کارخانۀ تولید فولاد روی محصولات تولید شده انجام میشود.
پیش گالوانیزه کردن شامل نورد ورق فولادی از طریق فرآیندی مشابه فرآیند گالوانیزه گرم است و از استخر روی (Zinc) مذاب و مایع عبور داده میشود. سپس برای سرد شدن مقطع موردنظر، آهن گالوانیزه را از جایی در حال خود آویزان میکنند تا زمانی که کاملا خشک شود.
مزیت این روش در این است که رول پیچهای بزرگ ورق گالوانیزه را میتوان به سرعت توسط پوشش یکنواختتری در مقایسه با روش گالوانیزه گرم انجام داد.
تنها ضعفی که برای آن میتوان نام برد این است که ممکن است برخی نواحی بدون پوشش باقی بمانند.
3) الکترو گالوانیزه کردن (Electrogalvanizing)
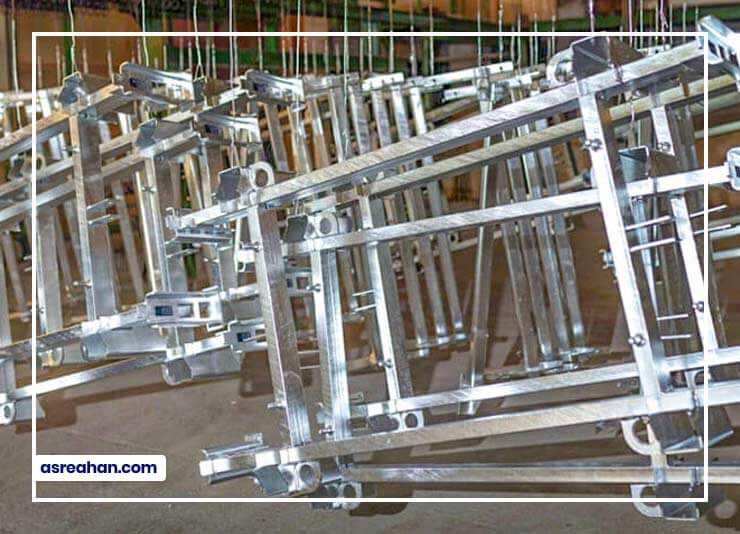
برخلاف فرآیندهای قبلی در الکتروگالوانیزاسیون از استخر مذاب استفاده نمیشود. در عوض در این فرآیند از جریان الکتریکی موجود در محلول الکترولیت برای انتقال یون روی به فلز پایه استفاده میکنند.
این فرایند شامل کاهش الکترولیکی یون روی (Zinc) با بار مثبت به فلز روی است. سپس بر ماده دارای بار مثبت رسوب میکند. این روش نیز برای رول ورق فلزی اعمال میشود.
از مزایای فرآیند الکتروگالوانیزه به پوشش یکنواخت و ضخامت دقیقی که بر تمام سطح ایجاد میکند، میتوان اشاره کرد. لازم به ذکر است ضخامت پوشش در این روش نازکتر از روش گالوانیزه گرم است.
4) استخر مذاب گالوانیزه
روش دیگری از گالوانیزه کردن وجود دارد که بسیار مشابه روش گالوانیزۀ گرم است. یعنی تمیزکردن و فروبردن محصولات در داخل استخر مذاب فلز روی.
این روش مطابق روشهای قبل انجام میگیرد فقط بعد از اتمام این مرحله قطعه گالوانیز شده زیر لبه تیزی قرار میگیرد تا مقدار اضافی پوشش کنده شود و لایۀ یکدست و نازکی حاصل گردد.
در انتهای فرآیند، قطعات در داخل کوره قرار میگیرند و در آنجا میمانند تا زمانی که فولاد تحت مدت زمان مشخصی به دمای پخت برسد؛ سپس در ابعاد مشخص برش داده میشوند.
فولاد گالوانیزه شده توسط این روش، دارای پوششی مات است و این در مقایسه با بقیه آهن گالوانیزه ها جلوۀ بصری زیباتری خواهد داشت؛ همچنین کیفیت و جنس سطح باعث رنگپذیری بهتری میشود.
لایه پوششی این فرآیند، سختتر و مقاومتر از بقیه فرآیندهای گالوانیزه است؛ در بین فلزات گالوانیزه شده، این نوع فلز خاصیت جوشکاری بهتری دارد.
ویدئوی ساخت آهن گالوانیزه گرم روی قطعات فلزی را میتوانید در زیر مشاهده کنید:
فولاد ضد زنگ بهدلیل داشتن عناصر آلیاژی اضافی در ترکیبات شیمیایی، مقاوم در برابر خوردگی بوده در حالی که ترکیبات فولاد معمولی شامل آهن و کربن است.
فولاد ضد زنگ دارای مقدار زیادی کروم است که به آن کمک میکند تا در برابر خوردگی مقاومت کند. کروم و سایر عناصر آلیاژی در طی فرآیند ذوب اولیه قبل از شکل گیری به فولاد ضد زنگ اضافه میشود.
بخوانید: همه چیز درباره ی فولاد ضد زنگ (قسمت اول)
آهن گالوانیزه و فولاد ضد زنگ با هم تفاوتهایی دارند. اصلیترین تفاوت این دو فلز یا مقطع در مواد تشکیلهندۀ آنها است.
ترکیبات مقطع ضد زنگ در هنگام نورد و قبل از شکلگرفتن تغییر میکند؛ یعنی با تغییر مواد تشکیلدهندۀ فولاد آن را به فولاد ضدزنگ تبدیل میکنند.
در گالوانیزه کردن آهن همان طور که در متن گفته شد، مقطع بعد از تولید با یک لایه فلز Zinc پوشش داده میشود. هر دو مقطع ضدزنگ و آهن گالوانیزه در برابر خوردگی مقاوم هستند.
مقاومت فولاد ضد زنگ در برابر خوردگی
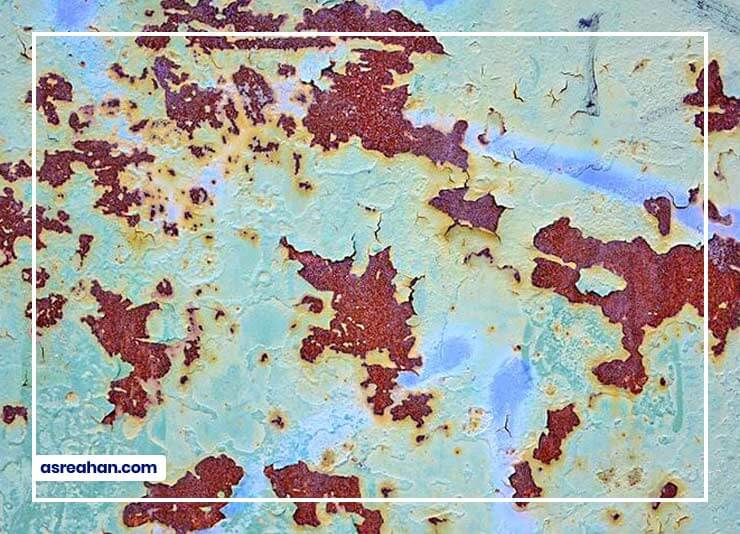
خوردگی در فولاد کربندار زمانی رخ میدهد که آهن موجود در فولاد با اکسیژن در محیط اطراف خود ترکیب شود.
کروم موجود در فولاد ضد زنگ قادر است از این امر جلوگیری کند زیرا با اکسیژن ترکیب شده و یک لایه منفعل از اکسید کروم تشکیل میدهد.
این لایه از اکسید کروم در بسیاری از شرایط از تشکیل اکسید آهن جلوگیری میکند تا زمانی که محتوای کروم فولاد به اندازه کافی زیاد باشد.
مقاومت فولاد گالوانیزه در برابر خوردگی
فولاد گالوانیزه با پوشش فلز روی بر سطح کربن در برابر خوردگی مقاومت میکند. لایه روی (Zinc) که روی سطح فلز کشیده شده است دو هدف دارد:
- اول اینکه از تماس اکسیژن با فولاد جلوگیری میکند؛ بنابراین احتمال خوردگی را کاهش میدهد
- در ثانی حتی اگر قرار باشد پوشش فلز روی آسیب جزئی ببیند و قسمتی از آهن در تماس با هوا باشد، فلز روی موجود در قسمتهای دیگر نسبت به فولاد واکنش نشان میدهد و این باعث میشود که روی، مولکول اکسیژن را بیشتر از آهن جذب کند و از زنگ زدگی فولاد جلوگیری کند.
کاربرد فولاد ضد زنگ
از فولاد ضد زنگ معمولاً درکاربریهایی استفاده میشود که خطر خوردگی یکی از نگرانیهای اصلی است و نباید رخ بدهد مانند:
- ساخت تجهیزات کارخانجات مواد غذایی؛
- تجهیزات ساخت دارو؛
- موتور فضاپیما؛
- وسایل آشپزخانه.
کاربرد فولاد گالوانیزه
از فولاد گالوانیزه زمانی استفاده میشود که خوردگی مطلوب نباشد؛ اما در مقادیر کم مجاز است و از لحاظ ظاهری و زیبایی هم نگران کننده نیست.
بیشترین کاربرد آهن گالوانیزه در موارد زیر است:
- اجزای خودرو؛
- صنعت ساختمان سازی؛
- کابیت سازی؛
- تابلو علائم رانندگی؛
- تیر برق؛
- ساخت نرده؛
- انواع اتصال دهندهها.
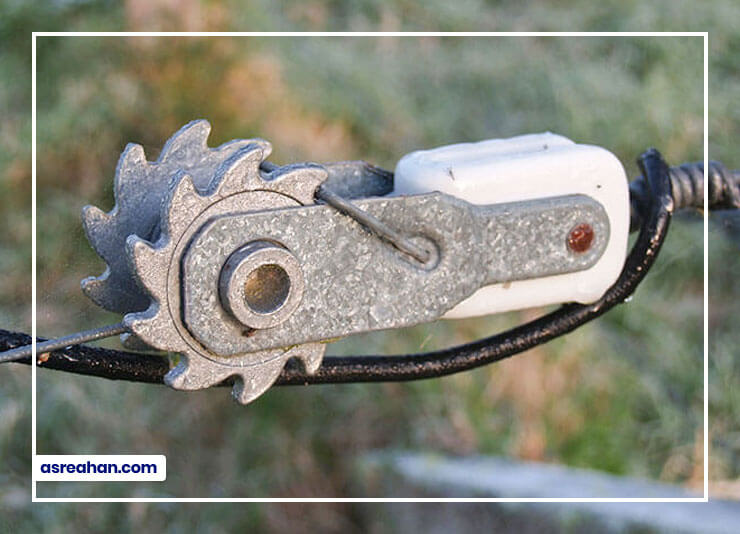
تفاوت فولاد ضد زنگ و فولاد گالوانیزه
تفاوتهای موجود بین این دو فلز دلیلی برای انتخاب و استفاده از هرکدام است؛ یعنی تفاوتهای هر یک از این فلزها است که کاربردهای منحصربهفری برای آنها ایجاد میکند.
در فولاد ضدزنگ علاوهبر آهن و کربن، درصدی کروم و مقداری نیکل نیز به ترکیبات آن اضافه میکنند تا مقاومت فولاد در برابر خوردگی افزایش پیدا کند.
افزودن کروم موجب تشکیل اکسید کروم در فولاد میشود که سطح فلز را در برابر خوردگی و زنگ زدگی محافظت میکند؛ اما در گالوانیزه کردن، سطح فولاد تولید شده را قبل از استفاده توسط فلز روی پوشش میدهند.
فولاد ضد زنگ آستنیتی یا آلومینیوم از جمله فلزات مقاوم در برابر خوردگی هستند که از مقاومت خوبی برخوردارند؛ اما صرفه اقتصادی ندارند به همین علت استفاده از فرآیند گالوانیزه کردن هزینه کمتری خواهد داشت. طبق این دلایل ترجیحاً از فولاد گالوانیزه بیشتر استفاده میشود.
بخوانید: اسید شویی فلزات | هدف از انجام آن، نحوه فرآیند و دیگر نکاتی که باید بدانید
جمع بندی
استفاده از آهن گالوانیزه که شامل روکش فلز روی است نسبت به فولاد بدون روکش مزایایی دارد که در وهله اول افزایش مقاومت فلز در برابر خوردگی است. رنگ پذیری و جوش پذیری بالای آن از جمله مواردی است که استفاده این فلز را توجیه میکند.
گالوانیزه کردن فلز طبق استانداردها و روشهای متفاوتی انجام میشود که در متن به آن پرداخته و تفاوت اساسی آن با فولاد ضد زنگ بررسی شد. اجرای روکش روی در سطح بالایی فلزات موجب کاهش هزینهها در طولانی مدت میشود.
برای دسترسی سریع به آهن آلات موجود در بازار و قیمت روز آهن و فولاد میتوانید با واحد مشاوره عصرآهن با شماره 0414180 در تماس باشید، کارشناسان ما راهنمای شما خواهند بود.
وبسایت عصرآهن تمام اطلاعاتی را که در مورد محصولات آهن و فولاد، قیمت، کاربرد و فروشندگان این محصولات نیاز دارید، برای شما فراهم کرده است.