صنایع مرتبط با آهن و فلزکاری از دیرباز جزو صنایع مادر و از مهمترین ارکان اولیه برای توسعه هر کشور بودهاند. یکی از آلیاژهای پر مصرف آهن، فولاد است که در صنایع مختلف همچون ساخت و ساز، خودروسازی و لوازم خانگی کاربردهای فراوانی دارد. با فراهم آوردن بستری مناسب جهت استفاده بهینه از زنجیره فولاد و آشنایی با صنایع دخیل در ساخت فولاد در کشور، میتوان از خروج سرمایه مرتبط جلوگیری کرد و این صنعت مهم را بیشتر توسعه داد.
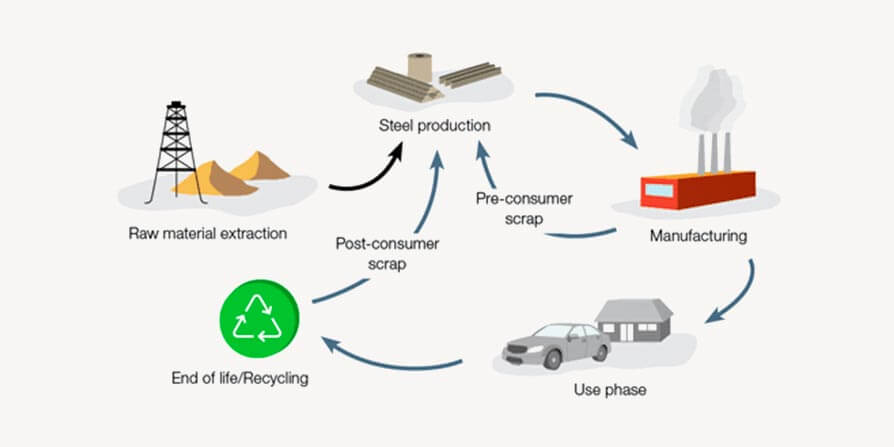
به دلیل ضریب بالای اشتغالزایی صنعت فولادسازی و همچنین رفع نیازهای اولیهی صنایع مختلف در ایران، از دیرباز دولتهای مختلف نگاه ویژهای به زنجیره تولید فولاد در داخل کشور داشته اند. این صنعت خود به سه بخشِ صنایع معدنی، فولاد سازان و نوردکاران وابستگی شدیدی دارد.
ایران با داشتن معادن بسیار غنی و نیروی کار فراوان، میتواند این صنعت را به یکی از صنایع پرسود حتی در بخش صادرات تبدیل کند. در این راستا، شناخت زنجیره فولاد؛ آشنایی با صنایع دخیل در ساخت فولاد در کشور از اهمیت بالایی برخوردار است.
زنجیره تولید فولاد؛ بایدها و نبایدها در صنعت مادر
روند روبه افزایش تجارت جهانی در صنعت فولادسازی، نشان از جایگاه کلیدی این صنعت در آبادانی کشورهای مختلف را نشان میدهد. رشد کشورها و رسیدن به اهداف بلندمدت و حتی کوتاهمدت دولتها، این صنعت مادر را به یکی از پر رونقترین صنایع مدل کرده است.
در ایران نیز جهت رفع نیازهای صنایع خودروسازی، ساختمانی و همچنین صنایع مرتبط با تولید لوازم خانگی، پیشرفتهای وسیعی در زنجیره تولید فولاد از پیش از انقلاب و پس از آن صورت گرفته است. از اینرو دولتها با سرمایهگذاری مناسب در این صنعت پرکاربرد در داخل کشور، میتوانند از برون رفتِ بوجه جلوگیری نمایند.
زنجیره فولاد در ایران آینده
در حال حاضر و با توجه به شرایط رکود، تولید فولاد در ایران نزدیک به سی میلیون تُن به صورت سالانه تخمین زده شده است که تنها نیمی از این ظرفیت، در حال بهرهبرداری میباشد. با اعطای خدمات و ارائهی تسهیلات ویژه به سرمایهگذاران، میتوان ظرفیتهای کشور را بیش از پیش بالا برد. در سند چشم انداز ایرانِ 1404، تولید سالانه فولاد خام در کشور باید از 55 میلیون تن عبور کند.
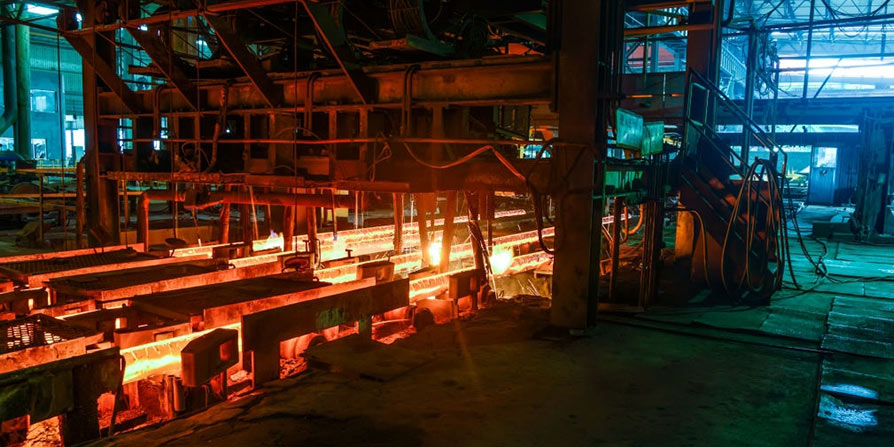
زیرساختهای لازم برای تولید بیشتر فولاد در کشور
دسترسی واحدهای فولادی در کشور به خطوط ریلی و نزدیکی آنها به بنادر مهم و رفع نیازهای اولیه که شامل آب، برق و گاز میباشد و همچنین بالابردن کیفیت معادن بالادستی، میتوانند در تولید و به کارگیری فولاد نقش مهمی را ایفا کنند.
با توجه به نگاه ویژهای که به صادرات غیر نفتی در چند دهه اخیر در کشور شده است، صنایع فولاد در ایران از پتانسیل بسیار بالایی برای جذب سرمایههای خارجی برخوردار است. در سال 1395 برای اولین بار صادرات محصولات زنجیره فولادی از واردات آن پیشی گرفت.
چشمانداز صادرات در ایران 1404
کشورهای منطقه که از دیرباز مشتری محصولات فولادی کشور بودند، خود اقدام به استخراج سنگ آهن و تولید فولاد کردهاند. کشورهای خاورمیانه با احداث کارخانجات نورد در سالهای اخیر، توانستهاند نیازهای خود را در داخل کشور برآورده کنند. از اینرو با کاهش هزینهی تولید فولاد در واحدهای فلزکاری و ذوبآهنی کشور، میتوان به صادرات 14 میلیون تُن محصولات فولادی که در سند چشمانداز ایران 1404 آمده، دست یافت. با بهروز رسانی صنایع بالادستی نظیر معادن، کارخانجاتِ فولادسازی و همچنین استفاده از پیشرفتهترین دستگاههای نورد، میتوان به این مهم دست یافت.
بخشهای مختلف زنجیره فولاد
صنایع معدنی، فولادسازان و نوردکاران از بخشهای اصلیِ زنجیره تولید فولاد در داخل کشور میباشند. هر یک از این واحدها، به صورت مستقل و در عین حال مرتبط با دیگر واحدها، نقش کلیدی را در صنعت فلز کشور ایفا میکنند. با توجه به رقابتی بودن بازار فولاد در سطح جهانی، هرچه هزینهی پایانی در تولید فولاد کمتر باشد، کشورهای بیشتری خواهانِ خرید این فلز پرکاربر میشوند. لزا شناخت و داشتن آگاهی از این سه بخش؛ صنایع معدنی، فولادسازی و نورد کاری از اهمیت بالایی برخوردار است.
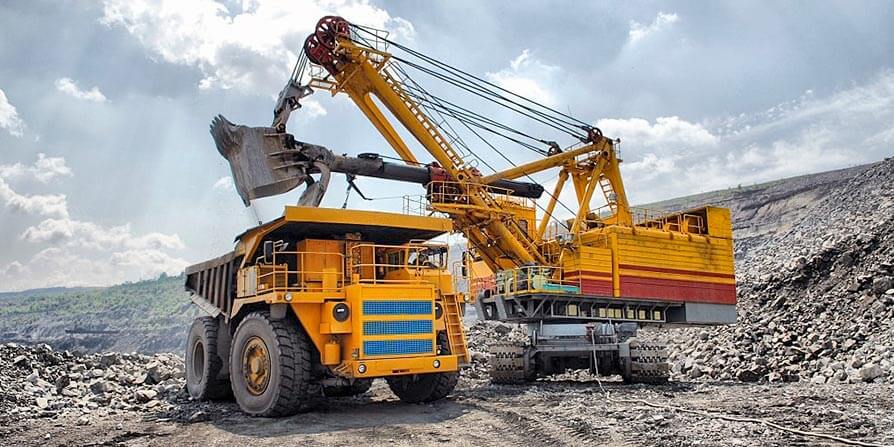
صنایع معدنی؛ کشف و استخراج سنگ آهن
زنجیره فولاد در کشور ابتدا از اکتشاف و استخراج سنگ آهن شروع شده و پس از آن به واحدهای فولادسازی و ذوبآهن رسیده. در مرحله آخر، جهتِ استفاده در صنایع مختلف به واحدهای نوردکاری انتقال داده خواهد شد.
تعیین قیمت منصفانه خرید سنگ آهن و تخصیص یارانه از سوی دولت به صنایع معدنی، میتواند معدنکاران را در ارائه هرچه بهتر محصولات یاری بخشد. اقدامات غیرکارشناسانه در این بخش طی چند دهه اخیر، ضربهای مهلک به تولید صنایع فولادی کشور وارد کرده است. سنگ آهن از دل معادن توسط معدنکاران با هزینههای کلان استخراج میشود، اما به دلیل نبود بازار پررونق در داخل کشور، مجبور میشوند محصولات خود را پایینتر از ارزش واقعی خود به فروش برسانند.
صنایع معدنی و بورس
با ارائه محصولات معدنی در بورس، میتوان قیمت واقعی آنها را مشخص کرد. تمام بخشهای دخیل در زنجیره فولادی برای رسیدن به قیمتهای واقعی بایستی در بورس ارائه شوند. قیمتگذاری کل زنجیره فولاد به محصول پایانی، نمیتواند برای واحدهای معدنی توجیه اقتصادی داشته باشد.
اگرچه در دهههای اخیر، دولت با تدوین قوانین اصلاح شده به مدد زنجیره فولاد آمده، اما با قیمتگذاری دستوری در این شیوهنامه، صنایع معدنی را با خطر ورشکستگی مواجه کرده است. در ایران کارخانجات فولاد، مواد اولیه خود از جمله سنگ آهن را 50 درصد ارزانتر از نرخ جهانی، از معادن خریداری میکنند. این در حالی است که محصولات نهایی این واحدها، به قیمتهای بالاتر در بورس به صنایع دیگر فروخته میشود.
صنایع معدنی در چشمانداز ایرانِ 1404
برای دستیابی به افق 1404 در صنعت فولاد، نیاز به تولید 160 میلیون تن سنگ آهن به صورت سالانه است. از اینرو برای تشویق افراد جهت سرمایهگذاری در این بخش، باید تمهیداتی از سوی دولت اتخاذ گردد.
شناخت نیازهای معادن و کاهش هزینههای جاری آنها در تولید سنگ آهن در دستورالعملهای دولت قرار گرفته است. این بخش با تولید روزافزون خود میتواند کمک قابل توجهی به تکمیل زنجیره فولاد در داخل کشور کند.
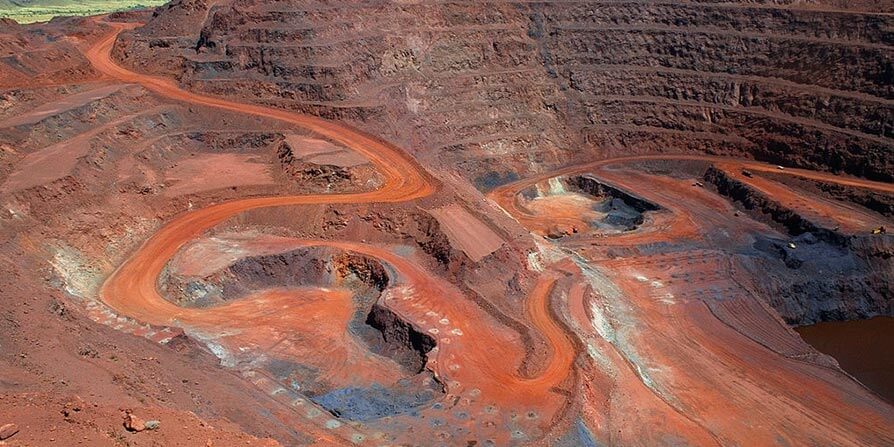
نگاه به زنجیره فولاد از اولین بخش
همانطور که قبلا نیز اشاره شد، صنایع معدنی از ارکان اولیهی تکمیل زنجیره فولادی است. از اینرو توجه به نیازهای این بخش از الزامات صنعت فلز کشور میباشد. در این بخش به اختصار، نیازهای معادن را ذکر میکنیم:
- بهبود زیرساختها و سهولت در جابجایی مواد اولیه به واحدهای دیگر
- قیمتگذاری به صورت آزاد، با توجه به هزینههای بالای استخراج
- رفع تنشهای موجود در بازار فولاد از جمله افزایش صادرات خامفروشی
- افزایش دسترسی مستقیم صنایع پایین دستی و حذف دلالان
- سرازیر کردن سرمایه به واحدهای معدنی
مهمترین صنایع معدنی کشور
در سال 2020، نام بیش از 65 کشور در تولید فولاد به چشم میخورد. ایران با تولید بیش از 26 میلیون تن فولاد رتبه دهم را در جدول تولیدکنندگان انبوه داراست. در زیر به مهمترین قطبهای تولید فولاد در کشور خواهیم پرداخت.
- مبارکه اصفهان: این مجتمع عظیم در سال 1371 شروع به کار کرد. ساخت این واحد فولادی بیش از ده سال به طول انجامید. در حال حاضر تولید فولاد در این مرکز بیش از 2.3 میلیون تن در سال است. گروه مبارکه فولاد اصفهان تمامی حلقههای زنجیره تولید فولاد از سنگ آهن تا محصول پایانی را در خود جای داده است.
- شرکت فولاد خوزستان: این مجتمع در سال 1368 در پایان جنگ، پس از 15 سال به بهرهبرداری رسید. بیش از 50 درصد از محصولات فولاد خوزستان که عمدتا شمش فولاد هستند به کشورهای دیگر صادر میشود. این مجتمع نیز تمامی مراحل زنجیره فولاد را در خود دارد که از این حیث، بعد از شرکت فولاد مبارکه قرار میگیرد.
فولادسازان؛ واحد میانی در زنجیره فولاد
دغدغه اصلی این واحد میانی، نبود سنگ آهن و یا قیمت بالای آن است. ایجاد توازن در عرضه سنگ آهن توسط صنایع معدنی و توجیه اقتصادی برای تولید مصنوعات فولادی از وظایف دیگر دولت است. فولادسازان برای ادامه حیات خود نباید از کمبود سنگ آهن در دپوهای خود رنج ببرند. بهدلیل آنکه سنگ آهن بهصورت خام با ناخالصیهای زیادی مواجه است، تبدیل آن به فلز خالصتر ملزم به ایجاد تغییراتی در آن است.
فولادسازی؛ تبدیل سنگ آهن به فولاد
یکی از روشهای اولیه برای تولید فولاد، دمیدن اکسیژن به درون آهن است. در این روش با کاهش سطح کربنِ فلز آهنچدن، فولاد تهیه میشود. کوره قوس الکتریکی از پیشرفتهترین روشهای تولید فولاد از آهن و چدن است. در این روش آهن توسط دمای حاصل از قوس الکتریکی (نوعی تخلیه الکتریکی در محیط)، ذوب میشود و پس از جداسازی عناصر اضافه و دمیدن اکسیژن خالص به آن، فولاد تهیه میشود.
روشهای نوین تولید فولاد
روش کوره قوس الکتریکی برای تولید فولاد بسیار وقتگیر است. روشهای نوینی جایگزین این کورهها شدهاند که روند ساخت فولاد از آهن را سریعتر کرده. در یک روش، سنگ آهن پس از رسیدن به دمای ذوب، وارد یک پاتیل میشود. تمامی ِ مراحل بعدی تولید فولاد مرغوب در این پاتیل شکل میگیرد. برای افزودن عناصر آلیاژی و حفاظت از فولاد و پاتیل، بایستی دمای ذوب را کاهش داد.
از مراحل اصلی تولید فولاد با این روش در پایین اشاره کردهایم:
- همسانسازی محتویات و دمای پاتیل
- افزودن عناصر به صورت تدریجی
- حذف گوگرد، نیتروژن و هیدروژن
- تولید فولاد درجه یک و صیقلی از لحاظ اكسيده و سولفاته
فولادسازان داخلی
برای تکمیل نمودن زنجیره فولاد در داخل کشور، کارخانجات فولادی متعددی با سرمایهگذاری دولتی و بخش خصوصی احداث شدهاند. تولید فولاد مرغوب در داخل کشور، توسط چهار قطب اصلی (ذوب آهن اصفهان، مبارکه، نیشابور و خوزستان) صورت میگیرد. در ادامه به شرح مختصری از مجتمع ذوب آهن اصفهان و شرکت فولاد نیشابور خواهیم پرداخت.
- شرکت ذوب آهن اصفهان: این شرکت از بزرگترین تولیدکنندگان فولاد در خاورمیانه است. این مجتمع با کمک دولت شوروی سابق در سال 1344 احداث شد. شرکت ذوب آهن اصفهان در 45 کیلومتری این شهر در دشت وسیع طبس قرار گرفته است. به دلیل مرغوب بودن محصولات ذوب آهن اصفهان، از آنها در ساخت پروژههای حساسی مانند برج میلاد، نیروگاه هستهای بوشهر و سدهای بزرگ کارون یک و سه استفاده شد.
- کارخانه فولاد نیشابور خراسان: از ویژگیهای این کارخانه میتوان به تولید 550 هزار تن نورد ساختمانی و 630 هزار تن فولاد به صورت بیلت اشاره کرد.
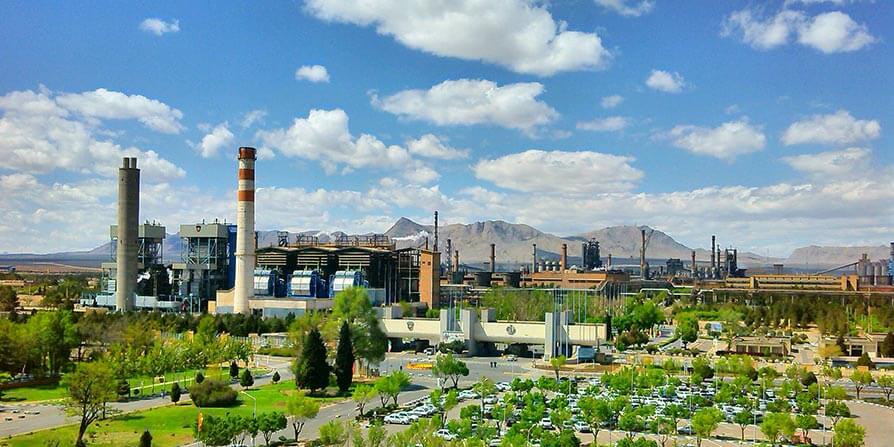
نوردسازان، تکمیل کننده زنجیره فولاد
به شکل دهی فلز به دو طریق گرم و سرد، نورد فلز گفته میشود. نورد گرم در کورههایی که توان تولید دمای بالا را دارند انجام میگیرد. نورد سرد توسط اعمال فشار به فلز از طریق دو غلتک در دمای معمولی محیط صورت میپذیرد.
وجود کارخانجات نورد در کنار مجتمههای تولید فولاد از اهمیت بالایی برخوردار است. سالانه میلیونها تن فولاد خام برای نورد وارد کشور میشود که این خود از اهمیت واحدهای نورد ایران حکایت میکند. با ساخت و تجهیز نمودن نوردسازان داخلی، میتوان از هدر رفت منابع ارزی جلوگیری نمود.
اهمیت نورد در صنایع فولاد
برای استفاده راحتتر از فولاد، به نوردهای گرم و سرد احتیاج است. فلز در این مرحله به اشکال مختلف، با ابعاد مشخصی که هر یک دارای ویژگیهای خود هستند، تبدیل میشوند. برای مثال در ساخت یک آسمانخراش یک نوع فولاد و برای تولید بدنهی انواع خودرو یک نوع دیگر استفاده میشود. از این رو به چند ویژگی و اهمیت واحد نورد به عنوان آخرین بخش از زنجیره فولاد خواهیم پرداخت:
- ساخت فولاد در اشکال مختلف
- افزایش مقاومت فولاد در برابر دما و ساییدگی
- ایجاد سطحی صاف و صیقلی برای مصارف گوناگون
- کاهش وزن فولاد و آسانی در حمل و نقل
نوردکاران داخلی
در سالهای اخیر توجه ویژهای به نوردکاران شده است که باعث رونق گرفتنِ این بخش از تولید فولاد در کشور گشته. نوردکاران متعددی در سطح کشور در حال فعالیت هستند که تعدادی از آنها را نام خواهیم برد:
- نوردسازان: کارخانه نورد سازان در سال 1379 برای رفع نیازهای کشور تاسیس شد. نورد سرد و گرم در این کارخانه انجام میگیرد.
- نوردکاران فولاد غرب: این شرکت در سال 1381 در شهر تبریز شروع به فعالیت کرد. از محصولات این مجموعه میتوان به کانکس، خانههای پیشساخته و ورقهای سقف شیروانی اشاره کرد.
- نوردکاران ساوه: این مجموعه در سال 1354 راه اندازی شد. هدف اولیه کارخانه تولید انواع لوله و پروفیلهای فولادی با توان تولیدی 50 هزار تن در سال بود.
سخن پایانی
در این مطلب سعی کردیم سه بخش اصلی مرتبط با زنجیره فولاد؛ صنایع معدنی، فولادسازان و نوردکاران را به شما خواننده گرامی معرفی کنیم. با توجه به افزایش نیاز جامعه به صنایع فلزی از جمله فولاد، روند ساخت و تولید نیز دستخوش تغییراتی شده است. کشف و پردازش اولیهی سنگ آهن توسط صنایع معدنی صورت میپذیرد. سپس واحد میانی یعنی فولادسازان، آنرا به فلزی با خلوص بالاتر تبدیل کرده که در نهایت توسط نوردکاران به اشکال مختلف تبدیل خواهند شد. برای بازدهی هر چه بهتر، تمامی این سه بخش از زنجیره باید همکاری لازم را با یکدیگر داشته باشند و نقص در هر یک از بخشها، زنجیره فولاد را با مشکلاتی جدی روبهرو خواهد کرد.