برای به هم وصلکردن قطعات فلزی از ترفندهای مختلفی استفاده میشود. جوشکاری یکی از روشهای اتصال قطعات فلزی به کمک حرارت، فشار یا ترکیبی از حرارت و فشار است.
در این مقاله قصد داریم راجعبه انواع جوشکاری در صنعت ساختمان صحبت کنیم. برای آشنایی با انواع جوش در جوشکاری و تصاویر مربوط به انواع جوش تا انتهای مقاله همراه ما باشید.
فهرست مطالب
لازمه فرآیند جوشکاری منبع ایجاد گرما یا فشار، فلز پایه و فلز پرکننده است که با توجه به تعداد این عوامل روشهای مختلفی را برای جوشکاری در صنعت ساختمان به کار میگیرند. در زیر انواع جوشکاری را معرفی خواهیم کرد:
انواع روشهای جوشکاری
فرآیند جوشکاری به سه روش زیر انجام میشود. هر کدام از این روشها طبق شرایط لازم مورد استفاده قرار میگیرند:
- جوشکاری دستی؛
- جوشکاری نیمه خودکار؛
- جوشکاری خودکار؛
- جوشکاری فورجینگ.
البته روش جوشکاری از نظر نوع جریان جوشکاری هم به دو دسته زیر تقسیم میشود:
- جوشکاری با جریان مستقیم (یکسو)؛
- جوشکاری با جریان متناوب.
جوشکاری دستی
جوشکاری دستی یکی از انواع روشهای متداول جوشکاری در صنعت ساختمانسازی بوده و جوش قوس الکتریکی یکی از انواع رایج آن است.
اتصال دو لبه فلز پایه در جوشکاری قوس الکتریکی با استفاده از مذاب حاصل از ذوب شدن بخشی از فلز پایه و فلز پر کننده (الکترود) که به واسطه ایجاد قوس الکتریکی مابین الکترود و فلز پایه انجام میشود، صورت می گیرد. ترکیب و سرد شدن این دو فلز مذاب در حوضچه مذاب سبب اتصال دو لبه فلز پایه میشود.
لازم به ذکر است که در این روش از الکترود روکشدار استفاده میشود که روکش آن در حین جوشکاری ذوب شده و پس از سرد شدن بهصورت لایهای روی نوار جوش باقی میماند، وجود این لایه از اکسیداسیون نوار جوش و سردشدن سریع آن که میتواند ایجاد عیوب جوشکاری نظیر ترک شود، جلوگیری میکند.
جوشکاری خودکار و نیمه خودکار
فرآیندهای جوشکاری خودکار و نیمه خودکار نیز شامل جوش زیر پودری (SAW)، جوش تحت حفاظت گاز (GMAW)، جوش تحت حفاظت گاز با الکترود مصرفی (MIG)، جوش تحت حفاظت گاز با الکترود تنگستن (TIG)، جوش تحت حفاظت گاز با الکترود توپودری (FCAW)، جوش گاز الکتریکی (EGW)، جوشکاری سرباره الکتریکی (ESW) است.
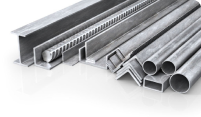
لیست قیمت تمامی مقاطع فولادی در بازار امروز
روش فورجینگ برای جوشکاری میلگرد
جوش خمیری که با نام جوش فورجینگ نیز شناخته میشود در صنعت ساختمان اغلب برای جوشکاری میلگردها مورد استفاده قرار میگیرد. در این روش دو سر میلگرد را که هرکدام به قطبی از مواد متصل شده، به یکدیگر نزدیک میکنند.
در این حین با برقراری قوس الکتریکی مابین دو میلگرد، دو سر میلگرد به دمای خمیری شدن میرسند و همزمان با این عمل دو سر مقطع به سمت هم فشار داده شده و فرایند جوشکاری انجام میشود.
وضعیت جوشکاری
بسته به نوع قرارگیری الکترود و قطعه مورد جوش چهار وضعیت جوشکاری حاصل میشود که شامل موارد زیر است:
۱-وضعیت تخت یا کفی (که با علامت IF در جوش گوشه و IG در جوش شیاری نشان داده میشود)؛
۲-وضعیت افقی (که با علامت 2F در جوش گوشه و 2G در جوش شیاری نشان داده میشود)؛
۳-وضعیت سربالا (که با علامت 3F در جوش گوشه و 3G در جوش شیاری نشان داده می شود)؛
۴-وضعیت سقفی (که با علامت 4F در جوش گوشه و 4G در جوش شیاری نشان داده می شود).
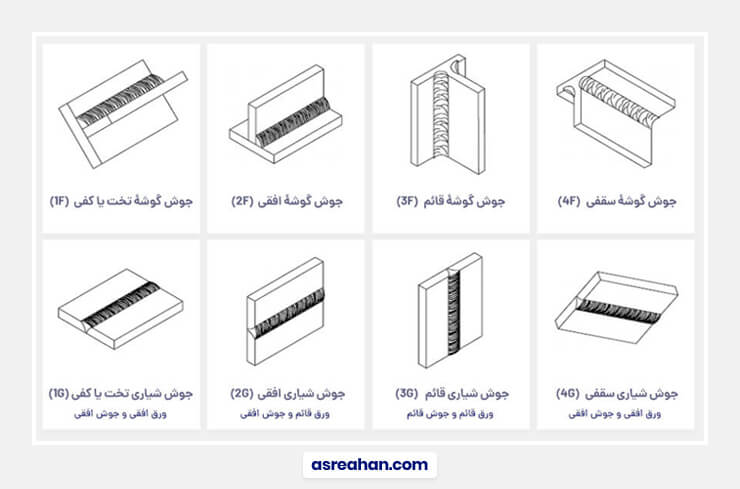
انواع اتصالات جوش
انوع اتصال جوش عبارتند از وضعیت قرارگیری قطعات فلز پایه که در انواع اتصال لب به لب، اتصال پوششی (روی هم)، اتصال سپری، اتصال گونیا و اتصال پیشانی تقسیم بندی میشوند.
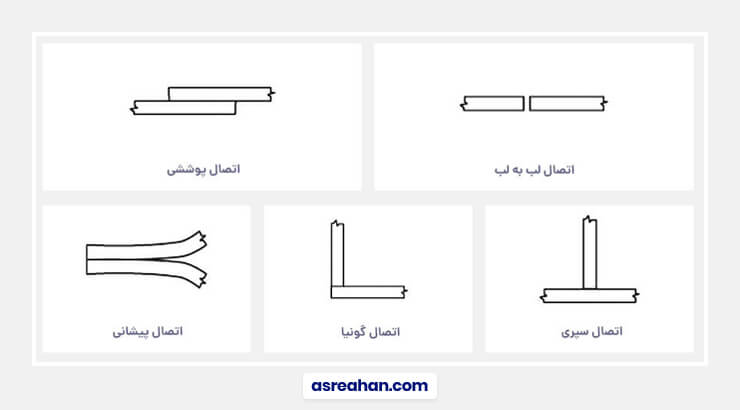
انواع جوش در صنعت ساختمان
انواع جوش شامل جوش شیاری، جوش گوشه، جوش کام و جوش انگشتانه است که جوش شیاری و جوش گوشه از انواع جوشهای رایج در صنعت ساختمان است.
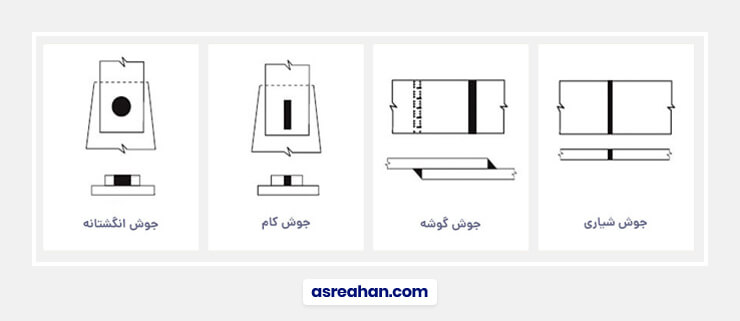
در جوش گوشه که یکی از متداولترین انواع جوش در جوشکاری و صنعت ساختمان است از اتصال سپری روی هم و اتصال گونیا استفاده میشود.
لازم به ذکر است که در اتصالات نبشیها، بادبندها و ورقهای بند از جوش گوشه استفاده میشود. جوش گوشه در مواردی که قطعه تحت تنشهای برشی قرار دارد، مورد استفاده قرار میگیرد.
جوش شیاری نیز یکی دیگر از انواع جوشهای رایج در صنعت ساختمان است که برای یکسره کردن ورقها، ساخت تیر ورقها، ستونهای ورقی، اتصالات صلب تیر به ستون و اتصال ورقهای زیرسری و روسری به ستون مورد استفاده قرار میگیرد.
لازم به ذکر است که جوش گوشه در موارد که قطعه فولادی تحت تنش قائم است مورد استفاده قرار میگیرد؛ همچنین در این روش لبههای جوش جهت نفوذ کامل باید آماده گردند.
انواع روشهای آمادهسازی لبهها در شکل زیر ارائه شده است که اغلب از درز ساده و درز جناغی در صنعت ساختمان استفاده میشود.
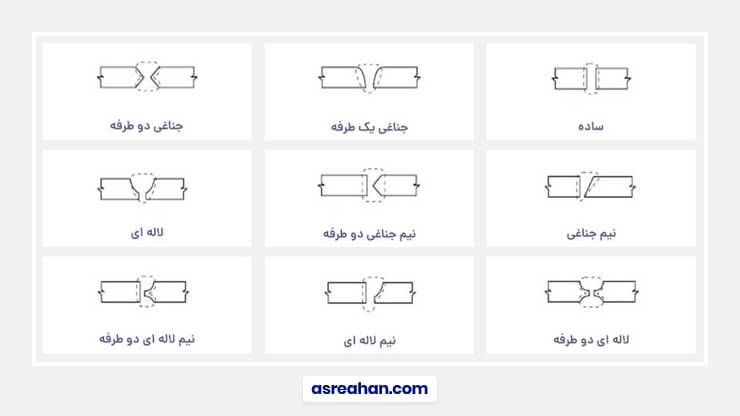
کاربرد انواع جوش در ساختمان
جوش گوشه بیشترین کاربرد را در ساختمان دارد. اغلب اتصالات شامل اتصالات نبشیها، مهاربندها، ورقهای مهاربندی توسط جوش گوشه انجام میشود.
اصولاً جوش گوشه باید طوری آرایش داده شود که تحت تنش برشی قرار داده شود. جوش گوشه نباید تحت تنشهای قائم قرار گیرد.
از جوش شیاری برای یکسره کردن ورقها برای ساخت تیرورقها و ستونهای ورقی و همچنین در اتصالات صلب تیر به ستون برای اتصال ورقهای زیرسری و روسری به ستون استفاده میشود.
از جوشهای شیاری در مواقعی که جوش تحت تنشهای قائم قرار دارد، استفاده میشود.
جوشپذیری فولاد
جوش پذیری در فولادهای ساختمانی به معنای جوش سالم و بدون ترک است و چون حوضچه جوش شامل ترکیبات الکترود و فلز پایه است، تعیین ترکیب فلز پایه و فلز جوش از اهمیت بالایی برخوردار است.
بر این اساس حدود متعارف آلیاژهای موجود در فلز پایه در جدول زیر ارائه شده است و فولادهایی که میزان عناصر آلیاژی آنها بیشتر از مقادیر درج شده در جدول باشد نیازمند الکترود و دستور عملهای خاص جهت جوشکاری هستند.
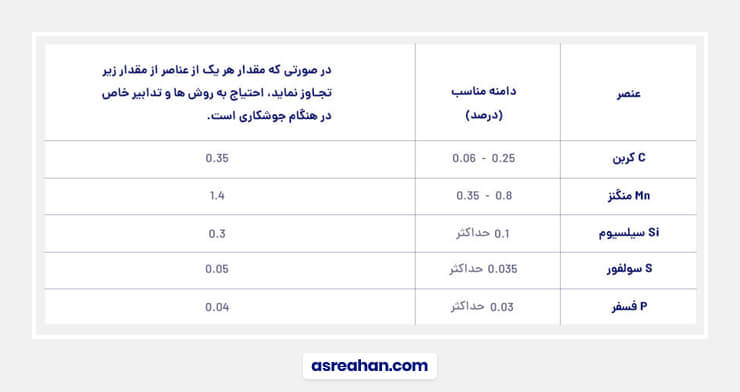
حدود مناسب آلیاژهای فولادی برای قابلیت جوشکاری مناسب برای جلوگیری از وقوع ترک در جوشکاری رعایت موارد زیر الزامی است:
- انتخاب دستورالعمل جوشکاری مناسب،
- کاهش گیرداری درز با تعبیه فاصله مناسب مابین دو لبه اتصال،
- استفاده از مصالح جوش کم هیدروژن،
- کنترل سرعت انجماد با استفاده از کاهش جریان الکتریکی، کاهش سرعت جوشکاری،
- پیش گرمایش، پس گرمایش و کنترل دما در پاسهای میانی.
بخوانید: جوشکاری میلگرد و هر آنچه که باید درباره آن بدانید
ترکخوردگی جوش
ترکخوردگی جوش یکی از عواملی است که نباید از آن چشمپوشی کرد. با استفاده از طرح خوب و انتخاب دستورالعمل جوشکاری مناسب، از این پدیده میتوان جلوگیری نمود. انواع ترکهای محتمل در جوشکاری عبارتند از:
- ترک در نوار جوش (به صورت ظاهری و داخلی)؛
- ترک در منطقهای از فلز پایه که در اثر دمایجوش و تغییر حالت متالورژیکی فلز پایه به وجود می آید که به آن تفتیده نیز گفته میشود (ترک در زیر نوار جوش)؛
- ترک در جوش در هنگام بهرهبرداری (ترک مقاومتی).
عوامل ایجاد ترک در نوار جوش چیست؟
ترک در نوار جوش بر اساس موارد زیر بهوجود میآید:
- گیرداری درز که سبب ایجاد تنشهای انقباضی میشود
- وجود آلودگی در اتصال
- کافی نبودن میزان پوششدهی پودر
- گیرافتادن پودر در زیر اتصال
- سرعت حرکت زیاد
- باقی ماندن سرباره خال جوشهای قبلی که با الکترود روکشدار انجام شده است
- هندسه مقطع نوار جوش؛ همان طور که میدانیم حوضچۀ جوش در هنگام سردشدن تمایل به انقباض دارد که سبب ایجاد کششهای چند محوری میشود. نوار جوش با سطح محدب یا برآمده توانایی مقابله با کششهای دو محوری را دارد ولی در نوار جوش مقعر کششهای عرضی سبب ایجاد ترک طولی در نوار جوش میشوند؛ همچنین در نوار جوش با عمق بالا و عرض کم احتمال ایجاد ترکهای داخلی زیاد است
- میزان کربن موجود در فلز پایه؛ هرچه میزان کربن در فلز پایه بیشتر باشد شکلپذیری فلز کمتر و در نتیجه احتمال وقوع ترک بیشتر میشود
- ورود حبابهای هیدروژن از الکترود به نوار جوش
- وجود رطوبت در سطح شیار فلز پایه
- سردشدن سریع جوش
عوامل ایجاد ترک در ناحیه تفتیده فلز پایه (ترک در زیر نوار جوش) عبارتند از:
- میزان کربن بالا در فلز پایه که باعث افزایش قابلیت سختشدگی و کاهش انعطاف ناحیه تفتیده میشود؛
- ورود هیدروژن از الکترود و در نتیجه ایجاد تردی هیدروژنی در ناحیه تفتیده؛
- سرعت سرد شدن.
عواملی که سبب ایجاد ترک در جوش در هنگام بهرهبرداری (ترک مقاومتی) میشوند عبارتند از:
- تردبودن نوار جوش یا قسمت تفتیده فلز پایه که سبب شکست این نواحی تحت تنشهای ضربهای در دمای پایین میشود؛
- ترک خستگی که ناشی از هندسه نامناسب درز است، این نوع ترک تحت بارهای سیکلی با دامنۀ بزرگ بهوجود میآید؛
- هندسه نوار: نوار جوش باید بهصورت محدب باشد و نسبت بین عمق جوش و عرض آن رعایت شود؛
- گیرداری درز؛
- میزان کربن و آلیاژها.
عواملی که باید کنترل گردند:
هندسه نوار: سطح نوار جوش باید قدری محدب بوده و دارای نسبت عرض به عمق مناسب باشد. این مسئله باید در جوشهای یک پاسه و جوش ریشه در جوشهای چند پاسه یا حتی پاسهای میانی مورد توجه قرار گیرد.
گیرداری درز: در هنگام طراحی و اجرا باید گیرداری درز را به حداقل رساند.
میزان کربن و آلیاژها: در هنگام انتخاب نوع فولاد باید دقت گردد که موازنهای بین هزینه فولاد و هزینه جوش برقرار گردد.
انتخاب فولادهای پرمقاومت هرچند که باعث کاهش هزینه فولاد میگردد، لیکن به علت وجود میزان کربن زیاد یا آلیاژها و بهخصوص عناصری مثل سولفور یا فسفر که تأثیر منفی بر کیفیت جوش دارند، افزایش قابل توجهی در هزینه جوشکاری وجود خواهد داشت. این دو هزینه باید قابل موازنه باشد.
واردشدن هیدروژن: برای جلوگیری از ورود حبابهای هیدروژن باید از الکترودهای کمهیدروژن استفاده گردد.
حرارت ورودی: باید کل حرارت ورودی کنترل گردد. این حرارت شامل پیشگرمایش، حرارت القایی به واسطۀ جوشکاری، گرمایش در حد فاصل پاسهای مختلف و پس گرمایش به منظور جلوگیری از سردشدن سریع است. حرارت القایی کمتر، باعث کاهش تنشهای انقباضی و کاهش سرعت سردشدن (که از تردی ناحیه تفتیده میکاهد) میگردد. این دو از عوامل مهم بروز ترک در جوش هستند.
سخن آخر
در این مقاله سعی کردیم دربارۀ جوشکاری در صنعت ساختمان و انواع جوش در جوشکاری صحبت کنیم. اگر سؤالی در این زمینه داشتید از بخش «ارسال دیدگاه» با ما در میان بگذارید تا در اسرع وقت به آن پاسخ دهیم.
سؤالات متداول
انواع جوش فلزات بهصورت جوشکاری دستی، جوشکاری خودکار و نیمه خودکار و جوشکاری فورجینگ انجام میشود.
انواع جوش در جوشکاری از نظر اتصال، اتصال لب به لب، اتصال پوششی (روی هم)، اتصال سپری، اتصال گونیا و اتصال پیشانی است. انواع جوشکاری با تصویر در داخل مقاله، توضیح داده شده است.