نورد گرم یکی از مهمترین فرآیندهای تولید میلگرد است که در دمایی بالاتر از دمای تبلور فلز صورت میگیرد. در این روش، فلز تا دمای بالا حرارت داده شده و سپس از میان غلتک عبور میکند تا به شکل و ابعاد مورد نظر برسد.
اما این فرآیند چگونه انجام میشود؟ چه تجهیزاتی در آن نقش دارند؟ و چه تفاوتی با روشهای دیگر دارد؟ در این مقاله، علاوه بر بررسی تاریخچه و مراحل نورد گرم، به معرفی دستگاهها و تجهیزات مورد استفاده، دمای مورد نیاز، فرآیند تابکاری، مزایا و معایب این روش و همچنین کاربردهای آن در صنایع مختلف میپردازیم.
نورد گرم چیست؟
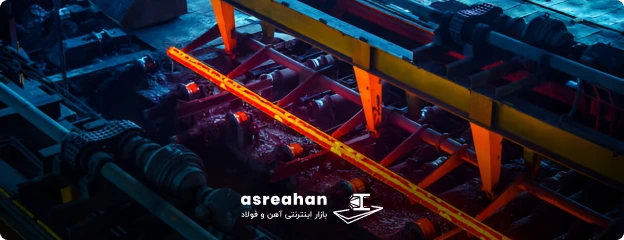
نورد گرم یکی از اصلیترین روشها برای تولید مقاطع فولادی مانند میلگرد است که بهدلیل تاثیر آن بر ساختار و خواص فلز، در صنایع مختلف کاربرد گستردهای دارد. در این فرآیند شمشهای فولادی در دمای بسیار بالا، معمولاً بین ۵۰۰ تا ۱۰۰۰ درجه سانتیگراد، حرارت داده میشوند تا قابلیت شکلدهی پیدا کنند. این دما باعث کاهش تنشهای داخلی و افزایش شکلپذیری فولاد میشود.
در فرآیند نورد میلگرد، فلز از بین دو غلتک با فاصلهای کمتر از ضخامت اولیهاش عبور میکند. غلتکها در جهتهای مخالف چرخش دارند و سرعت چرخش آنها بیشتر از سرعت حرکت فلز بر روی سطحی است که فلز روی آن قرار دارد. این حرکت، اصطکاک ایجاد کرده و باعث میشود که فلز به جلو رانده شود. به این ترتیب، طول فلز افزایش یافته و ضخامت آن کاهش مییابد. این فرآیند نهتنها به بهبود ویژگیهای مکانیکی فلز کمک میکند، بلکه از مهمترین روشها برای تولید مقاطع یکنواخت و باکیفیت در صنعت فولاد است.
بررسی تاریخچه نورد گرم
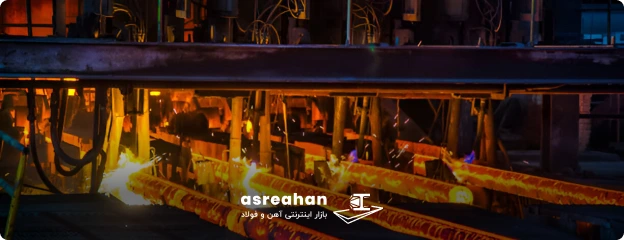
نورد گرم یکی از قدیمیترین روشهای شکلدهی فلزات است که از گذشتههای دور برای کاهش ضخامت و تغییر شکل فلزات مورد استفاده قرار میگرفته است. تحقیقات نشان میدهند که نورد گرم در قرن هفدهم میلادی آغاز شد. در آن زمان، این فرآیند با استفاده از دو غلتک چدنی انجام میشد که با عبور فلزاتی مانند سرب و قلع از بین آنها، سطح مقطع کاهش مییافت.
با گذر زمان، استفاده از غلتکهای بزرگتر برای بهبود راندمان این روش متداول شد. در ابتدا، این غلتک نورد گرم با نیروی اسب یا پرههای آبی به حرکت درمیآمد. در همان دوره، برای افزایش دقت و کنترل بیشتر بر فرآیند نورد، شیارهایی روی غلتکها ایجاد شد تا شکلدهی بهتری انجام شود.
در ادامه، با توسعه فناوری و افزایش نیاز به تولید انبوه، از غلتکهای کوچکتر که توسط غلتکهای بزرگتر به حرکت درمیآمدند، استفاده شد و به این ترتیب قفسههای چهار غلتکه به وجود آمدند.
یکی از مهمترین تحولات در صنعت نورد، اختراع ماشین بخار در قرن هجدهم بود که محدودیتهای نیروی محرکه را از بین برد و امکان استفاده از ماشینهای نورد قدرتمندتر برای تغییر شکل شمشهای فلزی را فراهم کرد. با صنعتی شدن فرآیند نورد و پیشرفت تکنولوژی، این روش جایگزین بسیاری از روشهای سنتی مانند آهنگری و ریختهگری شد.
مراحل نورد گرم
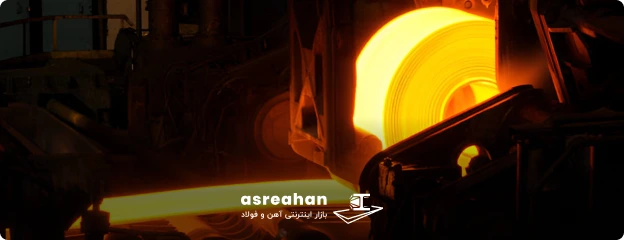
نورد گرم شامل مراحل مختلفی است که طی آن، شمش یا بیلت فولادی به اشکال مختلف مانند ورق، میلگرد، لوله یا مقاطع دیگر تبدیل میشود. تفاوت اصلی نورد گرم با نورد سرد در دمای عملیات است؛ در نورد گرم، فلز در دمای بالا شکلدهی میشود که این امر به فولاد اجازه میدهد تا با کمترین ترکخوردگی و تغییرات ساختاری، به شکلهای مورد نظر درآید.
در حالی که نورد سرد در دمای محیط انجام میشود و معمولاً برای تولید محصولاتی با دقت بالا و سطح صافتر استفاده میگردد. فرآیند نورد گرم شامل چند مرحله کلیدی است که در ادامه به بررسی آنها خواهیم پرداخت:
آماده سازی مواد
در مرحله نخست، ابتدا مواد فلزی مورد نیاز برای عملیات نورد گرم انتخاب میشوند. این مواد معمولاً شامل فولاد، مس یا آلومینیوم هستند که بهصورت شمشها یا بیلتهای بزرگ تهیه شده و آماده حرارتدهی میشوند. انتخاب دقیق این مواد از اهمیت بالایی برخوردار است، زیرا کیفیت نهایی محصول بستگی به ویژگیهای ماده اولیه دارد.
گرم کردن و آمادهسازی مواد
در فرآیند نورد گرم، ابتدا مواد اولیه باید به به دمای بالاتر از نقطه تبلور مجدد برسند تا بتوانند به راحتی از میان غلتکها عبور کنند. دمای نورد گرم معمولاً بین ۵۰۰ تا ۱۰۰۰ درجه سلسیوس است، که بستگی به نوع و ویژگیهای ماده دارد.
گرم کردن مواد در کورههای پیش گرم کن انجام میشود که قادر به تأمین حرارت یکنواخت و کنترل شده برای آمادهسازی مواد هستند. این مرحله نه تنها به تسهیل فرایند نورد کمک میکند بلکه باعث بهبود خواص مکانیکی و انعطافپذیری فولاد میشود، که برای شکلدهی بهتر در مراحل بعدی ضروری است.
پوسته زدایی
در مرحله پوسته زدایی، هدف اصلی از بین بردن لایههای اکسیدی و زنگزدهای است که در اثر تماس فلز با دماهای بالا در فرآیند نورد گرم روی سطح فولاد ایجاد میشود. این پوستهها میتوانند تأثیرات منفی زیادی بر کیفیت نهایی محصول بگذارند.
انجام عملیات نورد
برای نورد کردن شمشها یا بیلتهای فولادی که پوستهزدایی شدهاند، از استند نورد استفاده میشود. در این فرآیند، شمش یا بیلت گرمشده از میان غلتکهایی که فاصله آنها کمتر از قطر فلز است، عبور داده میشود. این حرکت منجر به تغییر شکل فلز و کاهش ضخامت آن میشود، که محصول را برای مراحل بعدی آماده میسازد.
ضخامت سنجی، تاب گیری و خنک کاری
پس از فرآیند نورد گرم، برای اطمینان از ابعاد دقیق، قطعه فلزی به دقت با استفاده از دستگاه ضخامت سنج اندازهگیری میشود. این دستگاه با دقت بالا ضخامت نوار فولادی را بررسی کرده و از هرگونه نقص در اندازهها جلوگیری میکند.
سپس، برای اصلاح هرگونه تاب یا انحراف در سطح فولاد، قطعه وارد دستگاه تابگیر میشود که این دستگاه با اعمال فشار و حرارت، تابزدایی کرده و قطعه را به حالت یکنواختتری درمیآورد. پس از این مراحل، قطعه فولادی وارد خط خنکسازی میشود. این فرایند، بهویژه در جلوگیری از تغییرات ناخواسته در ساختار میکروسکوپی فولاد و حفظ استحکام و انعطافپذیری آن، بسیار مهم است.
پس از تکمیل فرآیند نورد، محصول نهایی در اندازههای دلخواه برش خورده و بهصورت اتوماتیک رول میشود. لازم به ذکر است که ورقهای تولید شده در این مرحله همان ورقهای سیاه هستند که برای تبدیل به ورقهای سبکتر، باید فرآیند نورد سرد بر روی آنها اعمال گردد. برای اطلاع از آخرین قیمت ورق سیاه، میتوانید به وبسایت عصرآهن مراجعه کنید.
دستگاه و تجهیزات نورد گرم چیست؟
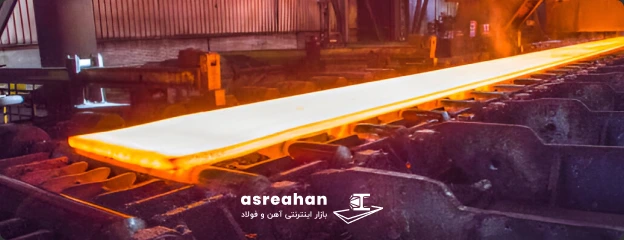
یکی از تجهیزات کلیدی و پرکاربرد در کارخانههای تولید آهن و فولاد، دستگاه نورد گرم است که برای شکلدهی فلزات بهویژه فولاد استفاده میشود. این دستگاه نقش مهمی در تولید محصولات فولادی از جمله میلگرد، تختال، تیرآهن، نبشی و ورقهای فولادی دارد و فرآیند آن تأثیر بسزایی در کیفیت نهایی محصولات ایفا میکند.
نحوه عملکرد این دستگاه به این شکل است که ابتدا، شمشهای فولادی وارد کورههای پیشگرمکننده میشوند که دمای آنها تا حدود ۱۱۰۰ درجه سانتیگراد افزایش مییابد. این حرارت باعث نرم شدن شمشها و آمادهسازی آنها برای تغییر شکل میشود. فرآیند انتقال شمشها به داخل کوره از طریق جکهای هیدرولیکی انجام میگیرد و پس از رسیدن به دمای مورد نظر، شمشها توسط جریانهای گرد آبی بهصورت یکنواخت گرم میشوند.
پس از رسیدن به دمای مناسب، شمشها به واحد غلتکزنی منتقل شده و تحت فشار شدید، شکل و ابعاد آنها تغییر میکند. این تغییرات بهگونهای است که باعث بهبود خواص مکانیکی فلز میشود و محصولی یکنواخت، بدون ترکهای سطحی و با استحکام بالا تولید میگردد.
فرآیند تابکاری نورد گرم چیست و چه مراحلی دارد؟

تابکاری یکی از مراحل کلیدی در فرآیند خط نورد گرم است که به منظور بهبود ساختار متالورژیکی و خواص مکانیکی فولاد انجام میشود. در این فرآیند، فولاد سرد شده را تا دمایی بالاتر از نقطه تبلور مجدد گرم کرده و برای مدت مشخصی در آن دما نگه میدارند. این کار باعث حذف تنشهای داخلی، افزایش چقرمگی، کاهش سختی و بازگردانی خاصیتهای اولیه ماده میشود.
تابکاری معمولاً در کورههای پیوسته و جعبهای انجام میشود و نقش مهمی در افزایش کیفیت نهایی محصولات فولادی دارد. این فرآیند به فولاد قابلیت شکلپذیری بهتر، بهبود قابلیت ماشینکاری و افزایش مقاومت در برابر شکست را میدهد.
تابکاری کامل
تابکاری کامل یک فرآیند حرارتی مهم در نورد گرم است که با هدف بهبود خواص مکانیکی چکشخواری فلز انجام میشود. در این روش، فلز در یک بازه زمانی مشخص و طبق یک برنامه دمایی کنترلشده تا دمای مناسب گرم شده و سپس بهآرامی سرد میشود.
این فرآیند موجب تغییر در ساختار میکروسکوپی فولاد گرم نورد شده و دانهبندی آن را درشتتر و یکنواختتر میکند، در نتیجه، محصول نهایی دارای ساختاری پرلیتی پایدار خواهد بود.
تابکاری هم دمایی
در روش تابکاری همدمایی، فولاد پس از گرم شدن تا دمای مشخص، در یک دمای ثابت نگه داشته میشود تا تغییرات متالورژیکی موردنظر در شرایط پایدار و هم دمایی انجام گیرد. سپس بهصورت کنترلشده و سریعتر از روشهای معمول خنک میشود.
این فرآیند باعث تشکیل ساختاری یکنواخت با دانهبندی ریز و پرلیتی میشود که بهبود خواص مکانیکی مانند استحکام، شکلپذیری و ماشینکاری را به همراه دارد.
تابکاری کروی
تابکاری کروی یکی از مراحل فرآیند تابکاری میلگرد است که هدف آن تبدیل ساختار کاربیدی فولاد به شکل کروی است. در این روش، با استفاده از بازپخت و نرماله کردن فولاد، کربیدهای فولاد از حالت لایهای یا سوزنی به ساختاری کروی تغییر شکل میدهند.
این فرآیند بهدلیل نیاز به نگهداری طولانیمدت فلز در دمای زیر بحرانی، زمان بیشتری نسبت به روشهای دیگر تابکاری دارد. اما نتیجه آن، افزایش نرمی فولاد، بهبود قابلیت ماشینکاری، کاهش سختی و افزایش انعطافپذیری است.
کار گرم
کار گرم یکی از مراحل مهم در نورد گرم فولاد است که در آن ماده فلزی در دمایی بالاتر از دمای تبلور مجدد قرار میگیرد و در نتیجه تغییر شکل پلاستیکی پیدا میکند.
این فرآیند به فلز اجازه میدهد تا بهراحتی و بدون شکستگی، تغییر شکل داده و به ابعاد و اشکال مورد نظر تبدیل شود. به عبارت دیگر، کار گرم فرآیندی است که در آن فلزات در دمای بالا نرم میشوند و تحت فشار یا کشش، تغییر شکلهای مختلفی پیدا میکنند.
دمای مورد نیاز برای فرایند نورد گرم چند درجه است؟
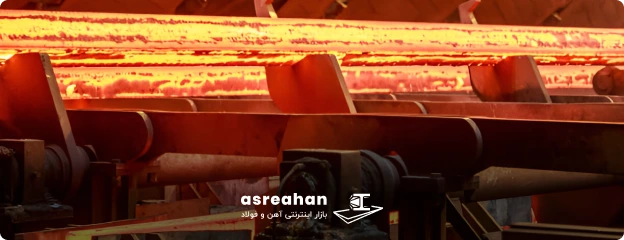
در فرآیند نورد گرم، کنترل دقیق دما امری ضروری است تا به کیفیت مطلوب در محصول نهایی دست یابیم. این امر از طریق افزایش تدریجی و یکنواخت دمای فلز تا میزان مورد نظر انجام میشود. برای دستیابی به این هدف، قطعه فلزی باید در دمای ثابت و مشخص برای مدت زمان معینی نگهداشته شود.
این فرآیند بهگونهای طراحی شده که تغییر شکل یکنواخت قطعه را تضمین کند؛ زیرا اگر دمای قطعه بهطور یکنواخت توزیع نشود، فرآیند نورد به صورت غیر یکنواخت انجام میشود. بهطور مثال، اگر قطعه بهطور همگن گرم نشود، بخشهای گرمتر در سطح بیرونی سریعتر از بخشهای داخلی که سردتر و مقاومتر هستند، تغییر شکل مییابند.
این عدم یکنواختی دما میتواند باعث بروز مشکلاتی مانند ترک و گسیختگی در سطح قطعه شود. بهویژه، زمانی که فلز پس از گرم شدن یا بین مراحل نورد سرد شود، بخشهای سرد نسبت به تغییر شکل مقاومتر خواهند بود. در نتیجه، نواحی داخلی که داغتر و ضعیفتر هستند، در معرض خطر ترک خوردگی و شکست سطحی قرار میگیرند.
برای فولادهای کربنی ساده و فولادهای کمآلیاژ، دمای نورد گرم معمولاً حدود ۱۲۰۰ درجه سانتیگراد در نظر گرفته میشود. مهم است بدانیم که فرآیند نورد گرم معمولاً در دمایی بین ۵۰ تا ۱۰۰ درجه سانتیگراد بالاتر از دمای تبلور خاتمه مییابد. این دمای پایان عملیات نورد، از سخت شدن کرنشی جلوگیری کرده و منجر به ایجاد دانههای ریز و یکنواخت در قطعه میشود که خواص مکانیکی مطلوب را به همراه دارد.
اجزای دستگاه نورد گرم
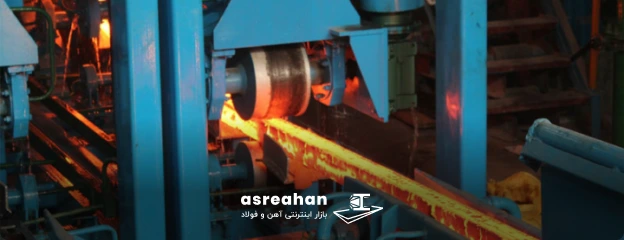
دستگاه نورد گرم از اجزای متعددی تشکیل شده که هر یک نقشی کلیدی در فرآیند تولید محصولات فولادی دارند. در ادامه، مهمترین اجزای این دستگاه را بررسی میکنیم:
- کوره پیشگرمکن: کوره پیشگرمکن وظیفه افزایش دمای شمشالها (بیلت، اسلب یا بلوم) را تا حد مورد نیاز برای نورد بر عهده دارد.
- اجکتور: پس از رسیدن بیلتها به دمای مناسب، اجکتور آنها را از کوره خارج کرده و به بخش نورد هدایت میکند. این مرحله باید با دقت انجام شود تا از افت دمای ناگهانی و آسیب به ساختار فلز جلوگیری شود.
- پوستهزدا: در اثر ریختهگری و کرومکاری مجدد، لایههایی از اکسید آهن (پوسته) روی سطح شمشال تشکیل میشود. پوستهزدا با استفاده از آب پرفشار یا روشهای مکانیکی، این لایهها را حذف کرده و از کاهش کیفیت محصول نهایی جلوگیری میکند.
- استند نورد: استندهای نورد شامل غلتکهای افقی هستند که وظیفه کاهش ضخامت و تغییر ابعاد قطعه را بر عهده دارند. این مرحله اصلیترین بخش فرایند نورد است که با فشار بالا روی فلز اعمال میشود.
- استند اجر: این استند شامل غلتکهای عمودی بوده و برای تنظیم عرض محصول و یکنواختسازی کنارههای ورق استفاده میشود.
- دستگاه ضخامتسنج: در حین فرآیند نورد، ضخامت ورق یا میلگرد بهطور مداوم توسط دستگاه ضخامتسنج کنترل میشود.
- تابگیر: در برخی موارد، محصولات نورد شده دچار تاب و اعوجاج میشوند. دستگاه تابگیر با استفاده از چندین غلتک کوچک، این اعوجاجها را اصلاح کرده و سطح محصول را صاف و یکدست میکند.
- خط خنککاری: پس از عبور از استندهای نورد، محصول باید تحت شرایط کنترلشدهای خنک شود تا خواص مکانیکی و ساختاری آن تثبیت گردد.
- قیچی: قیچی برای برش ابتدا و انتهای محصول، تنظیم اندازه و آمادهسازی ورقها یا میلگردها برای مراحل بعدی بستهبندی و انبارش استفاده میشود.
- دستگاه بستهبندی: دستگاه بستهبندی پس از اتمام فرآیند نورد، محصولات نهایی را وزنکشی، برچسبگذاری و بستهبندی و برای ارسال آماده میکند.
مزایا و معایب نورد گرم چیست؟
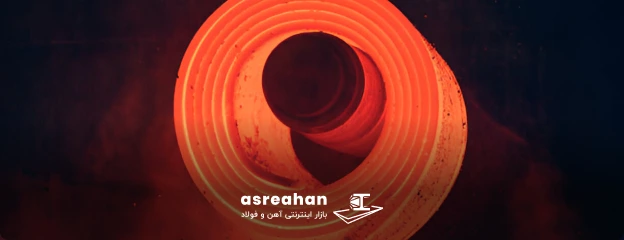
نورد گرم یکی از فرآیندهای کلیدی در تولید فولاد و سایر فلزات است که مزایای متعددی را به همراه دارد. در ادامه، مهمترین مزایا و معایب این روش را مورد بررسی قرار میدهیم.
مزایای نورد گرم
از جمله مهمترین مزایای این روش میتوان به موارد زیر اشاره کرد:
شکل پذیری
نورد گرم به فلزات این امکان را میدهد که در دماهای بالا به راحتی تغییر شکل دهند و چکشخواری شوند. در این فرآیند، دماهای بالا باعث کاهش استحکام فلزات و نرمتر شدن آنها میشود، به طوری که میتوان آنها را به اشکال مختلفی همچون ورقها، صفحات، میلهها و پروفیلها تبدیل کرد.
این ویژگی، علاوه بر تسهیل فرآیند تولید، باعث کاهش نیرو و انرژی مورد نیاز برای تغییر شکل فلزات میشود.
تولید و ساخت اقتصادی
نورد گرم نسبت به نورد سرد از نظر اقتصادی بهصرفهتر است. این مزیت بهویژه به دلیل دمای بالای فرآیند نورد گرم است که بهطور مستقیم موجب کاهش نیروهای مورد نیاز برای تغییر شکل فلزات میشود.
این کاهش نیروها علاوه بر تسهیل فرآیند، به افزایش نرخ تولید و کاهش زمان فرآوری در واحدهای خروجی کمک میکند.
بهبود خواص مکانیکی
فرآیند نورد گرم موجب بهبود قابل توجه خواص مکانیکی آنها نیز میشود. بهبود خواص مکانیکی به دلیل تاثیر دماهای بالا در طی فرآیند نورد گرم است که منجر به تبلور مجدد و رشد دانههای فلز میشود.
این تغییرات ساختاری باعث ایجاد ریزساختارهای تصفیه شده و یکنواخت میشود که در نتیجه آن خواص مکانیکی فلزات بهبود مییابند.
معایب نورد گرم
با وجود مزایای فراوان، نورد گرم معایب و محدودیتهایی نیز دارد. از جمله مشکلات آن میتوان به کاهش دقت ابعادی به دلیل دمای بالای فرآیند، سختی کنترل کیفیت در تولید محصولاتی با خواص مکانیکی دقیق و محدودیت در برخی از آلیاژها اشاره کرد. در ادامه، به بررسی دقیقتر این معایب پرداخته و راهکارهای موجود برای بهینهسازی فرآیند نورد گرم را بررسی خواهیم کرد.
عیوب سطحی
در فرآیند نورد گرم، بهدلیل اعمال حرارت و فشار زیاد، ممکن است رسوبات و لایههای اضافی بر روی سطح فولاد یا میلگرد ایجاد شود که نیاز به پوستهزدایی دارد. این رسوبات میتوانند ناشی از تماس فلز با غلتکها یا تغییرات دمایی ناهموار باشند.
علاوه بر این، در برخی موارد سطح کار ممکن است بهطور کامل صاف و یکنواخت نباشد و اعوجاجهایی در آن مشاهده شود. برای رفع این عیوب، انجام فرآیندهای تکمیلی نظیر پولیشکاری، صافکردن، یا عملیات حرارتی اضافی ضروری است.
عدم دقت ابعادی
نورد گرم به دلیل دمای بالا و تغییر شکل فلز در فرآیند، ممکن است موجب ایجاد اعوجاج شود. این امر باعث میشود دقت ابعادی در نورد گرم نسبت به نورد سرد پایینتر باشد.
در نورد سرد، به دلیل انجام فرآیند در دماهای پایینتر، فلز بهطور دقیقتری شکل میگیرد و محصول نهایی دارای دقت ابعادی بالاتری است. به همین دلیل، در صنایعی که دقت بالا در ابعاد محصول اهمیت زیادی دارد، گاهی از ترکیب نورد گرم و نورد سرد استفاده میشود تا هم استحکام مطلوب حاصل شود و هم دقت ابعادی حفظ گردد.
مصرف انرژی
در فرآیند نورد گرم، برای تغییر شکل فلزات، نیاز است که فلزات در دماهای بسیار بالا حرارت داده شوند. مصرف بالای انرژی در نورد گرم نه تنها هزینههای تولید را افزایش میدهد، بلکه تأثیرات زیستمحیطی قابلتوجهی نیز به همراه دارد.
استفاده گسترده از سوختهای فسیلی برای تأمین این انرژی، موجب انتشار گازهای گلخانهای و آلودگی هوا میشود که اثرات منفی بر سلامت انسان و اکوسیستمها میگذارد.
کاربرد نورد گرم: در چه نوع صنایعی از نورد گرم استفاده میشود؟

فرآیند نورد گرم برای تولید قطعات فلزی با ابعاد مختلف و استحکام بالا مورد استفاده قرار میگیرد. این فرآیند بهویژه در تولید لولهها و پروفیلهای سنگین مانند قوطیهای آهنی و لولههای گاز کاربرد فراوانی دارد. از مهمترین صنایع و کاربردهایی که از نورد گرم بهره میبرند میتوان به موارد زیر اشاره کرد:
ساخت و ساز
فولاد نورد گرم شده، یکی از مواد اصلی و ضروری در پروژههای عمرانی و ساختمانی است که کاربرد گستردهای در تولید اجزای سازهای، تیرها، ستونها، صفحات سنگین و حتی قطعات خاص دارد.
این نوع فولاد به دلیل فرآیند تولید خاص خود، استحکام و دوام بالایی پیدا میکند و از این رو، در ساخت ساختمانها، پلها، جادهها و سایر پروژههای زیربنایی بهطور فراوان استفاده میشود.
صنعت خودرو
در صنایع خودروسازی، فولاد نورد گرم شده بهطور گستردهای برای تولید قطعات کلیدی مانند قابها، شاسیها، چرخها، قطعات موتور و دیگر اجزای بدنه استفاده میشود.
ویژگیهای مهم فولاد نورد گرم، از جمله استحکام بالا، شکلپذیری مطلوب و هزینه مقرونبهصرفه، این روش را به انتخابی ایدهآل برای تولید قطعات خودرو تبدیل کرده است.
کشتی سازی
صفحات فولادی نورد گرم نقش حیاتی و گستردهای در صنعت کشتیسازی ایفا میکنند. این صفحات عمدتاً در ساخت بدنه، عرشه و سایر اجزای ساختاری کشتیها استفاده میشوند.
فرآیند نورد گرم امکان تولید صفحات فولادی با ضخامت بالا و ویژگیهای مکانیکی ممتاز نظیر استحکام و چقرمگی بالا را فراهم میآورد که برای تحمل شرایط سخت دریایی ضروری است.
کارخانه های نورد گرم ایران
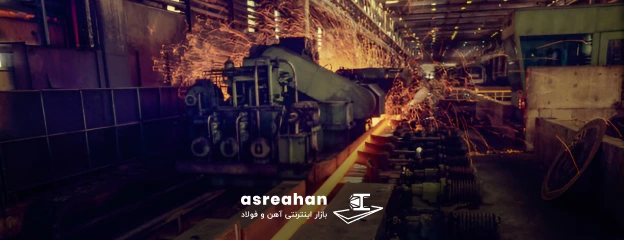
در کشور ما، کارخانههای تولید کننده ورق سیاه، حضوری فعال و تأثیرگذار در بازارهای داخلی و بینالمللی دارند. این کارخانهها با تولید ورقهای سیاه با کیفیت بالا، به یکی از ارکان اصلی صنایع مختلف از جمله ساختمانسازی، خودروسازی، و ماشینآلات صنعتی تبدیل شدهاند. برترین کارخانههای فولادی تولید کننده ورق سیاه در ایران عبارتند از:
- کارخانه فولاد مبارکه اصفهان: اولین و بزرگترین تولیدکننده ورق گرم در ایران است و سهم بزرگی در تأمین نیازهای داخلی و صادرات فولاد کشور دارد.
- مجتمع فولاد سبا: این کارخانه بهعنوان نخستین تولیدکننده ورقهای فولادی ضد زنگ در کشور، در تولید ورقهای با ویژگیهای خاص و مقاوم به خوردگی برای صنایع حساس فعالیت دارد.
- فولاد کاویان اهواز: این کارخانه از سال ۱۳۷۲ در صنعت فولاد فعالیت میکند و یکی از تولیدکنندگان بزرگ ورق گرم در کشور است که نیاز عمده بازار ایران به محصولات فولادی را تأمین میکند.
- شرکت اکسین اهواز: این کارخانه در اهواز یکی از مهمترین تولیدکنندگان فولاد و ورق گرم آلیاژی و محصولات تخصصی دیگر است که در صنایع مختلف مانند نفت، گاز و پتروشیمی کاربرد دارد.
- شرکت فولاد امیرکبیر خزر: این کارخانه یکی از پیشروترین تولیدکنندگان میلگردهای صنعتی و ساختمانی در سایزهای 8 تا 40 و با گریدهای مختلف مطابق استانداردهای ملی ایران و بینالمللی است.
- فولاد تیکمه داش: این کارخانه یکی از برترین تولیدکنندگان فولاد در شمال غرب کشور است که انواع میلگرد ساده و آجدار را با کاملترین سبد خرید برای مصرفکنندگان ارائه میدهد.
- شركت نورد فولاد گیلان: ظرفیت تولید سالانه محصولات نورد گرم این کارخانه ۲.۵ میلیون تن است و میلگردهای ساده و آجدار از جمله طرحهای در دست توسعه آن محسوب میشوند.
- کارخانه فولاد بافق یزد: این کارخانه با ظرفیت تولید سالانه ۵۵۰ هزار تن میلگرد، یکی از پیشروترین تولیدکنندگان میلگرد باکیفیت در کشور محسوب میشود.
- نورد گرم سمنان: کارخانه نورد گرم سمنان با بهرهگیری از تجهیزات پیشرفته، قادر به تولید سالانه ۲۳۰ هزار تن میلگرد آجدار در سایزهای ۸ تا ۳۲ و با استانداردهای A2، A3 و A4 است.
- فولاد قائم رازی: در فاز دوم کارخانه فولاد قائم رازی، تولیداتی همچون شمش فولادی و انواع میلگرد ساختمانی با درصد بالای کربن، از طریق فرآیند نورد گرم به تولید میرسند.
- فولاد شاهین بناب: این کارخانه با سه خط نورد گرم در تولید میلگرد آجدار، تیرآهن، ناودانی و مفتولهای آلیاژی فعالیت میکند. همچنین، کارخانه شماره ۴ این مجتمع با دو خط تولید نورد گرم، ظرفیت ۴۵۰ هزار تن در سال دارد.
- شرکت ذوب آهن اصفهان: این کارخانه انواع مختلفی از محصولات فولادی از جمله میلگرد، تیرآهن، نبشی و ناودانی را با روش نورد گرم تولید میکند.
- فولاد البرز ایرانیان: این کارخانه تولید کننده مقاطع فولادی نورد گرم از جمله میلگردهای فایکو در اندازههای مختلف با ظرفیت تولید سالانه یک میلیون تن است.
- جهان فولاد سیرجان: این کارخانه میلگردهای گرم نوردیده را طبق استاندارد ملی شماره ۳۱۳۲ در سه نوع میلگرد ساده، آجدار مارپیچ و آجدار جناغی تولید میکند.
جمع بندی
این مقاله درباره فرآیند نورد گرم فولاد و میلگرد توضیح میدهد که یکی از مهمترین فرآیندها در تولید فولاد است که در دماهای بالا، معمولاً بین ۵۰۰ تا ۱۰۰۰ درجه سانتیگراد، انجام میشود. در این فرآیند، شمش فولادی از میان غلتکها عبور داده میشود تا به شکل و ابعاد مورد نظر برسد.