آهن اسفنجی که این روزها تجارت آن بیش از پیش رونق گرفته است و کارخانههای تولید آهن آلات ایران نیز برای تولید آن از تمامی ظرفیت خود کمک میگیرند، به عنوان یکی از گزینههای جذاب برای خرید پیشنهاد میشود. در این مقاله به بررسی ساختار و نحوه تولید آن پرداخته و مزایای استفاده از آن را عنوان کردیم و به مقایسه و تفاوت آن با دیگر مواد اولیه آهنی پرداختیم. پس در ادامه این مطلب با ما همراه باشید.
آهن اسفنجی چیست؟
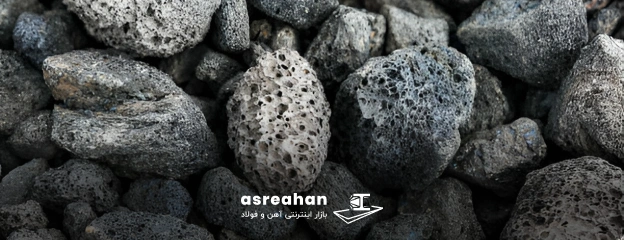
آهن اسفنجی یا به انگلیسی Direct Reduced Iron که به اختصار با نام DRI شناخته می شود از احیای مستقیم سنگ آهن و بدون استفاده از ذوب کردن آن انجام میشود.
به همین سبب این نوع آهن گاز اکسیژن خود را به تدریج از دست داده و شکل کروی به خود میگیرد، سطحی متخلخل و پر از حفرات ریز کوچک در سطح آن ایجاد میشود. این روش از محبوبیت خوبی نسبت به سایر روشهای تولید آهن برخوردار است چرا که به نسبت آلودگی کمتری وارد محیط زیست کرده و انتظار میرود در آیندهای نه چندان دور استفاده و تولید آن فزونی یابد.
آشنایی با تاریخچه آهن اسفنجی
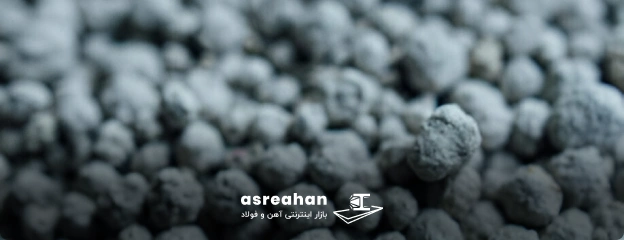
استفاده از آهن اسفنجی در کورههای القایی در ایران از سال 1389 آغاز شد، دورانی که کمبود آهن قراضه هنوز به شدت احساس نمیشد. در آن زمان، تولیدکنندگان هندی و چینی، به علت کاهش راندمان کورههایشان، استفاده از کورههای القایی فروخته شده به ایران را توصیه نمیکردند.
در همان سال، یکی از کارخانههای القایی در یزد، آهن اسفنجی را به عنوان ماده اولیه خود انتخاب کرد. در ابتدا، بسیاری از کارخانهها با استفاده از این ماده مخالف بودند و بازخوردهای منفی داشتند. علت اصلی این مخالفتها، عدم آشنایی با روش شارژ این ماده بود.
علاوه بر این، وجود فسفر و گوگرد در آهن اسفنجی در مقایسه با قراضه، باعث اختلال در آنالیز ذوب میشد و کربن بالا، زمان ذوب را افزایش میداد. با این وجود، پس از مدت کوتاهی، دیگر کارخانهها نیز به استفاده از آهن اسفنجی روی آوردند.
بررسی دو روش تولید آهن اسفنجی
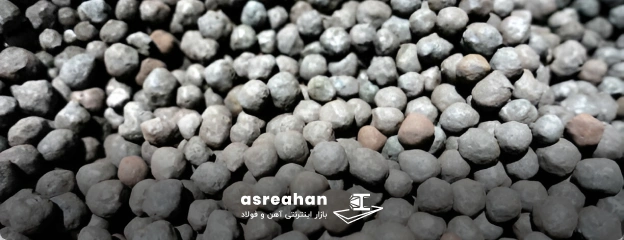
احیای سنگ آهن و تبدیل آن به آهن اسفنجی از دو راه استفاده از گاز طبیعی یا زغال سنگ امکان پذیر است. در پروسه احیا با گاز طبیعی نیز سه روش اصلی وجود دارد که با نامهای میدرکس،HYL و Purofer شناخته میشود. که روش میدرکس و HYL جز پرکاربردترینها هستند.
تولید آهن اسفنجی با استفاده از گاز طبیعی
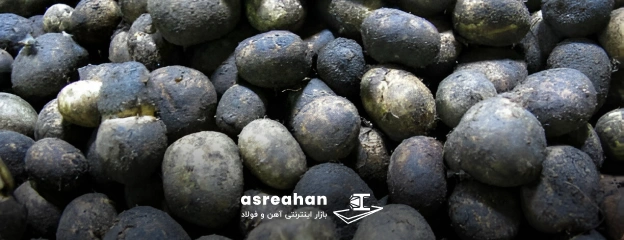
یکی از پرکاربردترین روشها برای تولید آهن اسفنجی استفاده از گاز طبیعی است. تبدیل گاز متان به هیدروژن و کربن مونوکسید و سپس ورود به کوره احیا سبب میشود به راحتی با سنگ آهن واکنش نشان داده و تبدیل به آهن اسفنجی شوند. برای انجام تمامی مراحل این فرایند نیز دو راه وجود دارد:
روش MIDREX (میدرکس)
در روش MIDREX، سنگ آهن با عیار بالا به طور مستقیم و بدون واسطه با گازهای حاصل از شکستن گاز طبیعی احیا میشود. این فرایند به دلیل بهرهوری بالای انرژی و استفاده از گاز طبیعی، به یکی از پرکاربردترین روشها در تولید آهن اسفنجی تبدیل شده است.
روش HYL
در روش HYL، گاز طبیعی به گازهای مورد نیاز تبدیل و به داخل کوره فرستاده میشود. این فرایند به دلیل پیچیدگی و هزینههای بالاتر نسبت به روش MIDREX، ممکن است در شرایط خاص کارآمدتر باشد. اگر نیاز به کنترل دقیقتر فرآیندهای احیا و تولید باشد، این روش به عنوان گزینهای بهتر در نظر گرفته میشود.
تولید آهن اسفنجی با استفاده از زغال سنگ
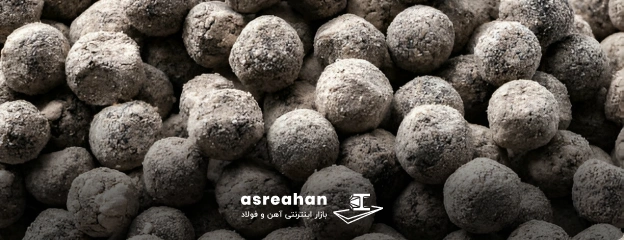
تولید آهن اسفنجی در مناطقی که دسترسی به گاز طبیعی سخت است، با زغال سنگ صورت میپذیرد. ر این شرایط آهن اسفنجی در کورههای خاصی و با استفاده از کربن ساخته میشود. استفاده از زغال سنگ ممکن است هزینههای بیشتری را متحمل شده و یا تبعات بیشتری برای محیط زیست داشته باشد.
عیار و چگالی آهن اسفنجی چقدر است؟
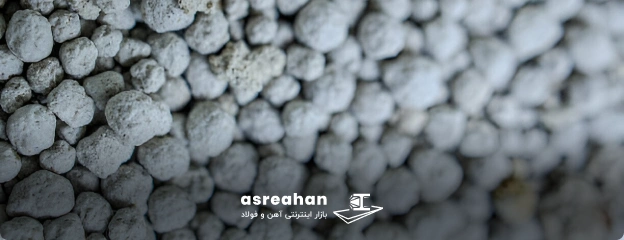
در مقایسه با قراضه آهن، آهن اسفنجی دارای چگالی بیشتری بوده که به صورت کلوخه برابر با 1.80 gm\cc و به صورت نرمه دارای چگالی 1.75 gm\cc است.
به دلیل چگالی بالای آهن اسفنجی، شارژ قراضه آهن به کوره کمتر شده و عیار آن چیزی در حدود 84 تا 95 درصد است. توجه داشته باشید که علاوه بر عیار آهن اسفنجی و ساختار خالص آن، تغییرات قیمت آهن امروز نیز بر قیمت آهن اسفنجی موثر بوده و نوسانات جهانی آن به صورت مستقیم بر روند قیمت تمامی محصولات فولادی اثر میگذارد.
فرمول شیمیایی آهن اسفنجی
فرمول شیمیایی آهن اسفنجی از احیای مستقیم سنگ آهن به دست آمده و به شرح زیر است:
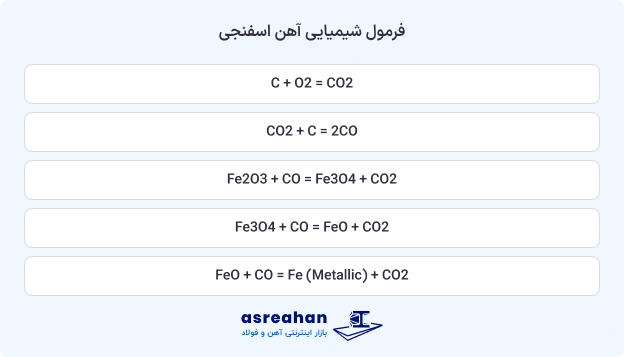
درصد ترکیبات استفاده شده در آهن اسفنجی نیز به صورت زیر است که همانطور که مشاهده میکنید بیشترین مقدار را آهن به خود اختصاص داده است. لازم به ذکر است که درجه متالیزاسیون نشان میدهد که چه درصدی از آهن به شکل آزاد و چه درصدی به صورت اکسید آهن در محصول وجود دارد.
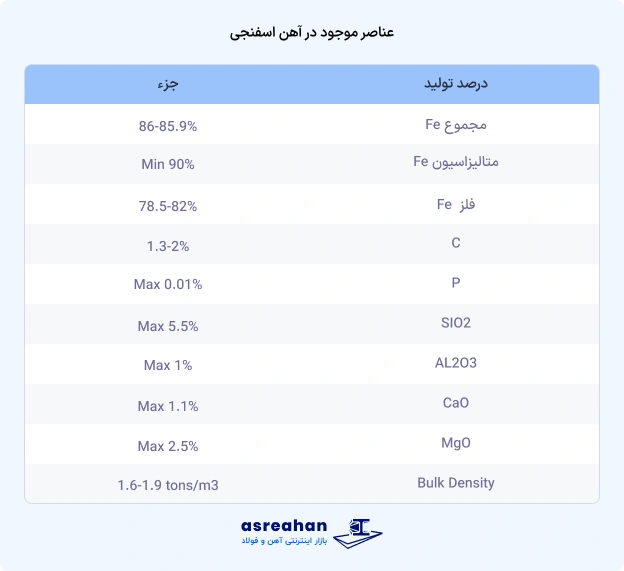
در کورههای الکتریکی (مانند کوره قوس الکتریکی یا کوره القایی) بخشی از این اکسید آهن میتواند احیا شده و به آهن آزاد تبدیل شود. به عنوان مثال، در کورههای القایی تجربه نشان داده که تقریباً نیمی از اکسید آهن احیا میشود. به همین دلیل، میزان سرباره یا پرت آهن اسفنجی در این کورهها کاهش مییابد.
مزایای استفاده از آهن اسفنجی
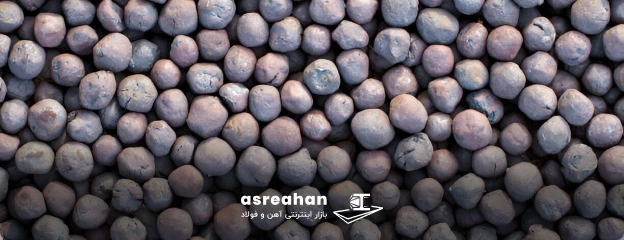
استفاده از آهن اسفنجی مزایای بیشتری نسبت به قراضه یا دیگر محصولات داشته که در ادامه این بحث به برخی از آنها میپردازیم:
- در ساختار آهن اسفنجی از گوگرد و فسفر کمتری استفاده شده و عناصر زائدی که در قراضه آهن وجود دارد در آهن اسفنجی دیده نمیشود.
- ساختار آن از بالای 97 % آهن تشکیل شده پس استفاده از آن کیفیت فلزکاری را تا سطح معقولی بالا میبرد و آسیب کمتری به کورهها میرسد.
- در مقایسه با قراضه آهن، اکسیژن کمتری برای تولید آهن اسفنجی مورد نیاز است.
- یک جایگزین خوب برای قراضه آهنی بوده و به عنوان عامل خوبی برای خنک کنندگی استفاده میشود.
خطرات آهن اسفنجی
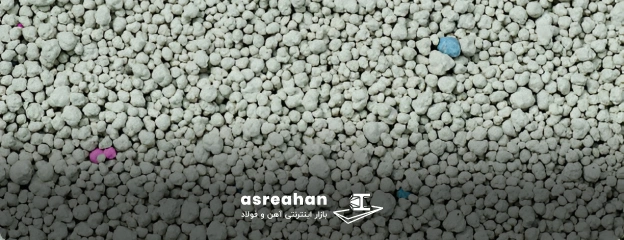
بسیاری از افراد بر این باورند که به دلیل استفاده درصد بالایی از آهن خالص در آهن اسفنجی، هیچ گونه خطری تهدید کننده نمیباشد. ولی به طور کلی، استفاده از آهن اسفنجی سه خطر عمده را به همراه دارد که در ادامه به بررسی کاملی از آن میپردازیم.
- آلودگی زیست محیطی: مواد خام مورد استفاده در تولید آهن اسفنجی، از نظر ترکیب شیمیایی و فیزیکی، باید به طور جداگانه بررسی شوند. یکی از ویژگیهای مهم آهن اسفنجی این است که به خصوصیات مواد خام مانند سنگ آهن، زغال سنگ غیر کک و دولومیت بسیار حساس است.
همچنین تولید آن ممکن است به سلامتی کارگران آسیب برساند چرا که در فرآیند تولید آهن اسفنجی، گازهای مضری مانند اکسید کربن، دیاکسید گوگرد و سایر ترکیبات گازی تولید میشوند که به منظور جلوگیری از این آسیبها، استفاده از وسایل حفاظتی مانند ماسکهای تنفسی ضروری است. - پتانسیل اکسیداسیون و زنگزدگی: اکسیداسیون و زنگزدگی از مهمترین خطرات مرتبط با آهن اسفنجی محسوب میشوند.
برای مقابله با این مشکل، میتوان آهن اسفنجی را به سرعت به فولاد تبدیل کرد یا برای آن یک لایه حفاظتی ایجاد نمود. این اقدامات به منظور جلوگیری از اکسیداسیون و زنگزدگی ضروری است. - خطر اشتعال آهن اسفنجی در حالت خمیری: آهن اسفنجی ممکن است در حالت خمیری خود اشتعال یا اکسیداسیون پیدا کند که میتواند خطرناک باشد.
برای جلوگیری از این مشکل، میتوان از روشهایی مانند بریکتسازی استفاده کرد. همچنین میتوان از موادی مانند گاز خنثی، آهک، و سیلیکات سدیم استفاده کرد و آهن اسفنجی را در فضایی سرپوشیده و محصور نگهداری نمود تا خطر اشتعال به حداقل برسد.
کاربرد آهن اسفنجی
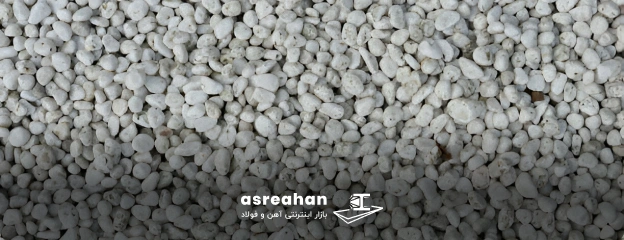
آهن اسفنجی در صنعت فولاد کاربردهای زیاد را از آن خود کرده است چرا که از احیای مستقیم سنگ آهن به دست آمده و خاصیتهای ویژهای دارد. ردپای استفاده از آهن اسفنجی در بسیاری از صنایع مختلف همانند صنعت خودروسازی، ابزارآلات و قطعات به چشم میخورد. آهن اسفنجی جایگزین قراضه آهن بوده و در بسیاری از کورههای القایی مورد استفاده قرار میگیرد.
البته که کاربرد آهن اسفنجی به اینجا ختم نشده و در در صنایع چدن و رزیختهگری فولاد نیز مورد استفاده قرار میگیرد چرا که استحکام بی نظیری به محصول بخشیده و دوام آن را تضمین میکند و به همین جهت ماده اولیه محبوب برای ساخت اسلحه و ابزارهای آهنی نیز میباشد.
تفاوت بریکت با آهن اسفنجی چیست؟
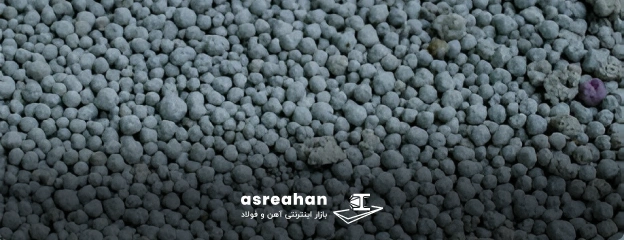
تفاوت اصلی میان بریکت و آهن اسفنجی از روش تولید آنها نشات میگیرد. پیشتر نیز اشاره شد که در ساخت آهن اسفنجی از روش زغال سنگ و یا میدرکس کمک گرفته شده اما بریکت خود از آهن اسفنجی تولید میشود.
به صورت کلی خواص این دو محصول با هم متفاوت است چرا که بریکت برای آلیاژسازی محصولی ایدهآل بوده و به راحتی با موادی همچون کربن ترکیب میشود که این ویژگی در آهن اسفنجی وجود ندارد. همچنین به دلیل تخلخل بالای موجود در آهن اسفنجی حجم زیادی به ازای وزن واقعی داشته و حمل و نقل آن با هزینه بیشتری صورت میپذیرد.
تفاوت گندله و آهن اسفنجی چیست؟
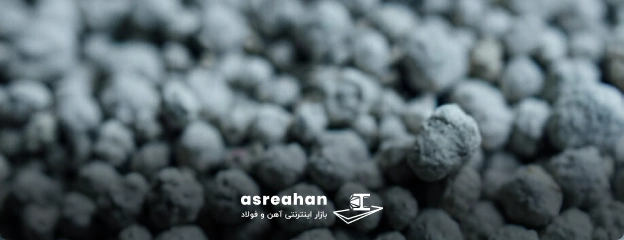
به طور کل گندله و آهن اسفنجی به عنوان ماده اولیه در فرآیند تولید فولاد به شمار میآیند که در خواص خود و روش ساخت دارای تفاوت هستند. به عنوان مثال گندله در چهار مرحله به تولید میرسد که این مراحل شامل خشک سازی، پیش گرم کردن، سوزاندن و سرد شدن است. پس در نتیجه فرآیند ذوب برای ذرات آن صورت نمیپذیرد.
اما در آهن اسفنجی که از اکسید آهن به عمل می آید؛ دو روش استفاده از گاز طبیعی یا زغال سنگ مشهود است و به نوعی فرآورده گندله محسوب میشود. پس در یک نگاه کلی آهن اسفنجی در صنایع مختلفی کاربرد دارد و از گندله به وجود آمده که لازم به ذکر است بعدها در صنعت خود آهن اسفنجی نیز به بریکت تبدیل خواهد شد.
لجن آهن اسفنجی چیست؟
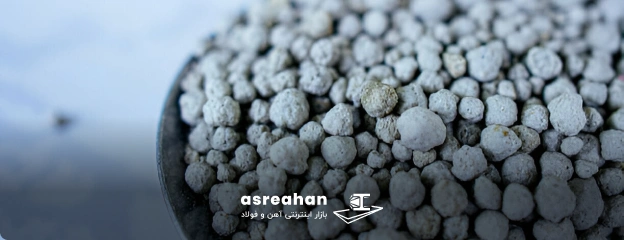
لجن آهن اسفنجی یک فرآورده معدنی است که هنگام تولید آهن اسفنجی به دست میآید. لجن آهن به صورت پودری بوده و در صنعت و تولید جایگاه مهمی را از آن خود کرده است.
لجن آهن اسفنجی زمانی به وجود میآید که ابتدا نرمه آهن اسفنجی با گاز احیا تماس پیدا میکند و سپس شسته میشود. بعد از انتقال به حوضچه ذرات و تهنشینی در آن، آب موجود در ترکیب به دلیل تبخیر کاهش مییابد و سپس با دیگر بارهای فلزی ترکیب میشود.
از مهمتریم کاربردهای لجن آهن نیز میتوان به تبدیل کردن به مواد کاربردی دیگر همچو گندله آهن و آگلومره اشاره کرد و در موارد دیگر صنعت نیز به کار برد.
کارخانههای تولیدکننده آهن اسفنجی در ایران

در ایران حدود 50 کارخانه به تولید آهن اسفنجی میپردازد که هر کدام، از روش منتخب خود این ماده را به تولید میرساند. اما به طور کل ذخایر گاز طبیعی ایران این امکان را به تولیدکنندگان میدهد تا از این روش برای احیای سنگ آهن استفاده کنند. در ادامه این مطلب لیست تولیدکنندگان آهن اسفنجی در ایران را در اختیارتان قرار میدهیم.
- ۱- کارخانه فولاد مبارکه: شرکت فولاد مبارکه اصفهان به عنوان بزرگترین تولیدکننده آهن اسفنجی در جهان شناخته میشود. این مجموعه ۲۰ درصد از بازار ورقهای تخت فولادی منطقه را تحت کنترل دارد و ظرفیت تولید آن به حدود ۱۱.۴ میلیون تن میرسد. ارزش کل محصولات تولیدی فولاد مبارکه در بازار، با توجه به شرایط فعلی، بیش از ۲۵۰۰۰۰ میلیارد تومان برآورد میشود.
- ۲- کارخانه فولاد کاویان گهر سیرجان: فولاد کاویان گهر سیرجان در حوزه آهن آلات فعالیت داشته و احیای آهن اسفنجی را به روش تونلی انجام میدهد. این کارخانه یکی از کارخانههای گندله سازی و کنسانتره در ایران است که ارتباط و همکاری خوبی با دیگر کارخانهها داشته و مشاوره تخصصی در خصوص آهن اسفنجی ارائه میدهد.
- ۳- کارخانه فولاد سیرجان ایرانیان: فولاد سیرجان ایرانیان فعالیت تولیدی خود را از آهن اسفنجی شروع کرده و اکنون جز ده کارخانه برتر تولید آهن اسفنجی در کشور است.
- ۴- کارخانه اسپاد فولاد آسیا: اسپاد فولاد آسیا با ده سال سابقه فعالیت در حوزه تامین مواد اولیه برای صنعت فولاد جز تولیدکنندگان آهن اسفنجی بوده و به واسطه تجارب خود ارتباط خوبی با کارخانههای آهن آلات و ذوبی دارد.
- ۵- کارخانه ساینا فولاد گلپا: این کارخانه با بیش از 25 سال سابقه در حوزه آهن آلات و حوزه استخراج صنعت معدن، یکی از تولیدکنندگان باتجربه آهن اسفنجی بوده و صادرات آن را به بیش از پنج کشور انجام میدهد.
- ۶- شرکت فولاد رهنمون صنعت: این کارخانه فعالیت خود را از سال 1395 آغاز کرده و علاوه بر تامین کنندگی مواد اولیه کارخانهها اعم از آهن اسفنجی و گندله و شمش میباشد بلکه در راستای تولید میلگرد، ورق و دیگر پروفیلهای فولادی نقش دارد.
- ۷- کارخانه توسعه آهن و فولاد گل گهر: شرکت توسعه آهن و فولاد گلگهر در سال ۱۳۹۱ با سرمایهگذاری عظیم در منطقه صنعتی گلگهر سیرجان تأسیس شد. این شرکت با هدف تولید 3.7 میلیون تن آهن اسفنجی به روش میدرکس و 3 میلیون تن فولاد به روش اسلب نازک و نورد ورق گرم فعالیت میکند. مأموریت اصلی شرکت، تولید ورقهای کیفی و تجاری با استانداردهای بالا و تأمین نیازهای داخلی کشور در این زمینه است.
- ۸- کارخانه فولاد اردکان: مجتمع فولاد اردکان به عنوان یکی از بزرگترین و اولین پروژههای خصوصی کشور در زمینه تولید آهن اسفنجی شناخته میشود. این مجتمع با هدف تأمین بخش عمدهای از نیاز داخلی کارخانههای فولادسازی، به همراه تأمین فولاد، فعالیت میکند. این مجموعه شامل تمامی مراحل تولید از جمله واحد کنسانتره، واحد گندلهسازی، واحد تولید آهن اسفنجی، واحد ذوب و فولاد و کارخانه نورد در شهرستان اردکان یزد است.
- ۹- فولاد برتر پارسیان: این مجموعه نیز به عنوان تامین کننده مواد اولیه برای کارخانههای حوزه تولید مقاطع فولادی شناخته میشود و آهن اسفنجی در لیست تولیدات آنها به چشم میخورد.
چند آمار و دیتای مهم در مورد آهن اسفنجی
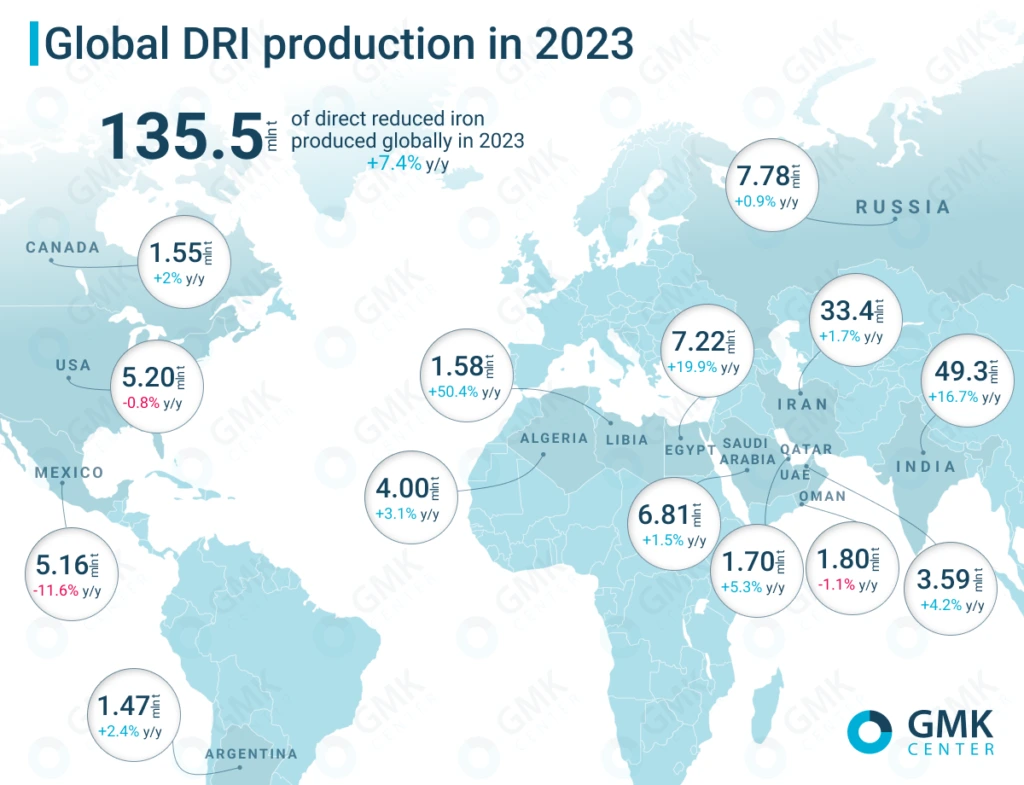
- هند و ایران با اختلاف چشمگیر از دیگر کشورها، بیشترین آهن اسفنجی جهان را در سال ۲۰۲۳ تولید کردند. تولید هند در این سال ۴۹ میلیون و ۳۰۰ هزار تن و تولید ایران ۳۳ میلیون و ۴۰۰ هزار تن بود.
هند در سال ۲۰۲۳، ۱۶.۷ درصد آهن اسفنجی بیشتری نسبت به سال ۲۰۲۲ تولید کرد و تولید ایران در سال ۲۰۲۳، ۱.۷ درصد بیشتر از سال ۲۰۲۲ بود. - کشور هند طبق آمار اعلام شده در سال 2023 از مجموع تولید ۱۳۵ میلیون و ۵۰۰ هزار تن آهن اسفنجی در جهان، مقدار ۴۹ میلیون و ۳۰۰ هزار تن را به خود اختصاص داده است.
- مابقی 39% تولیدات آهن اسفنجی نیز به ترتیب در کشورهایی مانند روسیه، مصر، عربستان سعودی، آمریکا، مکزیک، الجزایر، لیبی، قطر، عمان، کانادا و آرژانتین رقم میخورد؛ چرا که دارای منابع زغال سنگ و ذخایر گاز بوده و بدیهی است که بخش زیادی از آمار تولید آهن اسفنجی مربوط به این کشورها باشد.
جمع بندی
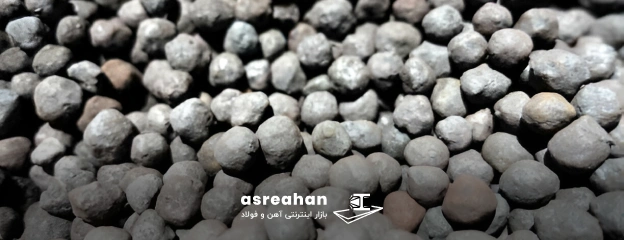
آهن اسفنجی یکی از مواد اولیه کارخانههای فولادی بوده و استفاده از آن نسبت به دیگر مواد همچون گندله مقرون بهصرفهتر است. این محصول خواص فیزیکی ویژهای داشته و آسیب کمتری به محیط زیست وارد میکند.
در این مقاله با بررسی کلی این محصول، کارخانههای تولیدکننده آن را معرفی کرده و آمار دقیقی از آنها در اختیارتان قرار دادیم؛ امید بر این است تا این مطالب یاریگر انتخاب شما برای یک خرید درست و بهینه باشد.
سؤالات متداول
بریکت از فشردهسازی آهن اسفنجی به دست میآید. بریکت دو تفاوت با آهن اسفنجی دارد و آن حجم بزرگ بریکت نسبت به آهن اسفنجی و وجود حفره و سوراخ روی سطح آهن اسفنجی است.
در حمل و انتقال آهن اسفنجی باید موارد لازم رعایت شود چراکه ممکن است انفجار و اشتعال بهوجود آید. راهکارهای مراقبی در داخل متن مقاله نوشته شده است.