ایران به سرعت در حال تبدیل شدن به بزرگترین تولیدکننده آهن اسفنجی در جهان است. با توجه به اینکه فرآیند احیای مستقیم سنگ آهن (DRI) در کارخانههای تولید فولاد رو به بهبود و در حال بهرهبرداری است.
از طرفی تولیدکنندگان اصلی آهن اسفنجی در جهان یعنی کشور هند و ونزوئلا با کاهش شدید احیای مستقیم سنگ آهن روبرو هستند؛ بنابراین فرصت بسیار مناسبی برای تولیدکنندگان آهن اسفنجی ایران مهیا است.
فهرست مطالب
با توجه به مرغوب بودن سنگ آهن در ایران و وجود منابع گاز طبیعی و استفاده از فناوری نوین مبتنی بر احیای اکسید آهن با روش میدرکس، مسیر برای برخورداری از محصول آهن اسفنجی برای کارخانجات فولاد هموار شده است.
تولید آهن اسفنجی در ایران
بیش از 800 هزار تن آهن اسفنجی سالانه در ایران تولید میشود. در واقع میتوان گفت ایران جزو بیشترین تولیدکنندگان فولاد در جهان است. به طوری که در سال 2020 دهمین کشور تولیدکننده فولاد در بین دیگر کشورهای سازنده فولاد بود همچنین رتبه دوم تولید آهن اسفنجی در سال 2020 از آن خود کرده است.
بیشترین میزان استخراج آهن در ایران از مناطق زیر است:
- سبزوار؛
- میانه؛
- شادگان؛
- سفید دشت؛
- بافت؛
- نی ریز؛
- قائنات.
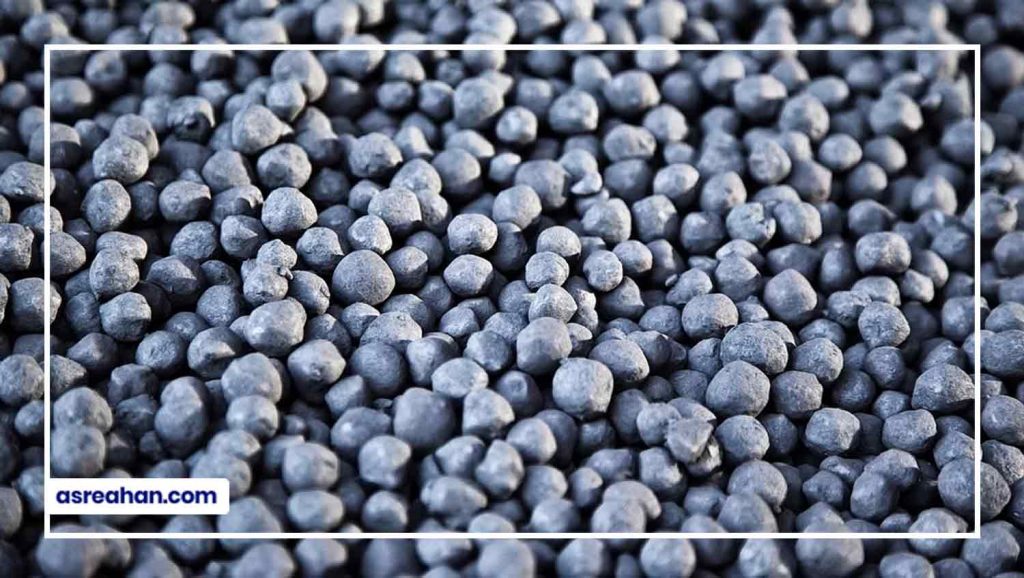
این نشان میدهد که کارخانه آهن اسفنجی در ایران فعالیت مناسبی در سطح داخلی و جهانی دارند. چون فرآوردههای آهنی در ساخت فولاد و مقاطع فولادی و ساختمانی بسیار پرکاربرد است و تولید آن از اهمیت بسیار بالایی برخوردار است.
ایران با داشتن تولیدکنندگان فولاد که تعداد آنها به بیش از 50 کارخانه میرسد به مواد اولیه تهیه آن نیز نیازمند است. سنگ آهن پس از گذراندن مراحل کنسانتره و تبدیل آن به گندله، به آهن اسفنجی تبدیل میشود که با استفاده از آن شمش فولادی میسازند.
کارخانه تولید آهن اسفنجی در ایران با استفاده از روش DRI فعال است؛ اما برای تولید آن از چند روش دیگر نیز میتوان استفاده کرد. به دلیل اینکه روش احیای مستقیم بر پایه گاز است و ایران منبع گاز طبیعی است، این فرآیند بهترین انتخاب برای تولیدکنندگان آهن اسفنجی ایران خواهد بود.
در سالهای اخیر با محدودیتهایی که برای کارخانههای فولاد به وجود آمده و بخشنامههایی که برای کاهش مصرف گاز در این کارخانجات اجرایی شده است، احتمال کمرنگتر شدن تولیدات ایران در صادرات دیده میشود که البته باید راهکارهای بهتری ارائه گردد.
بخوانید: ترکیبات سنگ آهن | روش استخراج و تبدیل آن به فولاد
لیست تولیدکنندگان آهن اسفنجی در ایران
آهن اسفنجی، مادۀ اولیه برای تولید شمش فولادی است. جایگزین بعدی برای آهن اسفنجی، آهن قراضه است. استفاده از آهن اسفنجی بهعنوان مادۀ اولیه، کیفیت شمش و نیز مقاطع ساخته شده از شمش را تا حد قابل توجهی بالا خواهد برد.
لیست کارخانههای تولیدکننده آهن اسفنجی در ایران به کمک احیای مستقیم به تولید این محصول میپردازند.
گفته میشود برای اولین بار در سال 89 تولید آهن اسفنجی در کوره القایی صورت گرفت. در ادامه تمامی تولیدکنندگان آهن اسفنجی در ایران معرفی خواهیم کرد:
- شرکت توسعه آهن و فولاد گل گهر
- شرکت صنعت فولاد شادگان، با ظرفیت تولید 800 هزار تن در سال
- مجتمع فولاد اردکان، با ظرفیت تولید 960 هزار تن در سال
- شرکت کاوه جنوب کیش، با ظرفیت تولید 1/8 میلیون تن در سال
- شرکت فولاد غدیر نی ریز، با ظرفیت تولید 800 هزار تن در سال
- شرکت فولاد سیرجان ایرانیان، با ظرفیت تولید 2/50میلیون تن در سال
- شرکت فولاد آذربایجان میانه
- مجتمع فولاد مبارکه اصفهان
- مجتمع فولاد خوزستان
- شرکت آهن و فولاد ارفع، با ظرفیت تولید 800 هزار تن در سال
- مجتمع فولاد رشتخوار، با ظرفیت تولید 1/2 میلیون تن در سال
- شرکت مجتمع جهان فولاد سیرجان، با ظرفیت تولید 2 میلیون تن در سال
لیست کارخانه تولید آهن اسفنجی که هم برای تولید محصولات داخلی از آن استفاده میکنند و هم به دیگر تولیدکنندگان، فولاد عرضه میکنند و نیز بخش بزرگی از نیاز کارخانجات تولید محصولات فولادی در جهان را تأمین میکنند، معرفی شد.
بیشترین حجم سنگ آهن ایران به کشورهایی نظیر چین و مصر صادر میشود و در کارخانجات تولیدی میلگرد، تیرآهن و دیگر مقاطع فولادی مورد استفاده قرار میگیرد.
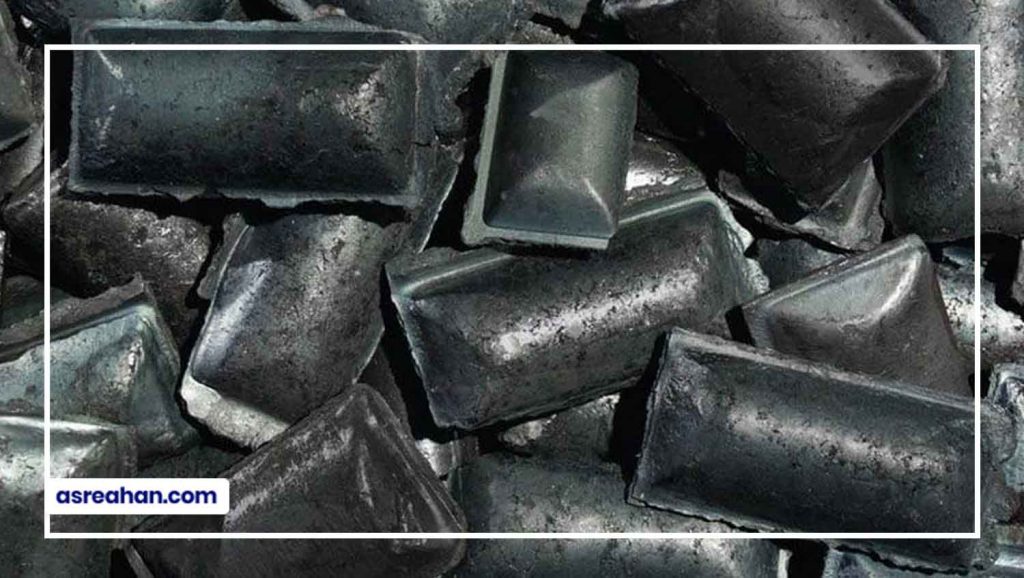
تفاوت گندله و آهن اسفنجی
در چرخه تولید فولاد، سنگ آهن ابتدا کنسانتره شده سپس به گندله تبدیل میگردد، گندله گویهای کوچکی است که با افزودن برخی مواد به سنگ آهن و حرارت آن به وجود میآید سپس به مرحله تولید آهن اسفنجی انتقال میگردد.
در واقع تولید گندله یک مرحله پیش از آهن اسفنجی است. یکی از تفاوتهای گندله با آهن اسفنجی میزان عیار آهن است یعنی عیار آهن در آهن اسفنجی بیشتر از گندله است. برای آسانتر شدن حمل و انبار آهن اسفنجی، آن را به شکل بریکت در میآورند این بریکت در سه نوع سرد، گرم و نرم است.
گندله گرد و کروی بوده ولی بریکت آهن اسفنجی شکلی شبیه به مکعب دارد. پس این دو محصول از نظر شکل ظاهری نیز با هم در تفاوتاند.
روش ذوب آهن اسفنجی
در واقع استفاده از کلمه ذوب برای تولید آهن اسفنجی درست نیست؛زیرا این محصول آهنی با استفاده از روش احیای مستقیم ساخته میشود که در این فرآیند بدون ذوب کردن مواد، اکسیژن درون سنگ حذف میگردد. در این روش با استفاده از گاز، فرآیند انجام میگیرد که اکثرا در دو روش است؛ میدرکس و HYL.
روش دیگری که برای تولید آهن اسفنجی مورد استفاده قرار میگیرد، استفاده از زغال سنگ به جای گاز طبیعی است. این محصول تولید شده باید همیشه از رطوبت حفظ شود و در جای خشک و خنک نگهداری گردد؛ بنابراین شرایط انبارداری و حمل و نقل ویژهای خواهد داشت.
بخوانید: جایگاه صنعت فولاد ایران در جهان
سخن آخر
تولیدکنندگان آهن اسفنجی در ایران، محصولی با 86 تا 90 درصد آهن به روش احیای مستقیم سنگ آهن تولید کرده و به بازار عرضه میکنند؛ همچنین صادرات این محصول پرکاربرد به تولیدکنندگان فولاد در جهان نیز از خط تولید آهن اسفنجی کشور بهرهمند است.
ما در این دانشنامه سعی داشتیم علاقهمندان و فعالان در حوزه آهن و فولاد را با تولیدکنندگان آهن اسفنجی در ایران آشنا کنیم. با تلاش و تولید بهینه این کارخانهها، ایران رتبه بسیار خوبی در تولید آهن اسفنجی در جهان خواهد داشت.
برای اطلاع از قیمت آهن آلات و خرید انواع مقاطع فولادی به وبسایت عصرآهن مراجعه کنید یا با واحد مشاوره عصرآهن با شماره 0414180 در تماس باشید، کارشناسان ما راهنمای شما خواهند بود.
وبسایت عصرآهن تمام اطلاعاتی را که در مورد محصولات آهن و فولاد، قیمت، کاربرد و فروشندگان این محصولات نیاز دارید، برای شما فراهم کرده است.