آهن عنصری است که در زندگی انسانها و در حیات زمین تأثیر زیادی دارد. از مهمترین عنصر در ساخت فولاد گرفته تا کمک به حمل اکسیژن در خون و تغذیۀ گیاهان و جانداران از جمله تأثیرات مهمِ عنصر آهن در حیات جهان است. آهن مادهای سخت و شکننده است که در گروه 4 جدول تناوبی قرار دارد و بهعنوان فلز، طبقهبندی شده است.
تا به حال به این فکر کردهاید استخراج سنگ آهن چگونه انجام میشود یا روش استخراج چند نوع است؟
در این مقاله همراه ما باشید؛ میخواهیم به ترکیبات سنگ آهن و نحوۀ استخراج آهن و تبدیل آن به فولاد بپردازیم.
فهرست مطالب
دربارۀ فلز آهن بیشتر بدانید!
منظور از اینکه میگوییم آهن بر کل زمین تأثیرگذار است یعنی اینکه این فلز چهارمین عنصر رایج در پوسته زمین بوده و حجم زیادی از هستۀ زمین را در بر میگیرد؛ حتی طبق تحقیقات و آزمایشات در اروپا، این عنصر علاوه بر اینکه در زمین یافت میشود، در عناصر خورشید و ستارگان نیز بهوفور در دسترس است.
در واقع میتوان بهراحتی گفت آهن برای بقای موجودات زنده بسیار مهم است. در گیاهان در تولید کلروفیل نقش دارد، در حیوانات و انسان جزو هموگلوبین خون است و موجب میشود اکسیژن، خون را از ریه به بافتهای بدن برساند.
بیشترین مقدار از این ماده برای ساخت فولاد و آلیاژهای آهن و کربن استفاده میشود؛ همچنین در ساختوساز و عرصۀ مهندسی عمران کاربرد زیادی دارد. بهعنوان مثال در ساخت المانهای سازۀ بتن مسلح استفاده میگردد. سنگ آهن در ساختار خود اکسید فریک، مگنتیت، لیمونیت یا همان هیدروکسید فریک هیدراته، سیریت کربنات آهن دارد. تولید آهن به استفاده از فرآیند ذوب برای تبدیل سنگ آهن به محصول قابل مصرف گفته میشود.
بخوانید: اصلی ترین تفاوت آهن و فولاد در چیست؟
دستهبندی آهن
همان طور که قبلاً گفته شد 5 درصد وزن پوسته زمین را آهن تشکیل میدهد و بعد از اکسیژن، سیلیکون و آلومینیوم چهارمین عنصر فراوان در جهان است که در دمای 1538 درجه سانتی گراد ( 2800 درجه فارنهایت) ذوب میشود.
سنگ آهن انعطافپذیر است و با چکش زدن بهراحتی میتوان آن را شکل داد. بهندرت از سنگ آهن بدون افزودن عناصر دیگر استفاده میشود و اغلب برای بهبود خواص آن با افزودنیهایی همراه میشود. عمدتاً آلیاژ آهن به همراه کربن در ساخت فولاد استفاده میشود و حدود 0/003 تا 8 درصد کربن به این عنصر اضافه میشود.
باتوجه به درصد کربن افزودنی، آهن به سه دستۀ فولاد کم کربن، فولاد با کربن متوسط و فولاد با کربن زیاد تقسیم میشود. در ترکیب کربن موجود در فولاد، کاربید آهن (Fe3C) که به آن سمینیت نیز گفته میشود، وجود دارد. تعین درصد آهن در سنگ آهن بهراحتی امکانپذیر نیست؛ اما با بررسی آنچه گفته شد میتوان مقدار مشخصی از آن را حدس زد.
خصوصیات مکانیکی مختلف در آهن با ایجاد تغییر در مقدار کربن به دست میآید؛ یعنی اگر در آهن مقدار زیادی از کربن استفاده شود به آن چدن و اگر کربن مصرفشده با میزان کم باشد به آن سمنتیت و فریت گفته میشود. این تطبیقپذیری آلیاژهای آهن و کربن منجر به استفادۀ گستردۀ آن در مهندسی شده و آن را به مهمترین فلز در صنعت تبدیل کرده است.
تاریخچۀ ذوب سنگ آهن در کوره
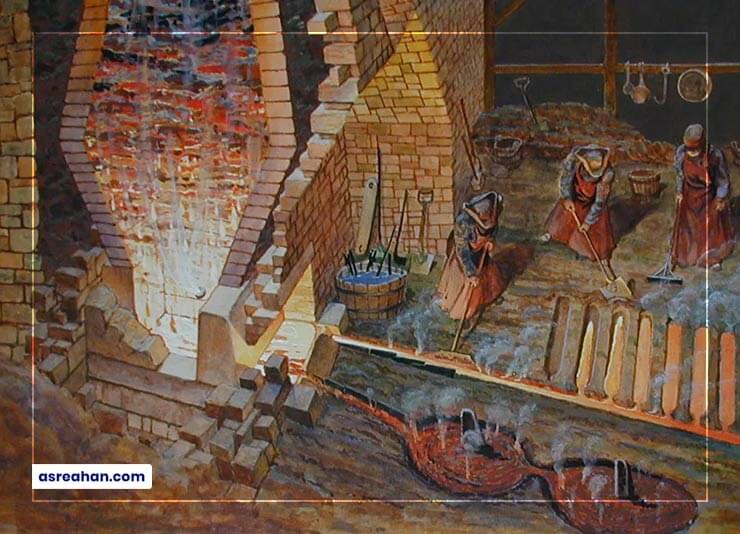
بر اساس شواهد موجود، شهاب سنگها 3 هزار سال قبل از میلاد بهعنوان منبع دسترسی به آهن شناخته میشدند؛ اما استخراج سنگ آهن از معادن سنگ به 2000 سال پیش از میلاد برمیگردد. مناطق آناتولی و ایران اولین منابع برای استخراج این سنگها بهشمار میآیند.
در گذشته برای ساخت آهن دو نوع کوره در نظر گرفته شده بود، کورههای کاسهای با حفر یک سوراخ کوچک در زمین و انتقال هوا از طریق لوله یا کورههای ساخته شده از سنگ، که هر دو کاربردی و قابل استفاده بودند. هر دو کورۀ ذوب، شامل بستری از زغال داغ بود که سنگ آهن با حرارت آن، ذوب میشد؛ اما از آنجا که کورههای اولیه قادر به رسیدن به دمای بالاتر از 1150 درجه سانتی گراد نبودند با گسترش علم و فناوری کورههای مدرنتر با قابلیت های زیاد ساخته شد.
بعد از ذوب سنگ آهن در کوره، نوبت شکلدهی و ساخت لوازم موردنیاز با استفاده از آهن بود. در دوران باستان، شکلدهی فلزات به چکش زدن فلز داغ گفته میشد. لازم است بگوئیم که آهن ساخته شده از این روش، فرفورژه نام دارد. در این روش امکان داشت از زغال سنگ، زیاد استفاده شود بنابراین آلیاژهایی از آهن و کربن که دارای نقطۀ ذوب کمتری بودند هم به نقطۀ ذوب برسند.
کاربردهای این نوع آهن بهدلیل شکنندگی آن محدود بوده و در اوایل دورۀ عصرآهن فقط چینیها از آن استفاده میکردند. تا قرونوسطا، تغییر کمی در روشهای ساخت آهن اتفاق افتاد؛ اما در قرن پانزدهم، روش کوره بلند در اروپا پدیدار شد؛ کورهای بزرگ که در کارخانۀ ذوب استفاده میشد.
محصول به دست آمده از کوره بلند به آهن خام (pig iron) تبدیل میشد و بعد از طی کردن مراحل مختلف در قالب شمش عرضه میگردید. با گذشت زمان، روش کوره بلند گستردهتر شد و از موتور بخار برای حرکت سیلندرهای دمنده آن استفاده شد. این کار برای تأمین هوای بیشتر انجام گرفت.
برویم سراغ آشنایی بیشتر با ترکیبات سنگ آهن.
ترکیبات سنگ آهن
سنگ آهن در طبیعت بیشتر در سنگهای آذرین یا رسوبی یافت میشود. بیشترین منبع برای سنگ آهن، سنگهای رسوبی هستند؛ اما بسیاری نیز در اثر هوازدگی تغییر کردهاند بنابراین تعیین منشأ دقیق سنگ آهن دشوار است. سنگ معدن آهن عمدتاً از هماتیت (Fe2O3) که به رنگ قرمز است، مگنتیت (Fe3o4) به رنگ سیاه، سنگ لیمونیت یا همان سنگ آهن (2Fe2o3.3H2o) به رنگ قهوهای و سیدیریت (FeCo3) که قهوهای کم رنگ است، تشکیل شده است.
مگنتیت خالص حاوی 72 درصد، هماتیت 70 درصد، لیمونیت 60 درصد و سیدریت 48 درصد آهن است؛ اما وجود این درصد از مواد معدنی در محتوای سنگ آهن یکجا ممکن نیست. در کل رسوباتی که کمتر از 30 درصد آهن دارند، پرطرفدار نیستند و کاربرد زیادی ندارند. سنگهای قابل برداشت باید دارای 50 الی 60 درصد آهن باشند.
نکتۀ مهم: وجود ترکیباتی مثل فسفر P2O5 در محتوای سنگ حتما باید بررسی شود؛ زیرا این ماده در ترکیب فلز تأثیر میگذارد و مشکلات بیشتری در ساخت فولاد ایجاد میکند.
بهتر است بدانید که چین، برزیل، استرالیا، روسیه و اوکراین پنج تولیدکنندۀ سنگ آهن هستند؛ همچنین مقادیر قابل توجهی نیز در هند، ایالات متحده، کانادا و قزاقستان استخراج میشود. این 9 کشور باهم، 80 درصد سنگ آهن جهان را تولید میکنند. برزیل، استرالیا، کانادا و هند بیشترین صادرات در این زمینه را دارند و ژاپن، اروپا و آمریکا جزء بیشترین واردکنندگان هستند.
بخوانید: فلزات آهنی و غیرآهنی | تفاوت و جنبههای کاربری هر یک از آن
مشخصات سنگ آهن
- حالت خالص این ماده در طبیعت نسبت به فلزات دیگر زیاد یافت میشود؛
- اگر در معرض هوای مرطوب و دمای بالا قرار بگیرد به سرعت تخریب میشود؛
- آهن (Fe)، فلزی نسبتاً متراکم با ظاهری سفید-نقرهای است؛
- خاصیت مغناطیسی دارد.
نحوه استخراج سنگ آهن
برای بهدست آوردن سنگ آهن باید این مادۀ معدنی استخراج شود. در استخراج سنگ آهن، با توجه به نوع معدن، عمق سنگ آهن و شرایط اقتصادی یکی از دو روش استخراج را در پیش میگیرند. انواع روش استخراج آهن عبارتند از:
- روش روباز (سطحی)
- روش زیرزمینی
استخراج آهن به روش روباز
بیشتر کانسنگهای آهن با استفاده از استخراج سطحی، استخراج میشوند. با اینکه معادن زیرزمینی برای استخراج این ماده وجود دارد؛ اما تا جای امکان، استخراج سطحی ترجیح داده میشود زیرا این روش مقرونبهصرفهتر است.
سنگ آهن استخراج شده شامل تودههایی با اندازههای مختلف است که بزرگترین آن بیش از 1 متر و کوچکترین آن 1 میلیمتر است. باتوجه به اینکه کوره بلند به تودههایی بین 7 الی 25 میلیمتر نیاز دارد، سنگ معدن باید توسط سنگشکن خرد شود تا حداکثر اندازه ذرات کاهش یابد. اگر سنگ آهن استخراج شده در ابعاد و کیفیت مناسبی باشد بدون ایجاد تغییرات (خرد کردن) مستقیماً به کوره انتقال داده میشوند. در این مرحله مواد زائد سنگ آهن از آن جدا میشود و سپس به کوره انتقال مییابد.
در استخراج سطحی سنگ آهن، در محدودۀ موردنظر با استفاده از مواد منفجره، کانسار (بخشی از پوستۀ زمین که تراکم مواد معدنی در آن زیاد باشد) را خرد میکنند؛ سپس به کارخانۀ ذوب آهن یا محل دپو انتقال میدهند.
استخراج معادن زیرزمینی
استخراج زیرزمینی با استخراج سطحی تفاوت دارد. اگر کانسار آهن در عمق زیادی از زمین قرار داشته باشد باید برای رسیدن به سنگ آهن، چاه حفر میشود و سپس از طریق حفاری، انفجار و بارگیری، بقیۀ مراحل استخراج آهن صورت میگیرد. این روش برای معادن زیرزمینی استفاده میشود.
بخوانید: افزایش تولید جهانی سنگ آهن در سال 2021
تا اینجای مقاله راجعبه ترکیبات و استخراج سنگ آهن صبحت کردیم. زمان آن رسیده تا به مراحل استخراج آن و تبدیل این مادۀ معدنی به فولاد را بیشتر بررسی کنیم.
مراحل استخراج سنگ آهن
سنگ آهک بخشی از باری است که هنگام استخراج آهن از سنگ معدن، همراه سنگآهن استخراج میشود. هنگامی که سنگ آهن (دارای کربنات کلسیم) در نتیجۀ گرمای زیاد داخل کوره تجزیه میشود، با ناخالصیهای موجود واکنش داده و چیزی به نام سرباره ایجاد میکند.
کربن به شکل زغال سنگ به کارخانههای فولادسازی تحویل داده میشود و قبل از مخلوط شدن با سنگ آهک و سنگ آهن معروف به هماتیت، باید آن را تا دمای بالا در کوره گرم کرد. این کار مقداری از ناخالصیها را از زغال سنگ حذف میکند و مادهای به نام کک را تشکیل میدهد.
1. خرد کردن سنگ
مرحله اول معمولاً خرد کردن است که در آن قطعات بزرگ سنگ معدن به اندازه کوچکتر کاهش مییابد. غربالگری و خرد کردن یک عملیات ساده مکانیکی است. طی این عملیات مکانیکی، ترکیبات سنگ معدن تغییر نمیکند.
قبل از اینکه سنگ آهن در دستگاه سنگشکن ریخته شود، تکههای کوچک از تکههای بزرگ سوا میشوند که این عمل باعث افزایش بهرهوری در نتیجۀ کار میشود (این کار وزن بار انتقالی به سنگشکن را کاهش میدهد). بعد از انتقال سنگ به سنگشکن و خرد کردن محتوای درون آن در ابعاد دلخواه، مواد معدنی در انبار مخصوص دپو میشوند.
تصویر زیر نشان میدهد که چگونه میتوان از سنگشکن برای شکستن سنگهای بزرگ به سنگهای کوچکتر استفاده کرد. در استخراج سنگ آهن این مرحله جزء مراحل مهم محسوب میشود.
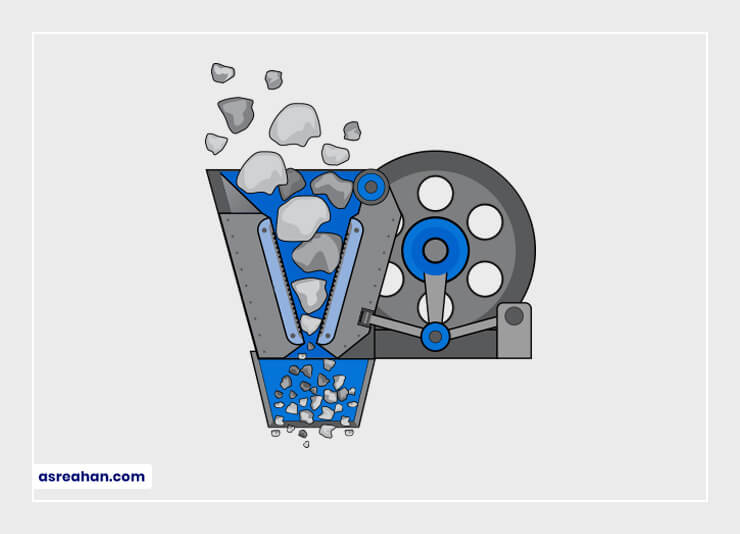
2. غربالگری
مرحله بعدی، غربالگری مواد خرد شده است و توسط آب و دستگاه مخصوص انجام میگیرد. این مرحله ممکن است 2 تا 3 بار انجام شود. بعد از این مرحله از روشهای مغناطیسی کمک میگیرند تا مواد سبک و مواد دارای خاصیت مغناطیسی از هم جدا شده و عیار آهن مصرفی، کیفیت بالایی داشته باشد.
ناخالصیهای شیمیایی طی فرایند پخت سنگ، حذف میشوند. در این مرحله، سنگ معدن حاوی فلز در یک اتاق یا کوره هوادهی شده تا دمای بالا گرم میشود. این فرآیند می تواند مولکولهای آب از داخل سنگ خارج کند و مواد شیمیایی نامطلوب را به محصولات شیمیایی مطلوبتر تبدیل کند.
پس از حذف ناخالصیها، سنگ آهن تصفیه شده با سنگ آهک و کک در بسترهای پخت مخلوط میشود. این بسترها برای فشردهسازی سنگ آهن، سنگ آهک و مواد کک به یک توده جامد استفاده میشود. مواد سست معمولاً هنگام گرم شدن بهصورت تودهای جامد و فشرده درمیآیند.
3. پخت سنگ آهن
سومین مرحله بعد از استخراج سنگ آهن، پخت آن است. این مرحله، شامل حرارت دادن به مواد درون کوره است. این مرحله تا زمانی انجام میشود که ذوب جزئی اتفاق بیفتد و ذرات سنگ به هم متصل شوند. این فرایند قبل از انتقال به فرآیند پخت انجام میگیرد که سنگ معدن آهن به حالت خمیری در آمده و باعث میشود ذرات به یکدیگر بچسبند. در این مرحله کُک زغال سنگ که یک مادۀ پر از کربن است به مواد مذاب اضافه میشود و سپس به کورۀ پخت انتقال میشود.
فرایند پخت تضمین میکند که سنگ آهن، سنگ آهک و مواد کک بهطور یکنواخت مخلوط میشوند؛ همچنین مواد مناسبی را برای ریختن در کوره بلند آماده میکند. به این مرحله سینترینگ (sintering) یا زینتر کردن سنگ آهن یا به اصطلاح تفجوشی میگویند.
بسترهای سینترینگ دارای سطح وسیعی هستند و فرایند پخت در آن بهسرعت انجام میشود. تصویر زیر نشان میدهد که چگونه میتوان از بسترهای تفجوشی برای تغییر خواص سنگها و مواد ناخالص استفاده کرد.
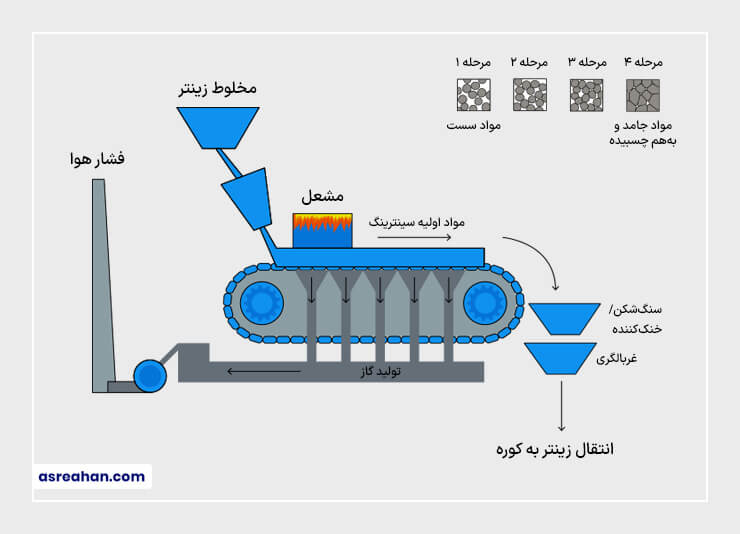
مخلوط سنگ آهن، کک و سنگ آهک بهعنوان شارژ کوره بلند شناخته میشود. بار شامل این مواد روی تسمه نقاله به بالای کوره بلند میروند. تصویر زیر نشان میدهد که چگونه از تسمه نقاله برای انتقال مخلوط بار به بالای کوره بلند استفاده میشود. این تسمهنقالهها در تمام طول شبانهروز کار کرده و دائماً مواد اولیه را به کوره بلند منتقل میکنند.
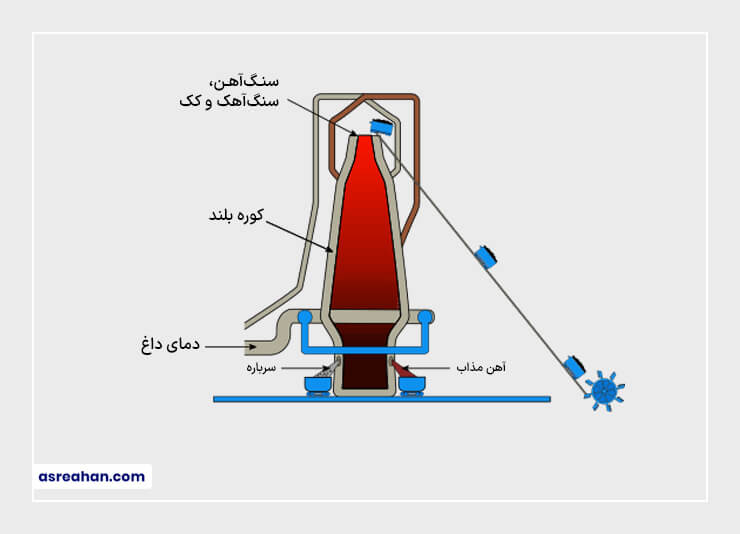
4. گُندلهسازی
در مرحلۀ آخر این مواد و ترکیبات تولید شده به گُندلههای نرم و کروی تبدیل میشوند. این گندلهها رنگ سبز یا قهوهی دارند و در دمای 1250 تا 1340 درجه سانتیگراد خشک و سخت میشوند. این گلولهها قطری بین 10 تا 15 میلیمتر دارند و در شکلی ایدهآل و مناسب قابل استفاده در کوره بلند هستند.
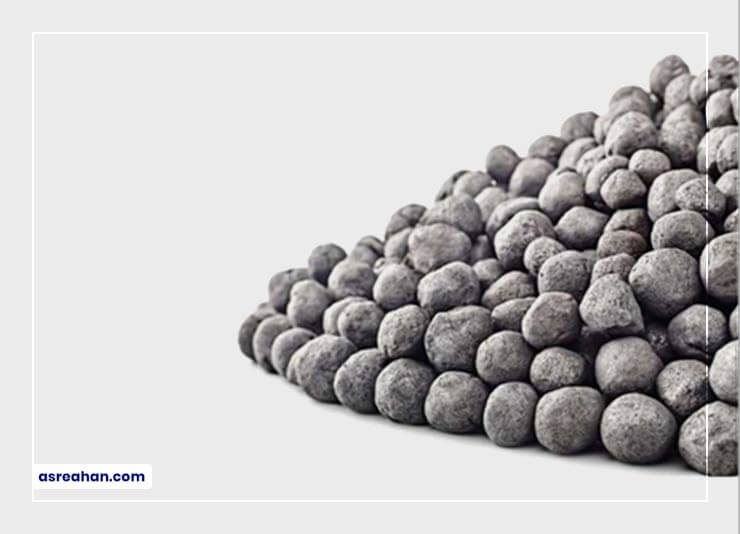
سنگ آهن چگونه به فولاد تبدیل میشود؟
استخراج آهن بیشک یکی از مهمترین فرایندهای صنعتی روی زمین است. یعنی جامعۀ مدرن بدون استخراج سنگ آهن بهوجود نمیآید.
کارخانههای تولید فولاد حداقل یک سیستم کوره بلند دارند که می توانند با استفاده از آن، آهن مذاب را از سنگ معدن تصفیه نشده مانند هماتیت تولید کنند. در این کارخانهها آهن مذاب تولید شده، توسط دمش اکسیژن به محصولات آلیاژی فولادی تبدیل میشود.
کارخانههای فولادی معمولاً خارج از شهر ساخته میشوند زیرا آلودگی زیادی تولید میکنند. این تولیدکنندهها دارای سیستمهای پیچیدهای هستند که از انواع مختلف ماشینآلات و بخشهای بزرگ تشکیل شدهاند. شکل زیر مهمترین قسمتهای یک کارخانۀ تولید فولاد را نشان میدهد.
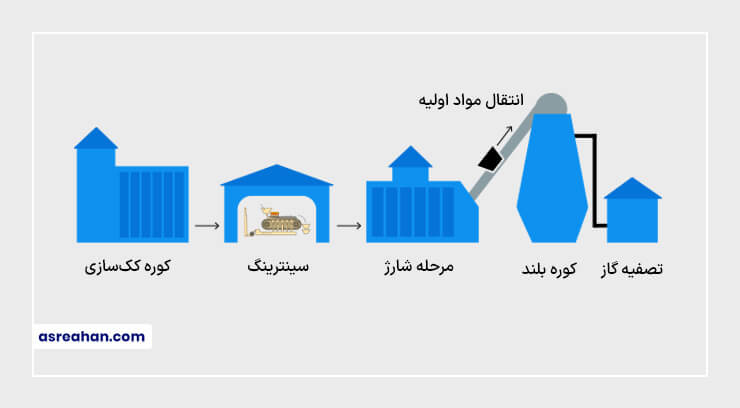
به تصویر بالا نگاه کنید. سازۀ سمت چپ، ساختمانی را نشان میدهد که کورههای کُکسازی را در خود جای داده است. کک در کورههای ککسازی تولید میشود و سپس با سنگ آهک ترکیب میگردد.
کُک، شکلی از کربن خالص است که از زغال سنگ تولید میشود و با حرارت دادن زغال سنگ تا دمای بالا در کورۀ ککسازی به دست میآید. سنگهای زغالسنگ معمولاً تا درجه حرارت 1000 تا 1100 درجۀ سانتیگراد گرم میشوند (در برخی مواقع تا دمای بالاتر هم گرم میشود).
این فرایند، باعث تبخیر یا تجزیۀ مواد آلی نامطلوب در زغال سنگ و دفع ترکیبات فراّر مانند آب میشود. موادی که بعد از این تجزیه بهدست میآیند، بیشتر متشکل از اتمهای کربندار هستند.
آهن در داخل یک کوره بلند - یک برج فولادی بزرگ به ارتفاع 40 متر - ریخته میشود. گازهای زائد تولیدشده از این فرایند، دیاکسیدکربن و نیتروژن است. برای آشنایی بیشتر با این مرحله پیشنهاد میکنیم به دانشنامۀ زیر را مطالعه کنید.
بخوانید: تاریخچه تولید فولاد از اولین زمان پیدایش تا به امروز
سنگ آهن؛ مهمترین عنصر در جهان
فلز آهن مادهای است که در صنایع بسیاری نظیر ساختوساز، ماشینسازی، کشتیسازی و صنایع مهم دیگر کاربرد دارد. برای تبدیل سنگ آهن به مادهای قابل مصرف و ایدهآل، فرآیندهای بسیاری باید انجام گیرد. در مرحلۀ نخست، استخراج سنگ آهن خام از معادن انجم میشود. پس از استخراج به ترتیب انتقال، خردکردن، غربالگری، تصفیه و شکلدهی روی مادۀ اولیه صورت میگیرد تا به محصول موردنظر تبدیل شود. در این دانشنامه سعی شد به جزئیات این فرآیند پرداخته شود.
برای دسترسی سریع به آهنآلات موجود در بازار و قیمت روز آهن و فولاد میتوانید با واحد مشاورۀ عصرآهن با شماره 0414180 در تماس باشید، کارشناسان ما راهنمای شما خواهند بود. سایت عصر آهن تمام اطلاعاتی را که در مورد محصولات آهن و فولاد، قیمت، کاربرد و فروشندگان این محصولات نیاز دارید، برای شما فراهم کرده است.
سوالات متداول
فلز آهن معمولاً از سنگ معدنی هماتیت استخراج میشود که حاوی اکسید آهن (Fe2O3) است. سنگ معدن باید قبل از قرار گرفتن در کوره بلند تصفیه شود. در ساخت آهن در کوره بلند، دو مادۀ خام یعنی هماتیت و سنگ آهک لازم است.
فولاد ضدزنگ که حداقل 10.5 درصد کروم دارد از استخراج سنگ آهن و پخت آن در کوره به دست میآید. این فولاد در برابر خوردگی بسیار مقاوم است. تنها تفاوت این نوع فولاد با فولادهای دیگر در ترکیبات و نوع آلیاژ آن است.