امروزه فولاد یکی از مهمترین و پرکاربردترین فلزات تولیدشده از آهن در جهان است. با استفاده از فولاد انواع مقاطع آهنی، لوازم خانگی، ماشینآلات، سازههای کوچک و بزرگ، انواع ابزار و دیگر محصولات کاربردی ساخته میشود. اما آیا میدانید تولید فولاد برای اولین بار چگونه و به چه روشی انجام شد؟ تاریخچه تولید فولاد به کدام تاریخ و عصر برمیگردد؟
در این مقاله از اولین زمان پیدایش فولاد تا به زمان حال را بررسی کردهایم. با ما همراه باشید تا سفری در پیدایش و دگرگونی صنعت فولاد داشته باشیم.
فهرست مطالب
تاریخچه تولید فولاد
تاریخچۀ تولید فولاد به 4000 سال قبل از آغاز عصرآهن برمیگردد. قدیمیترین نمونههای اولیه مربوط به استفاده از فولاد حدوداً 1800 سال قبل از میلاد ثبت شده و دقیقا از آن زمان با پشت سرگذاشتن عصرهای گوناگون از امپراطوری روم، اسپارتها، سلسلههای چین به کاربردهای امروزی رسیده است. اما چه کسی فولاد را کشف کرد؟
اگرچه تعیین زمان دقیق کشف فولاد غیرممکن است؛ اما با نگاه به تاریخچۀ تولید فولاد در طول تاریخ به ما کمک میکند تا کسانی که در پیدایش فولاد نقشی داشتهاند، پیدا کنیم.
عصر آهن و تاریخچه تولید فولاد
بیایید سرنخهای مرتبط با تاریخچه تولید فولاد را در طول تاریخ بررسی کنیم:
قرن سیزدهم قبل از میلاد
اولین نشانههای تولید فولاد را میتوان به آهنگران قرن سیزدهم ربط داد؛ آهنگرانی که برای اولین بار دریافتند، با کم کردن درصد کربن در آهن، این ماده مقاومتر و با دوامتر میشود.
قرن ششم قبل از میلاد
صنعتگران در هند باستان، از فولاد برای ساخت تیغه، نیزه و شمشیر استفاده میکردند. چون در این نوع فولاد از مادهای به نام ووتز استفاده شده به آن فولاد ووتز یا (wootz steel) هم گفته میشود. در گذشته از فولاد ووتز بهدلیل تیز و مقاوم بودن در ساخت انواع سلاح استفاده میشد. به این فولاد، فولاد دمشق هم گفته میشود.
قرن سوم پس از میلاد
چین بهعنوان تولیدکننده انبوه فولاد شناخته شده است. به احتمال زیاد در این بازۀ زمانی در کشور چین، از تکنیکهایی مشابه فرایند بسمر (در ادامه راجعبه ین فرایند بیشتر صحبت خواهیم کرد) که در قرن نوزدهم در اروپا رواج یافت، استفاده میکردند.
نمونههای تولید فلز فولاد با کیفیت در چین را میتوان به قرن دوم قبل از میلاد ربط داد؛ اما تولید انبوه آن در قرن سوم پس از میلاد آغاز شد.
قرن چهارم پس از میلاد
ستون آهنی دهلی (Iron Pillar of Delhi) در سال 402 میلادی در هند ساخته شد. این ستون بهدلیل مقاومت در برابر زنگزدگی مشهور است و تا به امروز پابرجاست. برای محافظت این ستون در برابر خوردگی و رطوبت، لایهای از جنس فسفر روی ستون فولادی کشیده شده است. تصویر این ستون را در زیر ببینید:
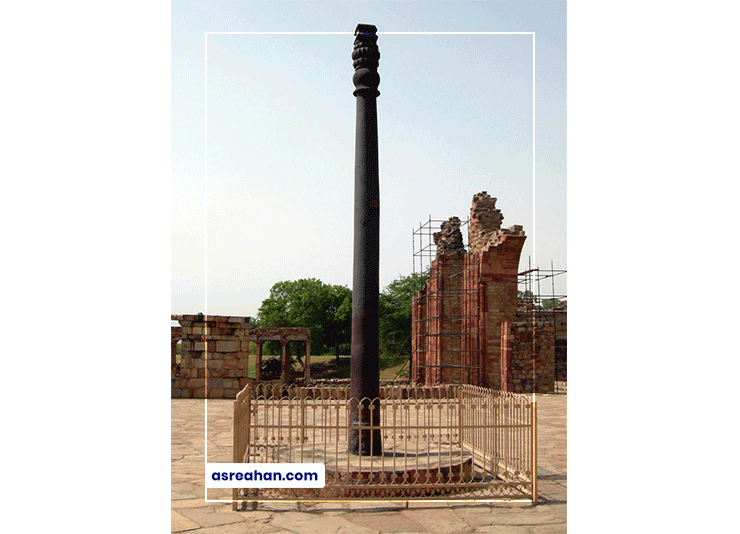
قرن یازدهم
استفاده از فولاد دمشق (Damascus steel) در قرن یازدهم در خاورمیانه توسعه یافت و بیشتر برای ساخت تیغههای شمشیر استفاده میشد. تیغههای دمشقی در خاور نزدیک از شمشهای فولاد ووتز که از هند و سریلانکا وارد میشد، تولید میشدند. محصولات تولید شده بهدلیل تواناییشان در تراشیدن لبههای بسیار تیز و مقاومت در برابر شکستن، مشهور بودند.
قرن دوازدهم
در قرونوسطا در آسیای جنوبی نوعی فولاد به نام فولاد بوتهای کشف شد. این نوع فولاد نسبت به فولاد امروزی شکنندهتر بود؛ اما در برخی کاربریها مانند ساخت ابزارآلات استفاده میشد. تا قرن دوازدهم، سریلانکا بزرگترین تأمینکننده فولاد بوتهای در جهان بود.
در قرن هفدهم خواص آهن برای همه روشن بود، اما افزایش روز افزون شهرنشینی در اروپا، نیازمندی به فلز را بیش از پیش کرد و در قرن نوزدهم، متالوژیستها برای تامین آهن مورد نیاز برای گسترش راهآهن شروع به چارهاندیشی کردند. باید مشکل شکنندگی آهن و فرایندهای تولیدی ناکارآمد حل میشد.
همین کارها باعث شناختهتر شدن فولاد و گسترش استفاده از آن شد. در سال 1856 پیشرفتی در تاریخ فولاد رخ داد و هنری بسمر از اکسیژن برای کاهش میزان کربن آهن استفاده کرد و صنعت فولاد مدرن متولد شد و تاریخچه تولید فولاد دگرگون شد.
سال 1702
کک برای اولین بار در ذوب سنگ آهن در حجم زیاد استفاده شد و بعد از آن جایگزین چوب و زغال چوب شد. میتوان گفت این رخداد شروع تازهای برای تولید فلز فولاد بود.
یکی از قدیمیترین انواع فولاد، فولاد ضدزنگ است که تولید آن در قرن 17 میلادی، در آلمان و انگلیس آغاز شد. به کمک این نوع فولاد با افزایش میزان کربن در آهن، چدن مذاب با استفاده از فرایندی به نام سمنتاسیون (هیدرومتالوژی) تولید میشود.
در این فرآیند، میلههای آهنی با زغال چوب پودری در جعبههای سنگی و گرم پوشیده شدهاند. پس از حدود یک هفته، آهن، کربن را در زغال چوب جذب میکند.
گرمایش مجدد، کربن را بهطور یکنواخت توزیع میکند و در نهایت پس از خنک شدن، فولاد ضدزنگ به دست میآید.
کربن بیشتر، باعث تولید فولاد ضدزنگ و کارآمدتر میشود. فولاد به دست آمده از آهن چدن مناسبتر است و قابلیت نوردکاری و فشردهسازی دارد.
سال 1712
توماس نیوکامن (Thomas Newcomen) اولین موتور بخار تجاری موفق را ساخت. و فولاد راه صنعت را به سوی انقلاب صنعتی هدایت کرد.
سال 1740
تکنیک فولاد بوتهای که در بالا به اولین استفاده از آن اشاره کردیم، توسط مخترع انگلیسی به نام بنجامین هانتسمن (Benjamin Huntsman) توسعه یافت. تولید فولاد ضدزنگ در دهۀ 1740 گسترش یافت؛ زمانی که بنجامین هانتسمن، ساعتساز انگلیسی در حال تلاش برای تولید فولاد با کیفیت برای فنرهای ساعت خود بود، متوجه شد که فلز ممکن است در بوتههای رسی ذوب شود و با یک شار ویژه برای حذف خاکستری که روند سمنتاسیون را پشت سر گذاشته شده، تصفیه شود.
همین امر موجب شد تا فولاد مایع یا عملیات ریختهگری بهوجود آید. اما با توجه به اینکه هزینههای تولید بسیار زیاد بود، هر دو فولاد ضدزنگ و فولاد ریختهگری فقط در پروژههای تخصصی استفاده میشد.
سال 1779
قدرت در کارخانههای فولاد جریان یافت، به این معنی که آنها دیگر نیازی به استفاده از آب نبود و با روشهای دیگری به نورد فولاد مشغول شدند. با نگاه به تاریخچه تولید فولاد و بررسی مراحل مختلف، میتوان فهمید که با استفاده از روشهای جدید پروسه تولید فولاد، کارآمدتر از قبل میشد.
سال 1783
هنری کورت (Henry Cort) شخصی که اهل انگلیس بود، غلتک فولادی را برای تولید فلزات اختراع کرد. پس از آن، آهنگران دریافتند که چطور میتوان چدن خام را با استفاده از کورههای پودلینگ (که توسط هنری کورت در سال 1784 توسعه داده شد) به یک آهن کار شدۀ کم کربن تبدیل کنند.
کوره گرم ذوب آهن که با استفاده از ابزارهای بلند و درشت، اجازه میدهند اکسیژن با کربن ترکیب شود سپس به آرامی آن را حذف میکنند.
زمانی که کربن موجود در آهن کاهش مییابد، نقطه ذوب آن افزایش پیدا میکند، بهطوری که تودههای آهن در کوره انباشته میشوند، این تودهها قبل از این که به ورق یا ریل نورد شده تبدیل شوند با چکش آهنگری روی آنها کار میشود.
سال 1794
فیلیپ وان (Phillip Vaughn)، مخترع ولزی، طرح بلبرینگ را برای پشتیبانی از محور کالسکه به ثبت رساند.
قرن هجدهم
در قرن هجدهم، فولاد بهعنوان یک ماده بسیار ارزشمند با کاربردهای فراوان شناخته شد. با این حال، تولید آن بسیار گران بود و در کاربردهای خاص مانند تولید زره، ابزار و سلاح تولید میشد.
سال 1813
مهندس انگلیسی هنری بسمر (Henry Bessemer) در 19 ژانویه 1813 متولد شد. اجازه دهید بعداً به این موضوع بپردازیم).
سال 1830
کمکم ماشینآلات فولادی در صنعت کشاورزی به کار گرفته شد.
سال 1855
فرآیند بسمر معرفی شد. فرآیند بسمر اولین فرآیند صنعتی ارزان قیمت برای تولید انبوه فولاد از آهن مذاب قبل از توسعه تولید آن به روش کوره باز بود. در این روش ناخالصیها از آهن از طریق اکسیداسیون حذف میشد. هر چه ناخالصی کمتر باشد، فولاد قوی تر است.
هر آنچه گفتیم نگاهی مختصر به تاریخچه تولید فولاد بود. برای آشنایی بیشتر با فرایند بسمر و اتفاقات بعد از آن در مسیر تولید فلز فولاد باید نگاهی عمیقتر به اتفاقات این بازۀ زمانی بیاندازیم.
در سال 1860 بیش از 3000 کوره پودلینگ در بریتانیا ساخته شده بود؛ اما این روند بهدلیل کمبود نیروی کار و کاهش شدت سوخت به تعویق افتاد. در نتیجه، چدن ساخته شده در کورههای پودلینگ، بهعنوان فلز اصلی در صنعت انگلستان در طول قرن نوزدهم باقی ماند.
چدن فلز محکمی است؛ اما به دلیل وجود کربن در آن، شکننده و ترد است و برای نورد و شکل دادن فلز مناسبی نیست. زمانی که متالوژیستها متوجه شدند محتوای کربن زیاد در آهن آن را شکننده میکند، روشهای جدیدی برای کاهش میزان کربن و افزایش کارآیی آن آزمایش کردند.
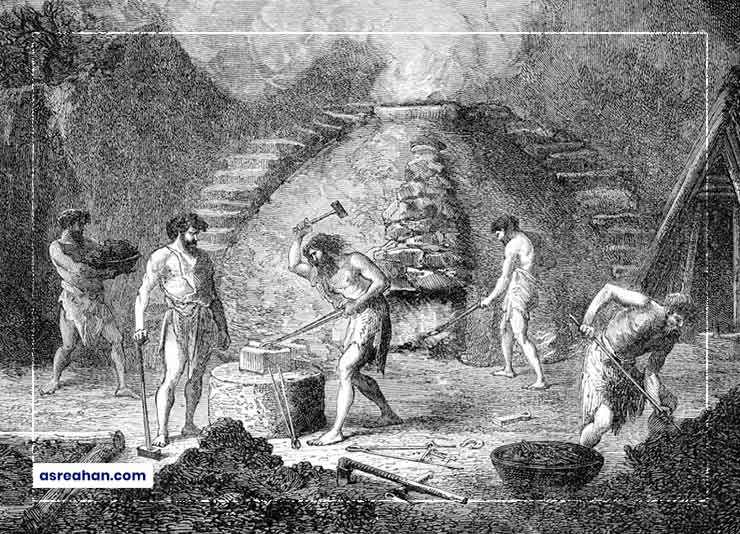
فرآیند بسمر و فولادسازی مدرن
با نگاه به تاریخچه تولید فولاد میتوان درک کرد که صنعت راهآهن چقدر نقش پررنگی در زندگی مردم داشته است. ازاینرو رشد راه آهن در طول قرن نوزدهم در اروپا و آمریکا فشار عظیمی بر صنعت فولاد وارد کرد. فولاد هنوز بهعنوان یک فلز ساختاری، پذیرفته نشده بود و تولید آن آهسته و پرهزینه بود. این مسئله تا زمانی ادامه داشت که هِنری بسمر با روش موثرتری یعنی با اضافه کردن اکسیژن به آهن مذاب، جهت کاهش محتوای کربن روی کار آمد.
در حال حاضر فرایندی که با نام بسمر شناخته میشود، از ظرفی گلابی شکل که نقش مبدل را دارد، تشکیل شده است و میتوان آهن را در آن گرم کرد و اکسیژن را به فلز مذاب دمید.
زمانی که اکسیژن به فلز مذاب منتقل شود، با کربن واکنش میدهد سپس کربندیاکسید آزاد شده و نهایتاً آهن خالص تولید میشود.
این فرایند سریع و ارزان بوده و کربن و سیلیکون را در عرض چند دقیقه از آهن حذف میکند. در واقع کربن زیادی از فولاد حذف شده و اکسیژن خیلی زیادی در محصول نهایی باقی میماند. در نهایت بسمر مجبور شد سرمایهگذاران خود را بازپرداخت کند تا بتواند روشی برای افزایش محتوای کربن و حذف ناخواسته اکسیژن بیاید. نام بسمر در طول تاریخچه تولید فولاد از جمله اسامی تاثیرگذار بوده است.
در همان زمان رابرت ماشت، متالوژیست بریتانیایی متوجه این مشکل شد و به آزمایش ترکیبی به نام اسپیژلیزن تشکیل شده از آهن، کربن و منگنز پرداخت.
منگنز برای حذف اکسیژن از آهن مذاب و کربن موجود در آهن بهکار میرفت، بنابراین پی برده شد اگر این عنصر در مقادیر مناسب اضافه شود، راهحلی برای مشکلات بسمر خواهد بود. بسمر با موفقیت آن را به فرایند تبدیل خود اضافه کرد.
تنها یک مشکل باقی میماند؛ راهحلی برای حذف فسفر از محصول نهایی که موجب شکنندگی فولاد میشد پیدا نشد. در نتیجه فقط سنگ معدن فسفر سوئد و ولز میتوانست مورد استفاده قرار گیرد.
در سال 1876 ولزمن سیدنی گیلچریت توماس یک شار اساسی پایه، یعنی سنگ آهک را به فرایند بسمر اضافه کرد. سنگ آهک، فسفر را از آهن خام به سربارههای آهن منتقل میکند که موجب حذف عنصر ناخواسته میشود.
این نوآوری به این معنی است که در هر نقطه از جهان میتوان با استفاده از سنگ آهن، به تولید فلز فولاد پرداخت.
تعجبآور نیست زیرا هزینههای تولید به طور قابل توجهی کاهش یافته بود. قیمت ریلهای فولادی در سالهای 1867 تا 1884 بیش از 80 درصد کاهش یافت.
این مورد به عنوان نتیجهای از تکنیکهای جدید تولید فولاد و آغاز رشد صنعت فولاد جهان به شمار میرود. با توجه به آنچه گفته شد میتوان درک کرد که دیگر تاریخچه تولید فولاد به تکامل خود نزدیک و نزدیکتر میشد.
بخوانید: آشنایی با آهن، فولاد و چدن | بررسی کاربرد و تفاوت هر یک از آنها
تولید فولاد به روش کوره باز
در دهۀ 1860 کارل ویلهلم زیمنس (Carl Wilhelm Siemens)، مهندس آلمانی، ساخت فولاد را از طریق ایجاد فرایند کوره باز افزایش داد.
فرایند سوزاندن کربن اضافی و دیگر ناخالصیها با استفاده از دمای بالا، در اتاقهای آجری داغ زیر کوره، فرایند کوره باز معرفی شد.
در کورههای احیا کننده از گازهای خروجی بهمنظور حفظ دمای بالا در اتاقهای آجری زیر کوره، استفاده میکردند.
در این روش برای تولید مقادیر بسیار بیشتر (50 تا 100 متریک تن ممکن است در یک کوره تولید شود)، تست دورهای فولاد مذاب انجام شد تا بتوانند فولاد قراضه را بهعنوان مادۀ اولیه در داخل کوره ذوب کنند و با استفاده از آن به تولید انواع محصولات فولادی بپردازند. اگرچه فرایند تولید در روش کوره باز پیشرفت کندتری داشت ولی در سال 1900، جایگزین فرایند بسمر شد.
میبینید! تاریخچه تولید فولاد پر از آزمایشها و تستهای مختلف است. سبکسنگینهایی که باعث هدفمند شدن راه ساخت فولاد شد.
تولد صنعت فولاد
تاریخچه تولید فولاد را بررسی کردیم اکنون زمان پرداختن به صنعت مدرن فولاد و خط تولید مقاطع فولادی است. انقلاب در ساخت فولاد که باعث شد محصولات ارزانتر و با کیفیتتر ارائه شود، توسط بسیاری از بازرگانان روز بهعنوان یک فرصت سرمایهگذاری به رسمیت شناخته شد. سرمایهگذاران قرن نوزدهم، از جمله اندرو کارنگی و چارلز شواب، میلیونها سرمایه در صنعت فولاد انجام دادند و از طریق آن به ثروتهای کلانی دست یافتند؛ اما در کنار ثروثاندوزی به جامعۀ بشریت نیز بسیار کمک کردند.
در دهۀ 1860، پس از جنگ داخلی آمریکا، ساخت فولاد این کشور با سرعت شگفتانگیزی رشد کرد. صنعت فولاد آمریکا، توسط اندرو کارنگی (Andrew Carnegie) صنعتگر اسکاتلندی-آمریکایی رهبری میشد. شرکت آمریکایی فولاد کارنگی که در سال 1901 تأسیس شد اولین شرکتی بود که بیش از یک میلیارد دلار ارزش داشت.
بعد از آن در سال 1868، فولاد تنگستن توسط رابرت ماشت (Robert Mushet) اختراع شد و به صنعت فولاد راه یافت.
بهترتیب بعد از آن در سال 1880 میلادی، اولین پل معلق فولادی یعنی پل بروکلین (Brooklyn Bridge) و اولین آسمان خراش فولادی یعنی ساختمان بیمه در شیکاگو (Home Insurance Building in Chicago) افتتاح شد.
با ورود به قرن بیستم، جنگهای جهانی در نیمه اول قرن بیستم اتفاق افتاد، به این معنی که ساخت فولاد روزبهروز افزایش یافت. این سازهها مهمترین سازههای فولادی در طول تاریخچه تولید فولاد بهشمار میآیند.
از آن زمان به بعد، پیشرفتهای مهمی در صنعت فولادسازی و پروسه تولید فولاد ایجاد شد. که شاهد تولید از سلاحها و ابزارهای مختلف، کالاهای مصرفی و تغییرات در حملونقل از جمله مهمترین این موارد بود. این تحولات از آن زمان تاکنون ادامه داشته است و فولاد نقش مؤثر خود را در همه جای جهان مدرن گذاشته است.
تولید فولاد به روش قوس الکتریکی
در تاریخچه تولید فولاد انواع روشهای تولید استفاده شد که بهترین آنها در تابهحال مورد استفاده قرار میگیرند. در اواخر قرن، توسعه دیگری در صنعت فولاد رخ داد که تأثیر مهمی بر تکامل تولید فولاد داشت. کوره قوس الکتریکی (EAF) که در انگلیسی به آن (Electric Arc Furnace) گفته میشود توسط پل هرویت (Paul (Héroult فرانسوی اختراع شد. این روش برای عبور جریان الکتریسیته از طریق مواد باردار طراحی شده بود، که باعث اکسیداسیون میشد.
در تولید فولاد به روش قوس الکتریکی، درجه حرارت را تا 3272 درجه فارنهایت (1800 درجه سانتیگراد) میتوان افزایش داد که برای ساخت فولاد حرارتی، دمای مناسبی است.
روش استفاده از کورههای قوس الکتریکی در ابتدا برای فولادهای خاص و نیز در جنگ جهانی دوم برای تولید فولاد آلیاژی استفاده میشد.
سرمایهگذاری در راهاندازی کارخانههای کوره قوس الکتریکی این امکان را فراهم کرد تا با تولیدکنندگان زیادی مانند فولاد آمریکا و فولاد Bethlehem، مخصوصا در ساخت فولادهای کربنی یا محصولات کوره بلند، رقابت کنند.
از آنجایی که در ساخت فولاد با کورۀ قوس الکتریکی میتواند فلز را از 100 درصد ضایعات یا مواد معدنی سرد تهیه کنند، انرژی کمتری در واحد تولید مورد نیاز است.
در حالی که روش کوره اکسیژن انرژی بسیار زیادی طلب میکند. ساخت فولاد با روش EAF میتواند با هزینۀ کم انجام شود.
به همین دلیل، تولید از طریق کوره قوس الکتریکی، بهطور مداوم برای بیش از 50 سال انجام شد و در حال حاضر حدود 33 درصد از ساخت فولاد جهان را به خود اختصاص داده است.
تولید فولاد به روش دمش اکسیژن
در حال حاضر بیشتر تولید فولاد جهانی یعنی حدود 66درصد آن، به روش دمش اکسیژن تولید میشود؛ یعنی این روش در تاریخچه تولید فولاد نمانده و در عصر مدرن نیز استفاده میشود. توسعه روش جداسازی اکسیژن از نیتروژن در دهه ۱۹۶۰ برای اولین بار انجام شد. این روش در کورههای اولیه اکسیژن با موفقیت آزمایش شد.
در کورههای اکسیژن، با دمش اکسیژن به مقادیر زیادی کربن در آهن مذاب و آهن قراضه سوزانده میشود سپس عناصر و آلیاژهای مورد نیاز به فولاد اضافه میگردد. در انبارهای بزرگ که دارای 350 تن آهن هستند در کمتر از یک ساعت میتوانند انبار آهن خود را به فولاد تبدیل کنند.
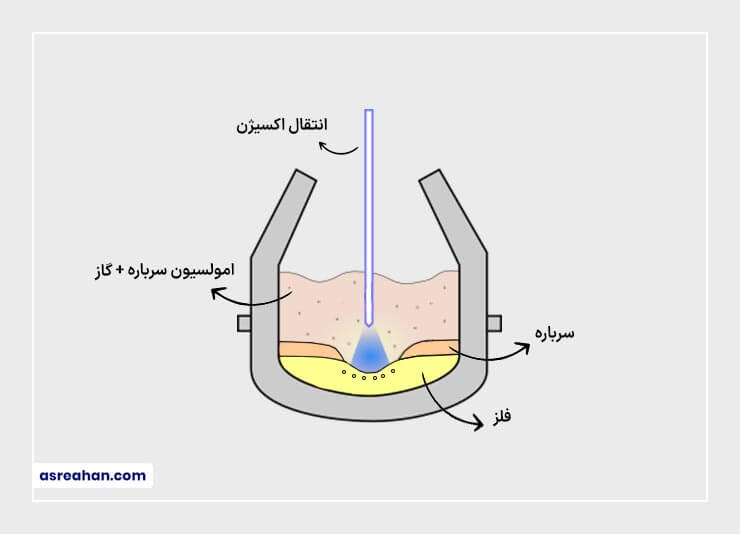
هزینههای مناسب خط تولید فولاد به روش دمش اکسیژن، باعث شد کارخانجات کوره باز غیر رقابتی شوند و بعد از ظهور این روش در دهه 1960، عملیات تولید به روش کوره باز از میان رفت. آخرین تأسیسات کوره باز در ایالات متحده در سال 1992 و در چین در سال 2001 بسته شد.
برای آشنایی با فرآیند تولید فولاد از سنگ آهن پیشنهاد میکنیم به دانشنامۀ ترکیبات سنگ آهن | روش استخراج و تبدیل آن به فولاد مراجعه کنید.
تاریخچه فولاد در ایران
شاید بسیاری از شما تاریخچه فولاد در ایران را با ذوب آهن اصفهان به یاد آورید بهدلیل اینکه این کارخانه اولین و قدیمیترین تولیدکنندۀ فولاد در ایران است. باید گفت اولین تاریخ تأسیس کارخانه فولاد در ایران به سال 1310 برمیگردد؛ زمانی که کشور آلمان در نظر داشت در داخل خاک ایران در جایی نزدیک به معادن سنگ آهن، کارخانه فولاد تأسیس کند؛ اما با شروع جنگ جهانی دوم این کار انجام نشد.
بعد از آن شرکت ملی ذوب آهن ایران در سال 1344 طی قراردادی با شوروی سابق ساخته شد و از آن زمان تاکنون خط تولید فولاد این کارخانه در ایران فعال است. در طول این مسیر تولیدکنندگان دیگری هم به لیست کارخانجات ساخت فولاد و انواع مقاطع آهنی اضافه شده است. امروزه در استانهای زیادی دسترسی به کارخانجات فولاد وجود دارد؛ اما تاریخچه تولید فولاد در ایران با ذوب آهن اصفهان شروع شده است.
بخوانید: جایگاه صنعت فولاد ایران در جهان
جمعبندی
در این دانشنامه تاریخچه تولید فولاد و نحوه پیدایش آن را آغاز تا اکنون را بررسی کردیم. همچنین بررسی کردیم اولین استفاده از فولاد به چه نحوی بود و توسط چه کسی کشف شده بود. امیدواریم با استفاده از مقالۀ جامع به اطلاعاتی که نیاز داشتید، دستیابی داشته باشید. اگر این مطلب برایتان مفید بود آن را با دیگران به اشتراک بگذارید.
همچنین لازم به ذکر است؛ برای خرید انواع مقاطع فولادی و بررسی قیمت روز آهن میتوانید به وبسایت عصرآهن (مرجع قیمت روز آهن) مراجعه کنید و یا با شماره 0414180 در تماس باشید. کارشناسان فروش در استعلام قیمت و خرید انواع مقاطع فولادی، راهنمای شما خواهند بود.
منبع: