فرآیند نورد یکی از پرطرفدارترین و بهترین روشها برای شکلدهی فولاد است و به دو روش نورد گرم و نورد سرد انجام میشود. نورد گرم و سرد باعث تولید محصولاتی با ویژگیها و کاربردهای متفاوت میشود. نورد گرم، با بهرهگیری از دماهای بالا، امکان تغییر ساختار داخلی فولاد و افزایش قابلیت شکلپذیری را فراهم میکند، در حالی که نورد سرد به دلیل انجام در دماهای پایینتر، دقت ابعادی و پرداخت سطحی بهتری ارائه میدهد.
در این مقاله، به بررسی جامع تفاوت نورد گرم و سرد خواهیم پرداخت و شما را با خواص و مزایا و معایب هر یک روشهای نورد میلگرد آشنا خواهیم کرد.
آشنایی با تعاریف نورد گرم و سرد
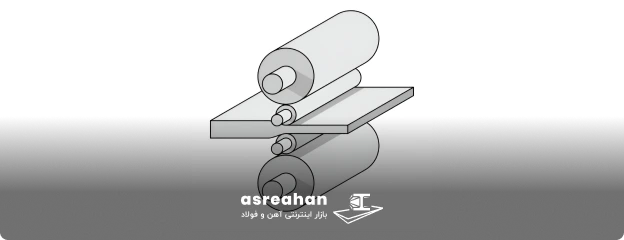
آیا تاکنون به این فکر کردهاید که تفاوت نورد گرم و سرد چیست؟ تفاوت اساسی بین این دو روش از همان دمای به کار رفته برای فرمدهی فولاد آغاز میشود. در ادامه مقاله، قصد داریم شما را با ویژگیها، مراحل، خواص فولاد تولید شده از آنها و مزایا و معایب این دو روش آشنا کنیم.
نورد گرم چیست؟
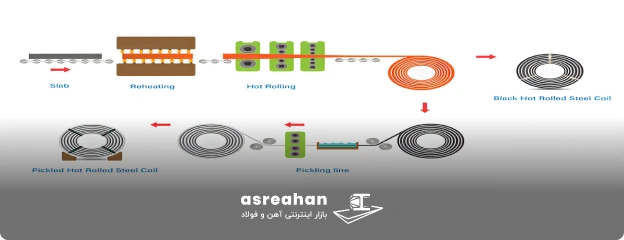
فرآیند نورد گرم فرآیندی است که در آن فلزات در دمایی بالاتر از دمای تبلور مجدد خود گرم میشوند تا به شکلدهی مطلوب دست یابند. در این روش، فلز گداخته از میان غلتکهای دوار عبور داده میشود تا ضخامت آن کاهش یافته و به ابعاد مورد نظر برسد.
مراحل نورد گرم
فرآیند نورد گرم شامل چند مرحله کلیدی است که در ادامه به بررسی آنها خواهیم پرداخت:
- آمادهسازی مواد اولیه
- گرم کردن مواد
- پوستهزدایی
- نورد کردن
- خنککاری
- برش و بستهبندی
ویژگی ها و خواص فولاد نورد گرم
فولاد نورد گرم، محصولی است که طی فرآیند نورد در دمایی بالاتر از دمای تبلور مجدد فلز تولید میشود. ویژگیها و خواص فولاد نورد گرم عبارتاند از:
- انعطافپذیری مناسب
- استحکام بالا
- مقاومت در برابر سایش
- مقاومت در برابر حرارت
- هزینه تولید کمتر
- تنش داخلی کم
کاربردهای نورد گرم
نورد گرم برای تولید لولهها، پروفیلهای سنگین مثل قوطی آهن و لوله گاز و بسیاری دیگر از مقاطع فولادی مورد استفاده قرار گیرد. از جمله این کاربردها میتوان به موارد زیر اشاره کرد:
- صنعت ساختمانسازی
- صنعت خودروسازی
- صنعت کشتیسازی
- صنایع نیرو
- ساخت قطعات ماشینآلات
مزایای نورد گرم
نورد سرد و نورد گرم هرکدام مزایای متفاوتی دارند که در این قسمت به بررسی مهمترین مزایای فرآیند نورد گرم میپردازیم:
- افزایش شکلپذیری و چکشخواری فلزات
- بهبود خواص مکانیکی فلزات
- هزینههای تولید کمتر
معایب نورد گرم
فرآیند نورد گرم، با وجود مزایای متعدد، معایبی نیز دارد که در ادامه به آنها پرداخته میشود:
- عیوب سطحی
- دقت ابعادی پایینتر
- محدودیتهای مواد
- مصرف انرژی بیشتر
نورد سرد چیست؟
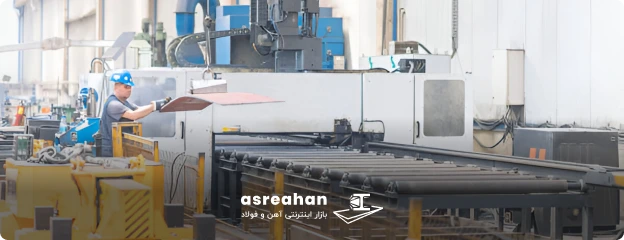
فرآیند نورد سرد فرآیندی است که به دنبال نورد گرم بر روی فولاد انجام میشود. در این مرحله، فولاد گرم نورد در دمای پایینتری مجدداً نورد میشود، یعنی از میان غلتکهای ویژه عبور داده میشود. این عملیات تنشهای مکانیکی را بر فلز اعمال میکند که به شکلدهی و تغییر فرم فولاد کمک میکند.
مراحل نورد سرد
در فرآیندهای تولید فولاد، نورد سرد نسبت به نورد گرم، مراحل بیشتری را شامل میشود:
- آمادهسازی مواد
- تغذیه مواد
- نورد اولیه
- نورد ثانویه و شکلدهی بیشتر
- پرداخت سطحی
- بررسی نهایی و کنترل کیفیت
- بستهبندی و ذخیرهسازی
ویژگی ها و خواص فولاد نورد سرد
ویژگیها و خواص فولاد نورد سرد عبارتاند از:
- نقطه تسلیم و توان کششی بالا
- افزایش سختی و استحکام
- بهبود سطح و دقت ابعادی
- افزایش مقاومت در برابر خوردگی
- کاهش قابلیت شکلپذیری
کاربردهای نورد سرد
با توجه به مزایای برتر، فرآیند نورد سرد در ساخت پلها، سیلوهای گندم، بدنه اتومبیلها، تاسیسات آب و فاضلاب، ساخت اسلحه، سیمهای برق فشار قوی مورد استفاده قرار میگیرد. در حالت کلی، کاربردهای این فرآیند عبارتاند از:
- صنعت خودروسازی
- صنعت ساختمانسازی و معماری
- صنعت برق و الکترونیک
- هوافضا و دفاع
- لوازم خانگی
مزایای نورد سرد
نورد سرد، فرآیندی است که به منظور بهبود خواص فلزات انجام میشود و مزایای متعددی را به همراه دارد. این مزایا، نورد سرد را به یک انتخاب محبوب در صنایع مختلف تبدیل کرده است. در ادامه، به برخی از مزایای کلیدی این فرآیند اشاره میکنیم:
- افزایش مقاومت فلز مورد نظر
- همگنسازی در سطح فلز
- کاهش وزن و بالا بردن خلوص فلز
- سهولت در نگهداری و تولید انبوه
- افزایش مقاومت فلز در مقابل موربیانه
- قابلیت د پوسیدگی فلز
- قابلیت بازیافت و استفاده مجدد آن در سطوح مختلف
- نصب آسان و سریع برای استفادههای مختلف
معایب نورد سرد
اگرچه نورد سرد مزایای بسیاری دارد، اما درک محدودیتها و چالشهای آن برای استفادهی بهینه از این فرآیند اهمیت زیادی دارد. در ادامهی این مطلب، به برخی از معایب نورد سرد اشاره خواهیم کرد.
- نامناسب برای مواد شکننده یا مواد با شکلپذیری پایین
- نامناسب برای اشکال پیچیده یا گوشههای تیز
- سایش و نگهداری ابزار و افزایش هزینههای عملیاتی
- هزینه تولید بالاتر
بررسی تفاوت نورد گرم و سرد از جوانب مختلف
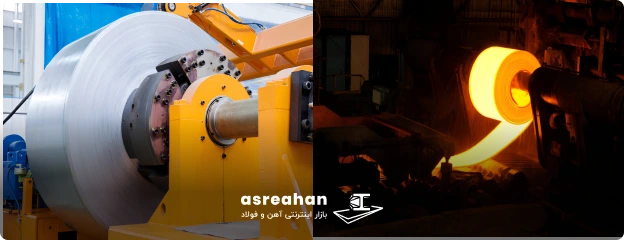
درک تفاوت نورد سرد و گرم برای انتخاب ورق فولادی مناسب ضروری است. این دو فرآیند، روشهایی برای تولید و پرداخت فولاد با ویژگیهای متمایز هستند که خواص و کاربردهای متفاوتی را به محصولات نهایی میبخشند. در ادامه، به بررسی مهمترین تفاوتهای نورد گرم و سرد میپردازیم.
تفاوت نورد سرد و گرم از نظر فرایند اجرای نورد
اصلیترین تفاوت نورد گرم و سرد، فرآیندی است که در هر کدام طی میشود. در روش نورد گرم، شمشهای فلزی با حرارتدهی بالا نرم شده و سپس از میان چندین غلتک عبور میکنند تا ضخامت آنها کاهش یابد. این فرآیند باعث ایجاد سطحی نسبتاً خشن و ناصاف در محصول نهایی میشود.
اما در نورد سرد، ابتدا همان مراحل اولیه حرارتدهی و عبور از غلتک انجام میشود و پس از خنک شدن، فلز تحت فشار مجدد در دمای پایین قرار میگیرد. این مرحله اضافی موجب بهبود خواص مکانیکی، افزایش استحکام و صافی سطح محصول میشود.
تفاوت نورد گرم و سرد از نظر دما و رفتار مواد
تفاوت نورد گرم و نورد سرد در دمای فرآیند و تأثیر آن بر خواص مکانیکی فلز نهفته است. نورد گرم در دماهای بالا، معمولاً بین ۹۰۰ تا ۱۳۰۰ درجه سانتیگراد، انجام میشود که در این شرایط، فلز به دلیل تبلور مجدد، انعطافپذیری بالاتری پیدا کرده و میتوان آن را بدون ایجاد ترک یا کاهش استحکام، به شکلهای مختلف درآورد. این فرآیند علاوه بر کاهش تنشهای داخلی، موجب بهبود همگنی ساختار و خواص مکانیکی فلز میشود.
در مقابل، نورد سرد در دمای محیط یا کمی بالاتر، معمولاً بین ۲۰ تا ۲۰۰ درجه سانتیگراد، انجام شده و فلز بدون تبلور مجدد، تغییر شکل میدهد. این فرآیند باعث افزایش سختی و شکنندگی فلز میشود، اما انعطافپذیری آن را کاهش میدهد. به همین دلیل، در بسیاری از موارد، برای بازگرداندن خاصیت شکلپذیری و کاهش تنشهای ایجادشده، فرآیند آنیلینگ پس از نورد سرد انجام میشود.
تفاوت نورد گرم و سرد از نظر کاربردهای محصولات تولید شده از طریق هر روش
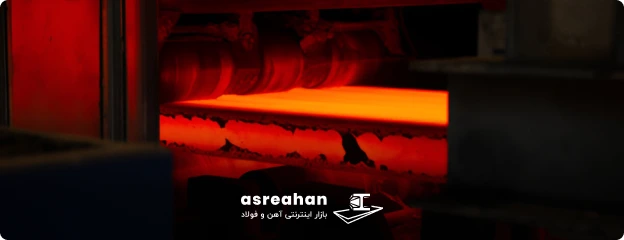
در فرآیند نورد گرم، به دلیل دمای بالای عملیات، دقت ابعادی کاهش یافته و سطح محصول از کیفیت پایینتری برخوردار هستند. به همین دلیل، این روش بیشتر برای تولید محصولاتی که نیاز به دقت بالا ندارند، مانند انواع فولادهای ساختمانی، مورد استفاده قرار میگیرد.
در مقابل، نورد سرد با بهبود خواص مکانیکی و افزایش دقت ابعادی، محصولاتی با کیفیت سطحی بهتر ارائه میدهد که آنها را برای کاربردهایی همچون تولید لوازم خانگی، ساخت لوله و استفاده در صنایع هوافضا مناسب میسازد.
تفاوت نورد گرم و سرد از نظر خواص محصولات نهایی
تفاوت نورد گرم با سرد در این است که در روش نورد گرم، محصولات در نتیجهی خنکشدن پس از اعمال دمای بالا، سطح خشنی دارند. علاوه بر این، به دلیل انقباض ناشی از سرد شدن سریع، دقت ابعادی کمتری دارند و ممکن است محصولات تولید شده در این روش اعوجاج جزئی داشته باشند.
در مقابل، محصولاتی که از فرآیند نورد سرد به دست میآیند، دارای کیفیت سطحی مناسب، تلرانس ابعادی کم، سطح صاف و بدون اکسید و استحکام بالایی هستند. تفاوت فولاد گرم نورد و سرد نورد در این است که فولاد سرد نورد، تلرانس ابعادی کمتری دارد و تا ۲۰ درصد سختتر و محکمتر از فولاد گرم نورد است.
تفاوت نورد سرد و گرم از نظر دقت ابعاد و پرداخت سطحی
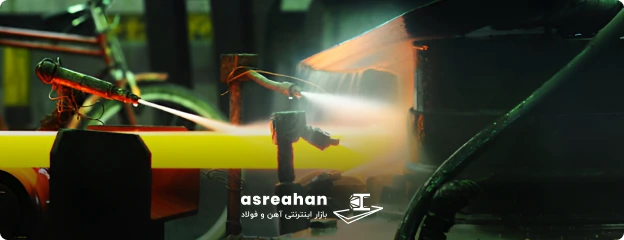
یکی از جنبههای کلیدی تفاوت نورد گرم و سرد، کنترل دقت ابعادی و پرداخت سطحی محصولات نهایی است. نورد گرم، با کاهش سریع ضخامت و سطح مقطع، برای تولید انبوه مناسب است. این فرآیند امکان تولید کارآمد ورقها و قطعات بزرگ را فراهم میکند. با این حال، به دلیل انبساط حرارتی و سایر عوامل مرتبط با دمای بالا، تغییرات ابعادی جزئی اجتنابناپذیر است.
همچنین، تشکیل رسوب و اکسیداسیون در دمای بالا، سطحی زبرتر نسبت به محصولات نورد سرد ایجاد میکند. در مقابل، نورد سرد در کنترل ابعادی برتری دارد و دقت بالایی در ضخامت، عرض و طول ارائه میدهد. این فرآیند امکان تولید ورقهای نازکتر و مقاطع کوچکتر با یکنواختی عالی را فراهم میکند. این فرآیند سطح صاف و صیقلی ایجاد میکند که آن را برای کاربردهایی که زیبایی و کیفیت سطح اهمیت دارند، مناسب میسازد.
تفاوت نورد گرم و سرد از نظر تجهیزات و ماشین آلات مورد نیاز
تفاوت نورد گرم و سرد در تجهیزات و ماشینآلات مورد استفاده در هر کدام قابل مشاهده است.
در نورد گرم، آسیابها با غلتکهای نورد بزرگی ساخته میشوند که توسط موتورهای قوی به حرکت درمیآیند و توانایی تحمل دما و نیروهای بالا را دارند.
اما در نورد سرد، آسیابها فشردهتر و چندمنظورهتر هستند و برای تولید مواد نازکتر و کاهش دقیق ضخامت طراحی شدهاند.
تفاوت نورد سرد و گرم از نظر بهرهوری، کارایی و هزینه ها

تفاوت نورد سرد و نورد گرم در بازدهی تولید و میزان هزینه، عملکرد آنها را به شدت تحت تاثیر قرار میدهد. نورد گرم، به دلیل سرعت بالا و مصرف انرژی کمتر، برای تولید انبوه مناسبتر و مقرون به صرفهتر است.
در مقابل، نورد سرد با وجود سرعت پایینتر، مزایایی مانند صرفهجویی در مواد و کاهش ضایعات را به همراه دارد. دقت ابعادی بالا و کیفیت سطح مطلوب در نورد سرد، نیاز به فرآیندهای تکمیلی را کاهش داده و در نتیجه، از هدر رفت مواد جلوگیری میکند. با این حال، به دلیل کار بیشتر و انرژی مصرفی بالاتر، نورد سرد هزینههای بیشتری را نسبت به نورد گرم در پی دارد.
تفاوت نورد سرد و گرم از نظر مناسب بودن مواد
انتخاب بین نورد سرد و نورد گرم به طور مستقیم به نوع ماده و کاربرد نهایی آن بستگی دارد. به طور کلی، تفاوت نورد گرم و سرد در خواص مکانیکی و ظاهری محصول نهایی مشهود است.
نورد گرم برای موادی که به راحتی تغییر شکل نمیدهند و نیاز به خواص مکانیکی اصلاح شده دارند، مناسب است و معمولاً برای شکلدهی به شمشها و بیلتها به کار میرود.
در مقابل، نورد سرد، که دقت ابعادی بالا و پرداخت سطحی عالی را فراهم میکند، در تولید ورقهای نازک، قطعات دقیق و محصولاتی با کیفیت سطحی بالا کاربرد گستردهای دارد.
تفاوت نورد گرم و سرد از نظر ملاحظات متالورژی
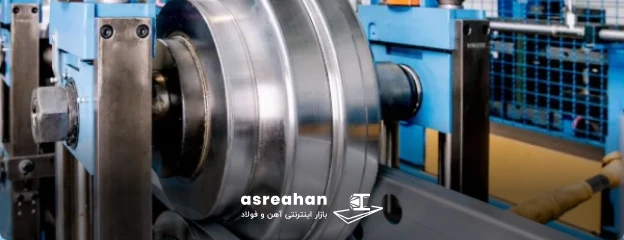
فرق نورد سرد و گرم نهتنها در دمای فرآیند، بلکه در ویژگیهای متالورژیکی آنها نیز مشهود است. در نورد گرم، قرار گرفتن مواد در دماهای بالا باعث تغییر در ریزساختار، رشد دانهها و حتی اکسیداسیون سطحی میشود.
در مقابل، نورد سرد که در دماهای پایینتری انجام میشود، این تغییرات را به حداقل رسانده و موجب حفظ خواص مکانیکی و ساختاری ماده میگردد.
تفاوت نورد گرم و سرد از نظر اکسیداسیون سطحی
در بررسی تفاوت نورد گرم و سرد، مواد نورد گرم در طی فرایند دچار اکسیداسیون شده و لایهای رسوبی بر روی آنها به وجود میآید که ممکن است کیفیت نهایی سطح ماده را تحت تأثیر قرار داده و نیاز به تمیز کاری اضافی ایجاد کند.
در مقابل، مواد نورد سرد به دلیل داشتن سطحی صافتر و مقاومت بیشتر در برابر اکسیداسیون، معمولاً از رسوببندی رهایی یافته است و نیاز به پاکسازی اضافی ندارد.
تفاوت نورد سرد و گرم از نظر ویژگی های مکانیکی
نورد گرم و نورد سرد، خواص مکانیکی متفاوتی را در مواد نورد شده ایجاد میکنند. به طور کلی، مواد نورد گرم شده، علیرغم دقت ابعادی پایین، استحکام بالایی دارند. در حالی که مواد نورد سرد شده، به دلیل ساختار سختشدهشان، شکنندگی کمتر و دقت ابعادی بیشتری را ارائه میدهند.
تفاوت نورد سرد و گرم از نظر قیمت محصولات نهایی
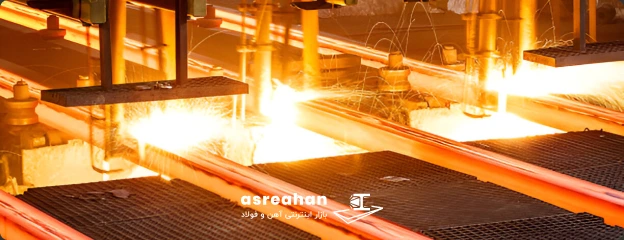
فرآیند نورد سرد، به دلیل دقت و زمان صرف شده بیشتر، محصولی با کیفیت سطح بالاتر و با خواص مکانیکی مطلوبتر ارائه میدهد. این مزایا، به طور طبیعی، منجر به افزایش قیمت آهن آلات تولید شده به روش نورد سرد میگردد. این اختلاف قیمت، یکی از بارزترین تفاوت های نورد گرم و سرد محسوب میشود.
به عبارت دیگر، تفاوت نورد گرم و سرد نه تنها در کیفیت، بلکه در قیمت ورق آهن یا ورق گالوانیزه نیز مشهود است. به طور کلی، عواملی مانند زمان تولید، دقت فرآیند و کیفیت سطح، تعیینکننده قیمت آهن آلات نورد سرد در مقایسه با نورد گرم هستند.
تفاوت نورد گرم و سرد از نظر تفاوت در مزایای هر روش
برای درک تفاوت نورد گرم و سرد، باید به مزایای منحصر به فرد هر روش نگاه کرد. نورد گرم، با توانایی شکلدهی قطعات بزرگ و اولیه مانند شمشها و بیلتها، انتخاب مناسبی برای تولیدات حجیم است.
در مقابل، نورد سرد با ارائه دقت ابعادی بالا، سطحی صاف و صیقلی، صرفهجویی در مصرف مواد و کنترل دقیق تلرانس، برای تولید قطعات ظریف و دقیق مناسب است. تصمیمگیری در مورد انتخاب بین این دو روش، یعنی درک تفاوت نورد سرد با گرم، بستگی به مشخصات نهایی محصول، نیازهای خاص صنعت و ملاحظات اقتصادی دارد.
تفاوت نورد گرم و سرد از نظر تفاوت در معایب هر روش
در این بخش از مقاله، تمرکز ما به بررسی تفاوت نورد گرم و سرد از جنبه معایب است. در روش نورد گرم، عیوب ابعادی، ساختار ناهموار و خشن و تلرانس ضعیف به عنوان نقاط ضعف این فرآیند مطرح میشوند.
در مقابل، نورد سرد با معایبی نظیر قیمت بالاتر محصولات، تنشهای داخلی، نیاز به عملیات تکمیلی بیشتر و محدودیت در کاهش شدید ضخامت و سطح مقطع همراه است.
جدول خلاصه تفاوت نورد سرد و گرم
برای درک بهتر تفاوت نورد گرم و سرد، میتوانید به جدول زیر که خلاصهای از تفاوتهای این دو روش را نشان میدهد، توجه کنید.
فرآیند | نورد گرم | نورد سرد |
فرآیند تولید | انجام در دمای بالا (۱۳۰۰ - ۹۰۰ درجه سانتی گراد)، عبور از غلتکها برای کاهش ضخامت | انجام در دمای پایینتر (۲۰۰ - ۲۰ درجه سانتی گراد) پس از نورد گرم، قرار گرفتن تحت فشار مجدد |
دما و رفتار مواد | انعطافپذیری بالا، امکان تغییر شکل آسان، کاهش تنشهای داخلی | افزایش سختی و استحکام، کاهش انعطافپذیری |
کیفیت سطح | سطح خشن و دارای اکسیداسیون | سطح صاف، صیقلی و بدون اکسید |
دقت ابعادی | دقت کمتر، امکان تغییر ابعاد حین سرد شدن | دقت بالا، تلرانس ابعادی کم |
خواص مکانیکی | مقاومت کمتر، استحکام معمولی، انعطافپذیری بالا | استحکام بالاتر، سختی بیشتر، شکنندگی بالاتر |
کاربردها | فولادهای ساختمانی، تیرآهن، میلگرد | صنایع خودروسازی، هوافضا، لوازم خانگی، لولهسازی |
تجهیزات مورد نیاز | آسیابهایی با غلتکهای بزرگ، با توانایی تحمل دما و نیروهای بالا | آسیابهای فشردهتر و چند منظورهتر، مناسب برای تولید ورقهای نازک |
هزینه تولید | ارزانتر، سرعت بالا، مصرف انرژی کمتر | گرانتر، سرعت کمتر، با کاهش ضایعات و دقت بیشتر |
ملاحظات متالورژی | رشد دانهها، اکسیداسیون سطحی، همگنی بیشتر در ساختار | حفظ ساختار ریزدانهای، کنترل بهتر خواص مکانیکی |
اکسیداسیون سطحی | تشکیل لایه اکسیدی نیازمند تمیزکاری | سطح صاف و بدون نیاز به تمیز کاری اضافی |
قیمت محصولات نهایی | ارزانتر به دلیل فرآیند سادهتر | رانتر به دلیل دقت و کیفیت بالاتر |
نحوه تشخیص محصولات نورد گرم و سرد
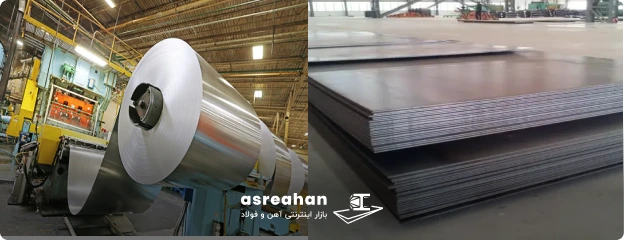
محصولات فولادی به دو روش نورد گرم و سرد تولید میشوند که هر کدام ویژگیهای منحصر به فرد و کاربردهای خاص خود را دارند. محصولات تولید شده به روش نورد گرم دارای سطحی ناهموار و زبر، لبههای غیر یکنواخت، رنگ مات و تیره، ابعاد با دقت کمتر و استحکام کمتر نسبت به نورد سرد هستند.
از جمله این محصولات میتوان به ورق سیاه، ورقهای پوششدار (گالوانیزه، رنگی، اسیدشویی و غیره)، پروفیلهای باز (نبشی، ناودانی، تیرآهن) و پروفیلهای بسته (لوله، قوطی، میلگرد) اشاره کرد.
در مقابل، محصولات تولید شده به روش نورد سرد دارای سطحی صاف و صیقلی، لبههای تیز و یکنواخت، رنگ روشن و براق، ابعاد با دقت بالا و استحکام بیشتر نسبت به نورد گرم هستند. انواع ورق روغنی، ورق گالوانیزه، ورق قلع اندود، پروفیلهای باز (ناودانی) و پروفیلهای بسته (لوله) از جمله این محصولات هستند. برای تشخیص این دو نوع محصول، میتوان به کیفیت سطح، لبهها، رنگ، دقت ابعادی و استحکام آنها توجه کرد.
محصولات نورد گرم بیشتر در ساخت سازههای سنگین، تولید قطعات صنعتی و صنایع کشتی سازی کاربرد دارند، در حالی که محصولات نورد سرد در تولید قطعات خودرو، لوازم خانگی و صنایع ساختمان سازی که دقت بالا مورد نیاز است، مورد استفاده قرار میگیرند. به عنوان مثال، قیمت میلگرد امروز تولید شده به روش نورد گرم به دلیل فرآیند تولید سادهتر و هزینه کمتر مواد اولیه، معمولاً پایینتر از نورد سرد است.
جمع بندی
تفاوت نورد گرم و سرد را میتوان از جنبههای مختلفی از جمله نوع فرآیند تولید، خواص مکانیکی و فیزیکی، کاربردها، مزایا، معایب و قیمت بررسی کرد. نورد گرم فرآیندی است که در آن فلز در دمای بالا، معمولاً بالاتر از دمای تبلور مجدد، شکلدهی میشود.
در مقابل، نورد سرد در دمای محیط یا نزدیک به آن انجام میشود و به دلیل کاهش تغییرات ساختاری در فلز، دقت ابعادی و کیفیت سطحی بالاتری دارد. بهطور کلی، اگر هزینه کمتر و تولید انبوه مدنظر شما باشد، نورد گرم انتخاب بهتری است، اما اگر دقت ابعادی بالا، مقاومت بیشتر و ظاهر بهتر موردنیاز باشد، نورد سرد گزینه مناسبتری خواهد بود.