رابطه مستقیم شمش فولادی و تولید میلگرد
شمش یکی از مقاطع بسیار مهم برای تولید انواع میلگردها و سایر محصولات فولادی به حساب میآید. پس از استخراج آهن و تولید فولاد خام، شمش اولین محصول قابل حمل در فرایند فولادسازی میباشد که به صورت جامد و در ابعاد کوچک، قابل جابهجایی میباشد. در واقع میتوان گفت، فرآیند شمش سازی، یکی از فرآیندهای میانی نورد فولاد است که ماده اولیه صنایع پایین دست به حساب میآید. شمشها در انواع مختلف و با ویژگیهای متفاوتی تولید میشوند که در ادامه این مطلب، انواع شمش برای تولید میلگرد را معرفی میکنیم.
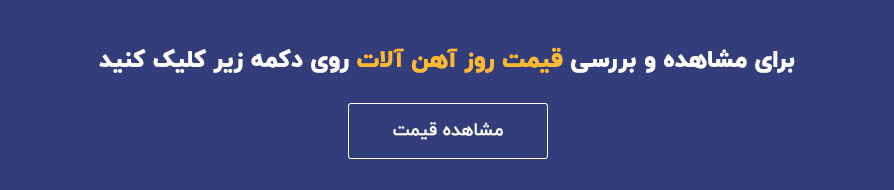
جایگاه شمش در زنجیره تولید میلگرد
زنجیره تولید میلگرد، شامل 4 مرحله کلی میباشد که یکی از مهمترین آنها تولید شمش است. این مقاطع را میتوان از لحاظ ساختار شیمیایی و فیزیکی در دستههای مختلفی دستهبندی کرد که هر کدام دارای ویژگیهای متفاوتی هستند. از این محصولات، در جهت تولید انواع کالاها، مانند میلگرد، تیراهن، مفتول و ... استفاده میشود. به طور کلی، شمشها به صورت ذوزنقه تولید میشوند و در طول 2 متری عرضه میشوند که این امر موجب حمل و نقل آسان آنها شده است. از انواع شمش برای تولید میلگرد فولادی، میتوان به موارد زیر اشاره کرد.
- شمش CCM یا بیلت
- شمشهای فابریک
- شمش بلوم
بخوانید: زنجیره فولاد | صنایع دخیل در ساخت فولاد کشور و اهمیت آنها در تولید فولاد
مشخصات انواع شمش برای تولید میلگرد
شمشهای فولادی، قطعاتی مستطیل شکل هستند که سطح مقطع آنها به دلیل قالبگیری دستی، سهولت در خارج کردن از قالب و حمل و نقل آنها به صورت ذوزنقه میباشد و طول هر شاخه از آنها، حداکثر به دو متر میرسد. این شمشها را عمدتا در کارگاههای کوچک تولید میکنند. شمشها عمدتا در انواع بلوم، بیلت و یا اسلب تقسیمبندی میشوند و همچنین در گریدهای مختلفی نیز تولید میشوند که این عبارت گرید، نشان دهنده متریال استفاده شده، برای تولید شمشها میباشد.
به طور مثال، گرید 3SP-5SP (تحت استاندارد روسیه) و St37-St52 (تحت استاندارد آلمان) از مشهورترین گریدهای شمشهای فولادی میباشد که با وجود درصدهای مختلف از عناصر موجود در فولاد ساخته شدهاند و دارای خواص مکانیکی متفاوت مانند انعطافپذیری، خمش، کشش و پیچش بوده و کاربردهای متفاوتی دارند. در ادامه انواع شمش برای تولید میلگرد را تعریف میکنیم.
شمش بیلت
شمشال یا همان بیلت، یکی از انواع شمش برای تولید میلگرد میباشد که به روش CCM تولید شده و به صورت مستقیم، از تولید به مصرف میرسد. بیلت طول بیشتری نسبت به سایر شمشها دارد و معمولا با شکل دایره یا مربع و با عرض کمتر از 15 سانتی متر و سطح مقطع کوچکتر از 230 سانتی متر مربع میباشد.
بلوم
یکی دیگر از انواع شمش برای تولید میلگرد فولادی، بلوم یا شمشه میباشد که شباهت بسیار زیادی به بیلت دارد. در واقع تنها تفاوت بین این دو نوع، در سطح مقطع آنها است. اگر سطح مقطع بیلت از 320 و عرض آن نیز از 15 بیشتر باشد، به آن بلوم میگویند. از این شمشها علاوه بر تولید میلگرد، برای ساخت ریل، قوطی و تیرآهن نیز استفاده میکنند.
اسلب
اسلبها شکل ظاهری متفاوتی نسبت به سایر انواع شمش برای تولید میلگرد دارند. در واقع شکل این شمشها مسطتیلی است و دارای ضخامت 230 میلی متر، عرض ۱.۲۵ متر و طول ۱۲ متر میباشد. تختال یا همان اسلب، برای ساخت ورقهای فولادی استفاده میشود و میزان کربن موجود در آنها، تعیین کننده میزان نرمی و کشش آن میباشد.
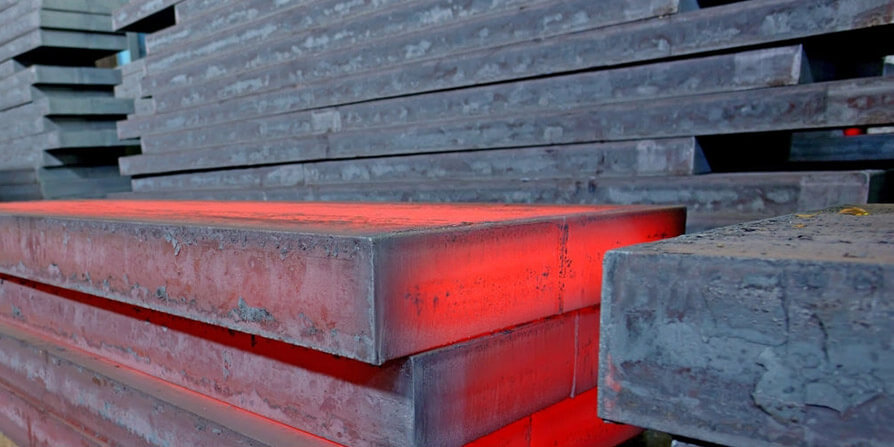
انواع شمش برای تولید میلگرد از لحاظ گرید
شمشهای فولادی از لحاظ میزان کربن موجود در آنها، در گریدهای 3SP و 5SP تولید میشود که هر کدام ویژگیهای خود را دارد. از این ویژگیها، میتوان به منعطف بودن شمشها با گرید 3SP اشاره کرد که در صنایعی که نیاز به خمش، کشش و انعطاف بیشتری هستند، استفاده میشود و البته قیمت بالاتری هم نسبت به شمشها 3SP دارند.
همچنین شمشهای 5SP یکی دیگر از انواع شمشها میباشند که دارای انعطافپذیری بسیار کمتری میباشند و در مواقعی که سازه تحت معرض نیرو و فشار نیست، استفاده میشود. این نوع از شمشها دارای قیمت ارزانتری نسبت به شمشهای با گرید 3SP هستند.
استفاده از انواع شمش برای تولید میلگرد
یکی از اصلیترین موارد برای تولید میلگرد، میزان کربن موجود در شمشها و آنالیز آن است. برای تولید میلگردهای با سایز پایین (14 تا 40)، از شمشهای با کربن 30 تا 35 استفاده میشود. همچنین برای ساخت میلگردهای با سایزهای پایینتر، به دلیل نیاز به نرمی و کشش بیشتر، از شمش کم کربن استفاده میکنند.
شمشهای 100، 120، 125، 130، 150 و 160 جز بیلتها محسوب میشوند و برای تولید میلگرد فرق زیادی با یکدیگر ندارند.180*180، 200*200 و 250*250 را نیز بلوم مینامند که از آنها بیشتر برای تولید میلگردهای صنعتی استفاده میشود.
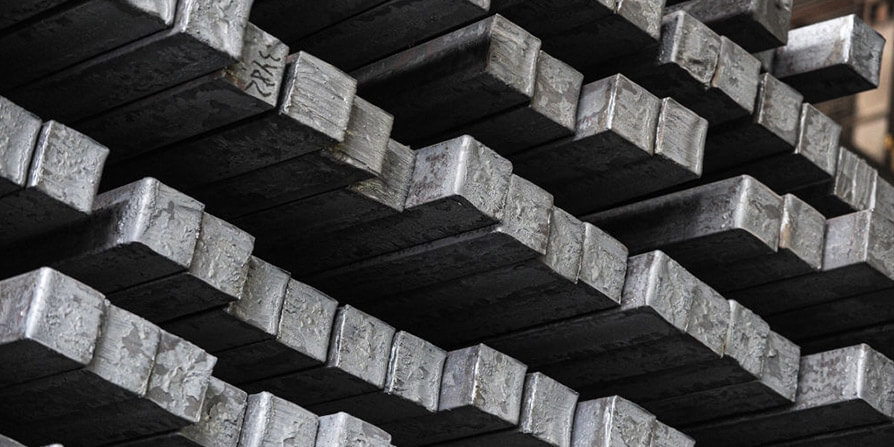
شمشهای برخی از کارخانههای تولید میلگرد، با توجه به خط نورد خود، از مدل 150 میباشد و در برخی دیگر از کارخانهها هم از شمش 125 استفاده میشود. همچنین، امروزه برخی از کاخانههای مدرن، از ترکیب انواع شمش برای تولید میلگرد استفاده میکنند. در واقع مواد اصلی استفاده شده برای ساخت میلگردها، به خط تولید کارخانجات نیز بستگی دارد. اما به طور کلی برای میلگردهایی ریز، از شمش 120 و یا 130 و برای ساخت میلگردهای درشتتر نیز از شمشهای 150 استفاده میکنند. همچنین لازم به ذکر است، در برخی از شرکتها، با توجه به خط نوردی که دارند، برای ساخت میلگردهای ریز هم از شمشهای 150 استفاده میکنند و آرماتورهای با سایز 8، 10 و یا حتی کلافها را تولید میکنند.
در ایران، با توحه به اینکه خط نوردها قدیمی هستند، فقط شمشهای و یا حداکثر 130 برای تولید میلگرد استفاده میکنند و قابلیت تولید میلگرد با استفاده از شمشهای 150 را ندارند.
تفاوت انواع شمش برای تولید میلگرد
شمشها در انواع مختلفی تولید میشوند که هر کدام دارای تفاوتهای بسیار زیادی هستند. این شمشها در بازار و بورس عرضه میشوند و بهتر است قبل از خرید، با تفاوتهای آنها آشنا شوید. در ادامه تقاوتهای شمش بلوم و بیلت را بیان میکنیم.
شمش بلوم و بیلت
شمشهای بلوم، اکثرا برای ساخت میلگردهای صنعتی استفاده میشوند. همچنین در برخی از کشورها، به دلیل تولید بسیار بالای فولاد و عدم توزان و ظرفیت دستگاه ccm و در برخی از موارد، به دلیل درخواست مشتریان، شمشهای بلوم در سایزهای 180 به بالا تولید میشود و پس از یک مرحله نورد، به ابعاد شمش بیلت به پایین تبدیل میشود.
از دیگر تفاوتهای این دو نوع شمش، میتوان به تفاوت چگالی آنها اشاره کرد. شمشهای بیلت دارای چگالی بالاتری دارد و بیشتر برای مصارف صنعتی کاربرد دارد. شمشهای 3sp با کربن حداکثر 22 درصد، برای تولید نبشی و ناودان و در برخی از موارد، در سایزهای میلگردهای ریز استفاده میشود. مقاطع 5sp، یکی از انواع شمش برای تولید میلگرد تا سایز 25 میباشد. البته لازم به ذکر است که برای تولید میلگردهای با سایز 25 به بالا، اغلب از شمشهای با گرید Gr60 میشود. همچنین برای تولید انواع کلاف نیز از شمشهای با گرید 5sp،Rst34 ، 1006، 1008 استفاده میکنند.
انواع شمش فولادی از لحاظ روش تولید
انواع شمش برای تولید میلگرد فولادی، از لحاظ روش تولید نیز متفاوت میباشد و میتوان آنها را به دو دسته تقسیم بندی کرد که در ادامه این روشها را معرفی میکنیم.
روش کوره بلند BF
تقربا میتوان گفت، بیش از 90 درصد از سنگ آهن، به روش سنتی کوره بلند ذوب میشود. سنگ آهن بیش از پخت و کلوخهسازی به همراه آهک و کک داخل کوره بلند ریخته میشود. آهن در کانورتر به فولاد مذاب تبدیل میشود . ناخالصیهای آن نیز مانند کربن به وسیله اکسیژن از آن جدا میشود. قولادهای مذاب به پاتیل حمل منتقل میشود و به واحد ریختهگری انتقال داده میشود. در این واحد، مواد داخل قالبهای شمش ریخته و بر روی غلطکی قرار داده میشود و با پاشیده شدن آب سرد، اقدام به خنکسازی آن میکنند. سپس شمش فولاد را به دلخواه برش میزنند.
کورههای قوس الکتریکی و کوره القایی
آهنهای قراضه با استفاده از سبدهای مخصوص، به داخل کورهها هدایت میشوند و بعد از آن، آهن اسفنجی همراه با سرباره مانند آهک، کک و بنونیت از بالا به داخل کوره ریخته میشود. پس از آن، فرآیندهایی مانند نمونهگیری، دمیدن اکسیژن، همگام سازی انجام میشود. مخلوط مذاب را توسط پاتیل حمل به واحد ریختهگری میبرند. ظروف را بر روی غلطک قرار میدهند و با استفاده از آب سرد آن را خنک میکنند تا شمش منجمد شود و آن را در ابعاد خاص، برش دهند.
ظرفیت کوره القایی، از یک کیلوگرم تا تن میباشد، اما در این روش، امکان تصفیه مذاب وجود ندارد و شمش تولیدی از نظر آنالیز دارای پراکندگی بسیار زیادی است. اما در کوره قوس، امکان آنالیز وجود دارد و عناصر مضر مانند گوگرد و فسفر در آن کمتر میباشد. همچنین لازم به ذکر است، در کوره قوس، میتوان شمشهای کم کربن نیز تولید کرد. با توجه به همین موضوع، کیفیت شمشهای حاصل از کورههای به روش قوس الکتریکی از کیفیت بسیار بالاتری نسبت به کوره الکتریکی برخوردار است.
روش کوره تونلی
این روش، در واقع احیای آهن در حالت جامد و به کمک کربن میباشد . این شیوه نسبت به دو روش قبلی، نوینتر، به حساب میآید و احداث واحدهای صنعتی، با این روش، در دستور کار قرار دارد اما در حال حاضر، تولیدکنندگان بزرگی در کشور از این روش استفاده نمیکنند.
قیمت انواع شمش برای تولید میلگرد چگونه تعیین میشود؟
قیمت انواع شمش برای تولید میلگرد به صورت روزانه تعیین میشود. در گذشته، شمش فولاد خوزستان تعیین کننده قیمت این مقاطع بود. اما با توجه به مشکلاتی که در این نوع از قیمتگذاری وجود داشت که از جمله آنها میتوان به دولتی بودن و شفاف نبودن قیمت این واحد تولیدی، در آخرین جلسه با ذوبیها، قرار بر این شد که ملاک قیمتگذاری شمش، سایر تولید کنندگان خصوصی آن مانند کیان و پاسارگاد باشد.
بخوانید: آشنایی با فرایند آنیلینگ فولاد
سخن پایانی
در این مطلب از وبسایت عصر آهن، انواع شمش برای تولید میلگرد را معرفی کردیم. امروزه با توجه به استفادههای بسیار زیاد از آرماتورها، برای افزایش کاربری، میلگردها در انواع مختلفی تولید میشوند. همچنین برای تولید هر یک از آنها، از متریال مخصوصی نیز استفاده میکنند. تا بتوانند میلگردی متناسب با نیازهای بازار تولید کنند. شمشهای فولادی یکی از مهمترین این مواد اولیه است و برای انتخاب بهتر میلگرد مورد نیاز بهتر است علاوه بر شناخت انواع آرماتور، با انواع شمش برای تولید میلگرد نیز آشنایی داشته باشید.