میلگرد یکی از مهمترین محصولات فولادی در صنعت ساختوساز است که فرآیند تولید آن تأثیر مستقیمی بر کیفیت، استحکام و قیمت نهایی محصول دارد. فرآیند تولید میلگرد شامل مراحل مختلفی مانند تهیه مواد اولیه، ذوب، ریختهگری، نورد و عملیات حرارتی است که هر کدام نقش مهمی در شکلدهی و بهبود ویژگیهای مکانیکی میلگرد ایفا میکنند. روشهای مختلفی برای تولید میلگرد وجود دارد، ازجمله نورد گرم، نورد سرد، ترمکس و میکرو آلیاژی، که هرکدام مزایا و کاربردهای خاص خود را دارند.
در این مقاله، جزئیات کامل مراحل تولید میلگرد، استانداردهای لازم و روشهای متداول ساخت آن در ایران و سایر کشورها را بررسی خواهیم کرد.
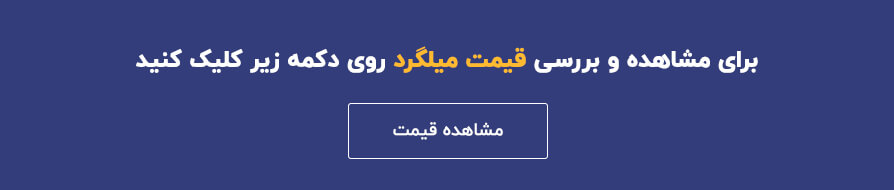
فیلم تولید میلگرد
مشاهده فیلم تولید میلگرد از نزدیک میتواند درک بهتری از مراحل مختلف این صنعت فراهم کند. در ویدیوی زیر، میتوانید روند تولید میلگرد را از مرحله ذوب مواد اولیه تا شکلدهی و بستهبندی نهایی مشاهده کنید.
اهمیت تولید میلگرد و استفاده از آن
میلگرد یکی از اساسیترین مصالح در صنعت ساختوساز است که نقش حیاتی در افزایش استحکام و دوام سازههای بتنی دارد. بتن بهتنهایی در برابر نیروهای فشاری مقاوم است، اما در برابر نیروهای کششی ضعف دارد؛ اینجاست که میلگرد با افزایش مقاومت کششی، موجب تقویت بتن و افزایش پایداری سازه میشود. این محصول در انواع مختلف و با روشهای متنوعی تولید میشود که هرکدام ویژگیهای خاصی دارند.
انتخاب نوع میلگرد مناسب، به عواملی مانند میزان بار وارد شده به سازه، شرایط محیطی و نوع طراحی بستگی دارد. این موضوع تنها مختص ساختمانهای مرتفع یا پروژههای بزرگ عمرانی نیست، بلکه حتی در ساخت فضاهای کوچک مانند انبارها و دیوارهای بتنی نیز استفاده از میلگرد استاندارد و مناسب اهمیت بالایی دارد. بنابراین، شناخت روشهای تولید میلگرد و استانداردهای مختلف آن، میتواند به انتخاب بهینه و افزایش دوام سازه کمک کند.
مواد اولیه مورد نیاز برای تولید میلگرد
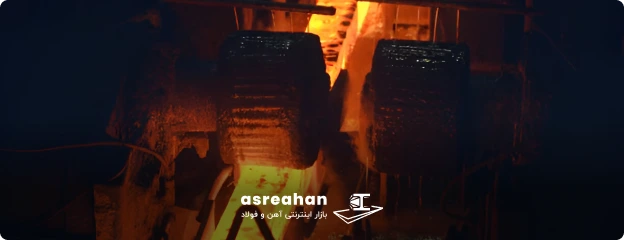
میلگرد یکی از اجزای اصلی در ساختوساز است که از فولاد ساخته میشود. فولاد، آلیاژی از آهن و کربن است که میتواند با سایر عناصر مثل منگنز، کروم، نیکل، مولیبدن و غیره ترکیب شود تا ویژگیهای خاصی پیدا کند. فرایند تولید میلگرد با تولید شمش فولادی در کورههای ذوب آغاز میشود. این شمشها ممکن است از فولاد کربنی، آلیاژی، ضد زنگ، فولاد ابزار یا فولاد الکتریکی ساخته شوند.
هر نوع شمش فولادی ویژگیها و ترکیب شیمیایی خاص خود را دارد. برای مثال، فولاد آلیاژی مقاومت بیشتری، سختی بالاتر، قابلیت جوشپذیری بهتر و مقاومت بیشتری در برابر خوردگی و سایش دارد. پس از تولید شمش فولادی، آن را در کورههای پیشگرم کننده گرم کرده و سپس به دستگاههای نورد ارسال میکنند. در این دستگاهها، شمش تحت فشار قرار میگیرد و به شکل میلگرد با اندازه دلخواه در میآید.
نحوه تولید میلگرد
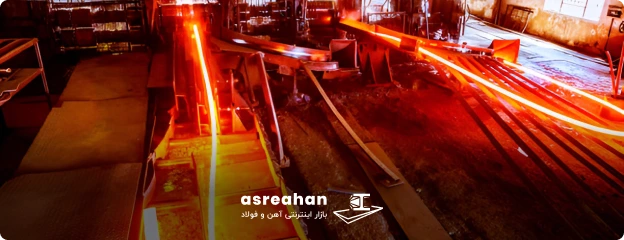
پروسه تولید میلگرد یک فرآیند پیچیده است که شامل چندین مرحله مختلف میشود. این مراحل بهطور مستقیم بر کیفیت و ویژگیهای نهایی میلگرد تأثیر میگذارند. همچنین، روشهای مختلفی برای تولید میلگرد وجود دارد که هرکدام ویژگیهای خاص خود را دارند. در ادامه این قسمت بهطور کامل به بررسی مراحل و انواع روش ساخت میلگرد خواهیم پرداخت و جدولی برای مقایسه انواع روش ساخت ارائه خواهیم کرد.
مراحل تولید میلگرد
مراحل ابتدایی تولید میلگرد در اکثر روشهای تولید آن شباهت زیادی به یکدیگر دارند. در این مرحله ابتدا مواد اولیه که معمولاً شامل فولاد کربنی یا ضایعات آهنی است، بهطور کامل ذوب میشوند. پس از ذوب شدن فولاد، آن را به شمش تبدیل میکنند.
در واقع، اولین گام مشترک در تمام روشها، تبدیل فولاد مذاب به شمش است. پس از این مرحله، شمشهای تولیدی کشیده شده و طول آنها افزایش مییابد و به شکل استوانهای در میآید.
برای تبدیل مواد مذاب به شمش، دو روش اصلی وجود دارد که به شرح زیر است.
- ریختهگری در قالبهای آماده: در این روش، فولاد مذاب در قالبهای از پیش ساخته شده ریخته میشود. پس از سرد شدن، شمشهای فولادی از قالبها جدا شده و به مراحل بعدی منتقل میشوند. این روش، بیشتر در کارخانههای کوچکتر مورد استفاده قرار میگیرد.
- ریختهگری مداوم: در این روش، فولاد مذاب از پاتیلها به محفظهای با چندین خروجی هدایت میشود که که در زیر هرکدام از این خروجیها باز یک محفظه قرار میگیرد که سایزی برابر با شمش دلخواه تولیدی دارند. مواد مذاب، به تدریج وارد محفظههای پایینتر شده و به دمای انجماد میرسند.
شمش فولادی، به صورت پیوسته از محفظهها خارج شده و توسط غلتکها صاف و صیقلی میشود. این روش، به دلیل تولید پیوسته شمش، به ریختهگری مداوم معروف است و بیشتر در کارخانههای بزرگ با ظرفیت تولید بالا استفاده میشود.
انواع روش تولید میلگرد
یکی از مهمترین فاکتورهایی که بر خصوصیات میلگرد تأثیر میگذارد، روش تولید آن است. هر روش تولید میتواند ویژگیهای خاصی مانند استحکام، سختی، و انعطافپذیری متفاوتی را به میلگرد بدهد. به همین دلیل، درک روش تولید میلگرد میتواند به درک ویژگیهای آن و تعیین کاربردهای آن در صنایع مختلف کمک کند.
بهطورکلی، چهار روش عمده برای تولید میلگرد وجود دارد که فرآیند ابتدایی در همه آنها مشابه است، اما تفاوتهای اصلی در مرحله نهایی و نوع مواد اولیه مورد استفاده است.
تولید میلگرد به روش نورد گرم
تولید میلگرد به روش نورد گرم یکی از اصلیترین روشها برای تولید مقاطع فولادی مانند میلگرد است که بهدلیل تاثیر آن بر ساختار و خواص فلز، در صنایع مختلف کاربرد گستردهای دارد. در این فرآیند شمشهای فولادی در دمای بسیار بالا، معمولاً بین ۵۰۰ تا ۱۰۰۰ درجه سانتیگراد، حرارت داده میشوند تا قابلیت شکلدهی پیدا کنند.
در فرآیند نورد میلگرد، فلز از بین دو غلتک با فاصلهای کمتر از ضخامت اولیهاش عبور میکند و به میلههایی با قطر کوچکتر و طول بیشتر تبدیل میشود. برای ایجاد آج روی سطح میلگرد، از غلتکهایی استفاده میشود که بهطور خاص برای این منظور طراحی شدهاند. این فرآیند نهتنها به بهبود ویژگیهای مکانیکی فلز کمک میکند، بلکه از مهمترین روشها برای تولید مقاطع یکنواخت و باکیفیت در صنعت فولاد است.
تولید میلگرد به روش نورد سرد
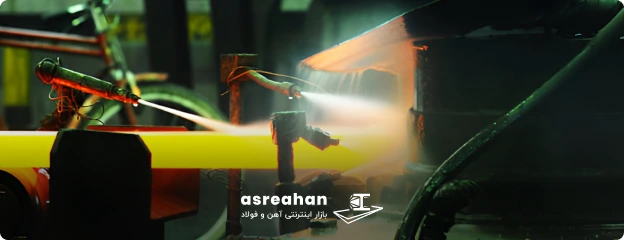
تولید میلگرد به روش نورد سرد یکی از فرآیندهای حیاتی در صنعت فلزکاری است که با هدف کاهش ضخامت و بهبود خصوصیات مکانیکی مواد به کار میرود. در این روش، فلزات بدون نیاز به گرمایش و در دمای محیط، تحت فشار غلتکها قرار میگیرند تا به ابعاد و شکل مورد نظر برسند.
از مزایای برجسته نورد سرد میتوان به افزایش استحکام و سختی فلز، به همراه ارتقاء کیفیت سطحی آن اشاره کرد. علاوه بر این، به دلیل دقت ابعادی بالا و کاهش زبری سطحی، نورد سرد برای ساخت قطعاتی که نیاز به پرداخت دقیق دارند، گزینهای مناسب و ایدهآل است.
ساخت میلگرد به روش ترمکس (فناوری QST)
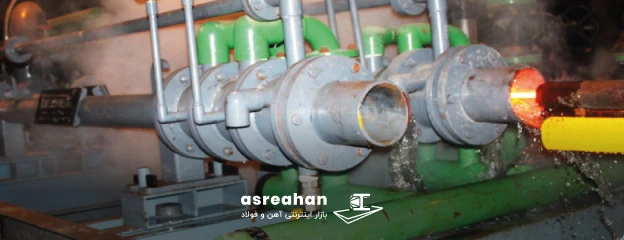
فرآیند تولید میلگرد به روش ترمکس یکی از تکنیکهای پیشرفته در تولید میلگرد است که به منظور بهبود خواص مکانیکی و کاهش هزینههای تولید مورد استفاده قرار میگیرد. در این فرآیند، میلگردهای نورد گرم ابتدا در دمای بسیار بالا بهسرعت خنک میشوند و سپس، آنها را در دمای متوسط حرارت داده شده و دوباره خنک میکنند.
این دو مرحله خنکسازی سبب ایجاد ترکیبی از استحکام بسیار بالا و کشسانیت مناسب در میلگرد میشود، همچنین از خوردگی آنها در برابر شرایط محیطی نیز به میزان قابل توجهی کاسته میشود.
ساخت میلگرد به روش میکرو آلیاژی (آلیاژسازی)
روش میکرو آلیاژی، که به عنوان آلیاژسازی نیز شناخته میشود، یک تکنیک پیشرفته در تولید میلگرد است که به منظور افزایش خواص مکانیکی و مقاومت در برابر خوردگی به کار میرود. در این فرآیند، مقادیر کنترل شدهای از عناصر آلیاژی نظیر منگنز، کروم، نیکل، مولیبدن و برخی دیگر از فلزات به فولاد مذاب افزوده میشوند. این ترکیبهای آلیاژی به فولاد کمک میکنند تا خواص بهتری از نظر استحکام، دوام و مقاومت در برابر شرایط محیطی بدست آورد.
پس از آلیاژسازی، فولاد مذاب به شمش تبدیل شده و سپس از طریق فرآیندهای نورد گرم یا سرد، به میلگرد با ابعاد و مشخصات مورد نظر شکل داده میشود. میلگردهای تولید شده به روش میکرو آلیاژی، به دلیل برخورداری از ریزساختار یکنواخت و کنترل شده، خواص مکانیکی و شیمیایی بسیار برتری نسبت به میلگردهای معمولی دارند.
جدول مقایسه انواع روش ساخت میلگرد
در بخش قبلی، به تفصیل به بررسی روشهای مختلف ساخت میلگرد پرداختیم و متوجه شدیم که هر روش تولید، ویژگیها و کاربردهای خاص خود را دارد. از نورد گرم گرفته تا نورد سرد، ترمکس و میکرو آلیاژی، هر یک از این فرآیندها بهگونهای بر کیفیت، استحکام و هزینههای تولید میلگرد تأثیرگذار هستند. حالا در این قسمت، به منظور مقایسه آسانتر و روشنتر این روشها، جدول زیر را ارائه میدهیم که ویژگیها، مزایا و معایب هر روش را در اختیار شما قرار میدهد.
روش تولید | توضیحات فرآیند | مزایا | معایب |
نورد گرم | حرارت دادن شمش فولادی در دمای بالا و عبور آنها از بین غلتکها | تولید مقاطع یکنواخت و باکیفیت، بهبود خواص مکانیکی | نیاز به دمای بالا، مصرف انرژی زیاد |
نورد سرد | اعمال فشار غلتکها بر فلز در دمای محیط | افزایش استحکام و سختی، بهبود کیفیت سطحی، دقت ابعادی بالا | محدودیت در ابعاد و شکل، نیاز به فشار بالا |
ترمکس (QST) | خنکسازی سریع میلگرد نورد گرم، سپس حرارت دهی و خنکسازی مجدد | استحکام بالا، کشسانیت مناسب، مقاومت در برابر خوردگی | پیچیدگی فرآیند |
میکرو آلیاژی (آلیاژسازی) | افزودن عناصر آلیاژی به فولاد مذاب، سپس انجام فرآیند نورد گرم یا سرد | افزایش خواص مکانیکی و مقاومت در برابر خوردگی، ریزساختار یکنواخت | هزینه بالا، نیاز به کنترل دقیق ترکیب آلیاژ |
استانداردهای تولید میلگرد
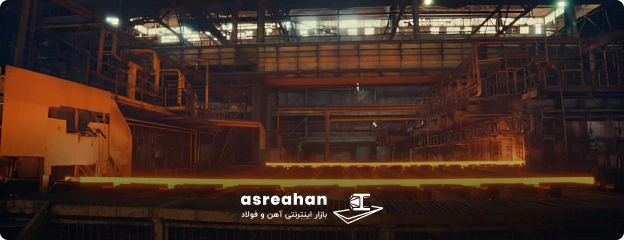
استانداردهای تولید میلگرد به منظور اطمینان از کیفیت، ایمنی و عملکرد میلگرد در سازههای بتنی تدوین شدهاند. این استانداردها مشخصات فنی، الزامات و روشهای آزمون را برای تولید میلگرد با کیفیت مطلوب تعیین میکنند. در این قسمت به برخی از مهمترین استانداردهای تولید میلگرد اشاره شده است:
- استانداردهای ملی ایران
- استاندارد روسیه
- استاندارد ISIRI 3132
- استاندارد DIN
- استانداردهای بینالمللی
- ASTM A706 (محصولات کم آلیاژ)
- استاندارد ASTM A996 آمریکا (فولاد ریلی)
- استاندارد ASTM A955 آمریکا (محصولات زنگ نزن)
- استاندارد ASTM A1035 آمریکا (قطعات کم کربن-کروم)
- استاندارد JIS G3112 ژاپن
- استاندارد DIN آلمان
- استاندارد EASC روسیه
- استاندارد BSI بریتانیا
- استاندارد ANSI ایالات متحده
- آیین نامه ACI(318-14)
- آیین نامه ANSI/AWS D1/4 بتن کانادا
- آیین نامه استرالیا
چه اقداماتی پس از تولید میلگرد انجام می شود؟
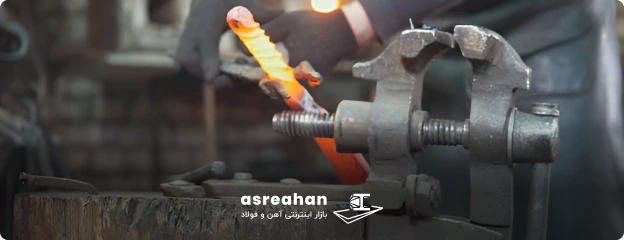
پس از اتمام فرآیند نورد میلگرد یا سایر روشهای ساخت، اقدامات مختلفی برای تضمین کیفیت و آمادهسازی آن برای استفاده در پروژههای ساختمانی انجام میشود. این مراحل شامل آزمایشات کیفی، بستهبندی، برش، حمل و ذخیرهسازی است.
یکی از مهمترین مراحل پس از تولید میلگرد، انجام آزمایشهای مختلف بر اساس استانداردهای پذیرش میلگرد است که باید بر اساس ضوابط مشخص، بهطور دقیق انجام شود. این اقدامات موجب میشوند که میلگردها مطابق با استانداردها و نیاز پروژهها، از نظر خواص فیزیکی و مکانیکی مناسب باشند.
انجام آزمایشات لازم بر اساس ضوابط پذیرش میلگرد
آزمایشهایی که بعد از تولید میلگرد انجام میشود، برای تأیید کیفیت آن ضروری است. این آزمایشات شامل بررسی خواص مکانیکی مانند مقاومت کششی، درصد تغییر شکل (از جمله کشش و فشردگی)، و سختی میلگردها میشود.
بهعلاوه، برخی آزمایشات به بررسی ترکیب شیمیایی فولاد و ارزیابی وجود هرگونه عیب ظاهری مانند ترک یا زنگزدگی میپردازند. آزمایشات باید بر اساس استانداردهای ملی و بینالمللی انجام شوند تا اطمینان حاصل شود که میلگردها برای استفاده در پروژههای ساختمانی ایمن و مناسب هستند.
همچنین، آزمایشهای دیگری مانند آزمایش خمشی و تستهای مقاومت در برابر خوردگی نیز انجام میشود تا ویژگیهای میلگرد در شرایط محیطی مختلف ارزیابی گردد. تمامی نتایج آزمایشات باید بهدقت مستندسازی شوند و گواهیهای لازم برای پذیرش میلگرد صادر شود.
خمکاری میلگرد
خمکاری میلگرد یکی دیگر از فرآیندهایی است که بعد از تولید میلگرد انجام میشود و برای پروژههای ساختمانی مختلف ضروری است. میلگردها بهطور معمول در اندازههای طولی تولید میشوند، اما برای استفاده در سازههای خاص نیاز به تغییر شکل دارند.
خمکاری میلگرد باعث میشود که میلگردها به ابعاد و اشکال مورد نیاز برای پروژههای مختلف، مانند ساختمانها، پلها یا دیگر سازهها، تبدیل شوند. این عملیات نیاز به دقت بالا و استفاده از تجهیزات خاص دارد تا میلگردها بدون ایجاد آسیب یا تغییرات منفی در خواص مکانیکی آنها خم شوند.
در فرآیند خمکاری، میلگردها معمولاً در دماهای خاصی خم میشوند تا از تغییرات ساختاری یا شکستن میلگرد جلوگیری شود. همچنین، رعایت استانداردها و کنترلهای کیفی در این مرحله اهمیت زیادی دارد تا اطمینان حاصل شود که میلگردهای خم شده همچنان خواص موردنظر را دارا هستند و میتوانند در پروژههای مختلف بهطور مؤثر عمل کنند.
کدام تکنولوژی های پیشرفته در تولید میلگرد مورد استفاده قرار می گیرند؟
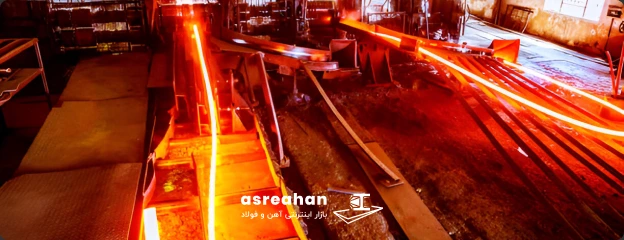
تکنولوژیهای پیشرفتهای که برای تولید میلگرد مورد استفاده قرار میگیرند و در افزایش بهرهوری، بهبود کیفیت محصولات و کاهش هزینهها نقش مهمی ایفا میکنند؛ عبارتاند از:
- فرآیند کوره الکتریکی
- تکنولوژیهای پیشرفته در ریختهگری
- کنترل هوشمند
- بهینهسازی استفاده از انرژی
- استفاده از فناوریهای جدید کنترل کیفیت
- بهرهمندی از کورههای الکتریکی در تولید میلگرد
نحوه تشخیص روش تولید میلگرد
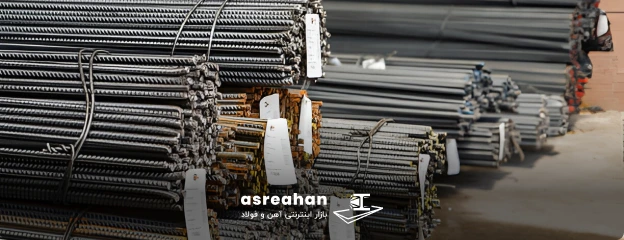
برای شناسایی روش تولید میلگرد خریداریشده، چندین روش وجود دارد که به شما کمک میکند روش ساخت میلگرد را تشخیص دهید و از مناسب بودن آن برای پروژه خود اطمینان حاصل کنید.
- بررسی اطلاعات درجشده روی پلاک بندیل میلگرد: تولیدکنندگان میلگرد موظف هستند اطلاعات مهمی از جمله نوع میلگرد، قطر، استاندارد تولید و روش ساخت را روی پلاک بندیل درج کرده و به بستهبندی محصول الصاق کنند. این اطلاعات معمولاً شامل روش تولید میلگرد نیز میشود.
- بررسی علامت اختصاری حکشده روی بدنه میلگرد: روی بدنه میلگردها معمولاً حروف اختصاری برجستهای حک میشود که نشاندهنده روش تولید آنها است. این کدها معمولاً شامل یکی از حروف زیر هستند:
- T: نشاندهنده تولید به روش ترمکس (خنککاری و برگشت تحت کنترل)
- A: نشاندهنده تولید به روش آلیاژسازی
- U: نشاندهنده تولید با سایر روشها
نحوه قیمت گذاری میلگردها پس از اتمام مراحل تولید میلگرد
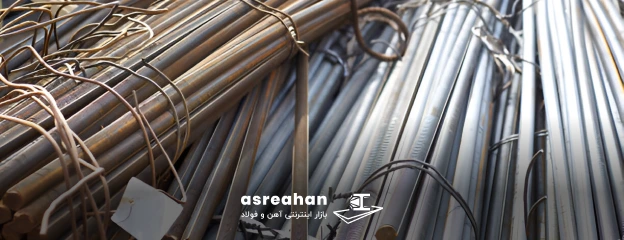
قیمتگذاری میلگرد به عوامل متعددی بستگی دارد که مهمترین آنها روش تولید، نوع مواد اولیه، هزینههای فرآیند ساخت و میزان عرضه و تقاضا در بازار است. هر روش تولید، ویژگیهای خاصی به میلگرد میبخشد که میتواند بر قیمت نهایی آن تأثیر بگذارد.
بهعنوانمثال، میلگردهایی که به روش ترمکس تولید میشوند، معمولاً قیمت پایینتری دارند، زیرا فرآیند تولید آنها سریعتر و کمهزینهتر است. در مقابل، میلگردهایی که به روش میکرو آلیاژی تولید میشوند، به دلیل استفاده از ترکیبات خاص در فرآیند ساخت آنها، گرانتر هستند.
علاوه بر روش تولید، سایز میلگرد نیز در قیمتگذاری آن مؤثر است. میلگردهای ضخیمتر به دلیل مصرف بیشتر مواد اولیه، قیمت بالاتری دارند. این موضوع بیشتر در فروش شاخهای میلگرد اهمیت دارد، درحالیکه در فروش وزنی، قیمت نهایی بر اساس وزن محصول و قیمت روز آهن آلات محاسبه میشود.
یکی دیگر از عوامل کلیدی در قیمت روز میلگرد، نوع سطح آن است. میلگردهای ساده و آجدار از نظر قیمت با یکدیگر تفاوت دارند، زیرا فرآیند تولید میلگرد آجدار نیازمند مراحل بیشتری بوده و هزینه بالاتری دارد. علاوه بر این، میلگردهای آجدار خود به انواع مختلفی تقسیم میشوند و نوع آج آنها نیز میتواند بر قیمت تأثیرگذار باشد. درنهایت، برای اطلاع از قیمت لحظهای میلگرد، میتوانید به وبسایت عصرآهن مراجعه کنید یا با شماره ۰۴۱۴۱۸۰ تماس بگیرید.
مقایسه نحوه تولید میلگرد و انواع روش تولید میلگرد در ایران و سایر کشورهای جهان
تولید میلگرد در سراسر جهان با استفاده از تکنولوژیهای مختلفی انجام میشود که هر کشور با توجه به زیرساختهای صنعتی، میزان دسترسی به مواد اولیه و استانداردهای موجود، روشهای متفاوتی را به کار میگیرد. در این بخش، روشهای تولید میلگرد در ایران، ژاپن و اروپا را بررسی و مقایسه خواهیم کرد.
روش تولید میلگرد در کشور ژاپن
در کشور ژاپن برای تولید میلگرد از تکنیک ترمکس بیشتر از سایر تکنیکها استفاده میکنند. روش ترمکس باعث صرفهجویی در هزینه تولید و افزایش سرعت تولید میشود.
روش تولید میلگرد در اروپا
در کشورهای اروپایی برای تولید میلگرد بیشتر از روش ترمکس استفاده میکنند. این کشورها معمولاً به صرفهجویی در هزینه و سرعت بالا در تولید توجه دارند و به همین دلیل، روش ترمکس گزینه غالب برای تولید میلگرد در این مناطق به شمار میآید.
روش ساخت میلگرد در ایران
ایران یکی از تولیدکنندگان بزرگ میلگرد در جهان است که از روشهای متنوع و پیشرفتهای برای تولید این محصول استفاده میکند. بر اساس آمار منتشر شده، میزان تولید میلگرد ایران در سال ۱۴۰۰ از ۲۵ میلیون تن فراتر رفته و بیش از ۷ میلیون تن آن به بازارهای بینالمللی صادر شده است.
در میان روشهای مختلف تولید میلگرد، روشهای میکروآلیاژی و ترمکس بیشترین کاربرد را در صنعت فولاد ایران دارند. این روشها نهتنها باعث تولید میلگردهایی با کیفیت و استحکام بالا میشوند، بلکه به دلیل تطابق با شرایط اقلیمی و نیازهای بازار داخلی، نقش مهمی در توسعه صادرات این محصول ایفا میکنند. بهکارگیری این فناوریها میتواند به گسترش بازارهای صادراتی ایران و افزایش سهم آن در تجارت جهانی میلگرد کمک کند.
تاثیر تولید میلگرد در اقتصاد و صنعت کشور
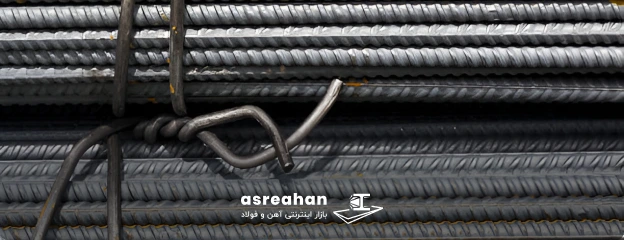
میلگرد به عنوان یکی از اصلیترین مواد اولیه در صنایع مختلفی همچون ساختمانسازی، خودروسازی، تجهیزات صنعتی و زیرساختها شناخته میشود و تولید آن نقش بسیار مهمی در اقتصاد و صنعت ایفا میکند. در ادامه، برخی از چالشها و فرصتهای مرتبط با تولید میلگرد بررسی میشود:
- فرصتها
- رشد تقاضا در صنایع مختلف
- نوآوری در فرآیندهای تولید
- افزایش صادرات
- چالشها
- نوسانات بازار جهانی
- رقابت بینالمللی
- محدودیت در منابع طبیعی
جمع بندی
در جمعبندی مقاله، میتوان گفت که تولید میلگرد فرآیندی پیچیده و متشکل از مراحل مختلفی است که هر یک نقش مهمی در کیفیت و خواص نهایی این محصول ایفا میکنند. روشهای متنوعی نظیر نورد گرم، نورد سرد، ترمکس و میکرو آلیاژی، با توجه به ویژگیها و نیازهای خاص هر پروژه، در تولید میلگرد به کار میروند.
علاوه بر این، استانداردهای تولید و آزمایشات لازم پس از تولید، تضمینکننده کیفیت میلگردها هستند. اهمیت این صنعت در اقتصاد و صنعت کشورها بهویژه در زمینه ساختوساز و پروژههای زیرساختی غیرقابلانکار است. با توجه به تنوع روشهای تولید در کشورهای مختلف، انتخاب روش مناسب میتواند تأثیر قابلتوجهی در کیفیت، هزینه و کارایی میلگردها داشته باشد.