نورد یکی از مهمترین و پرکاربردترین فرآیندهای شکلدهی فلزات است که بهعنوان یک تحول اساسی در صنعت فولاد شناخته میشود. این روش با اعمال فشار کنترلشده بر روی فلزات، باعث تغییر شکل آنها شده و به تولید مقاطع مختلف فولادی با اشکال، ابعاد و خواص مکانیکی کمک میکند. بهطور کلی، نورد نهتنها در اصلاح و بهبود خواص مواد نقش دارد، بلکه یکی از کلیدیترین فرآیندها در تولید محصولات با کیفیت محسوب میشود.
اما نورد به چه معناست و چگونه کار میکند؟ چه تفاوتهایی بین نورد گرم و نورد سرد وجود دارد و هرکدام چه مزایا و معایبی دارند؟ در این مقاله، نگاهی جامع فرآیند نورد خواهیم داشت و با انواع روشهای آن، مراحل آن و کاربردهای گسترده آن در صنعت آشنا خواهیم شد.
نورد چیست؟
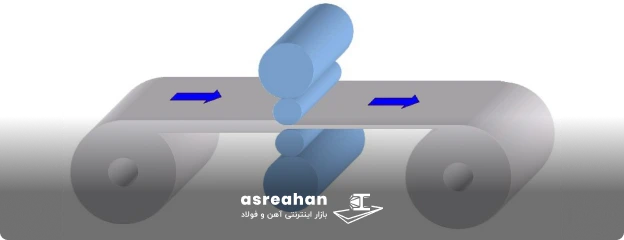
نورد به انگلیسی Rolling نامیده میشود و یکی از پرطرفدارترین و بهترین روشها برای شکلدهی فولاد است که به دو روش نورد گرم و نورد سرد انجام میشود. این فرآیند نه تنها برای شکلدهی فلزات، بلکه برای عملیاتهایی همچون پرداخت سطح فلز، حذف نقطه تسلیم و بهبود خواص مکانیکی نیز کاربرد دارد.
در نورد آهن، مواد اولیه مانند شمش، بیلت و اسلب به محصولات نهایی همچون میلهها، ورقها و صفحات تبدیل میشوند. این تبدیل با استفاده از غلطکهای مخصوصی صورت میگیرد که از طریق اعمال فشار، ضخامت مواد را کاهش یا شکل آنها را تغییر میدهد. به عبارتی، نورد فرآیندی است که به فلزات امکان میدهد تا به شکلها، ابعاد و خواص مورد نظر تبدیل شوند.
فولاد نورد شده یعنی چه؟
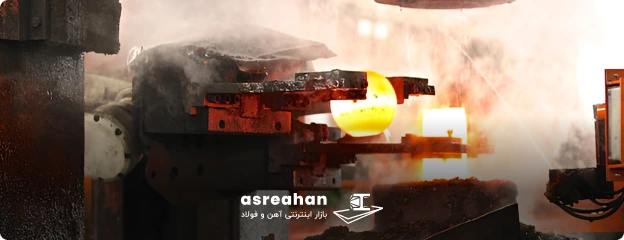
فولاد نورد شده به فولادی گفته میشود که با استفاده از فرآیند نورد، به شکلها و ابعاد مورد نظر تبدیل شده و در صنایع مختلف به کار میرود. این ماده معمولاً به محصولات مختلفی مانند ورق، میلگرد، پروفیل، لوله و تیرآهن تبدیل میشود که در صنایع مختلفی از جمله ساختوساز، خودروسازی، هوافضا و تولید ماشینآلات مورد استفاده قرار میگیرد. ویژگیهای مکانیکی این فولاد، مانند استحکام، انعطافپذیری و قابلیت شکلپذیری، بر اساس نوع نورد و دما تعیین میشود.
تاریخچه نورد
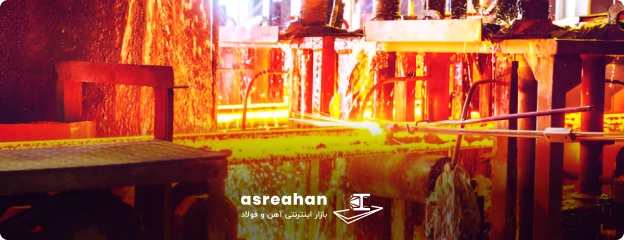
تاریخچه نورد آهنآلات به نیمه قرن هفدهم میلادی بر میگردد. این در حالی است که پیش از آن، در اوایل قرن چهارم میلادی از نورد سرد فلزات غیرآهنی بهطور محدود و پراکنده استفاده میشد. در دوران قبل از نیمه قرن هفدهم، غلتکها بیشتر برای صاف کردن و فشردهسازی مواد مختلف استفاده میشدند. اما ایده استفاده از غلتکها برای کاهش سطح مقطع فلزات و شکلدهی به آنها در این دوره بهوجود آمد.
با اختراع ماشین بخار در قرن هجدهم، صنعت نورد به سرعت پیشرفت کرد. این اختراع نه تنها روند تولید فلزات را تسریع کرد، بلکه موجب بهبود کارایی و افزایش دقت در تولید مقاطع فلزی شد. در پی این تحولات، نورد فلزات به یکی از روشهای اصلی و اساسی در تولید مقاطع فولادی تبدیل گردید و امروزه همچنان در صنعت فولاد از آن بهعنوان یک روش حیاتی برای شکلدهی و تولید مقاطع فولادی استفاده میشود. این پیشرفتها بهویژه در دهههای اخیر باعث تغییرات عمدهای در کیفیت و کمیت تولیدات فولادی در سطح جهانی شده است.
انواع نورد
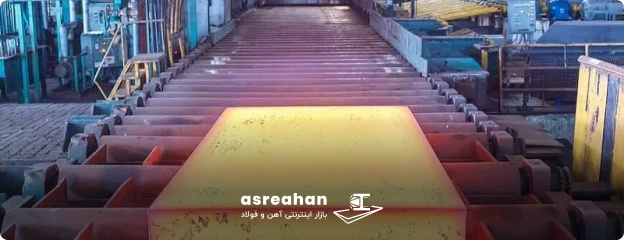
میتوان فرآیند نورد را بسته به شرایط مختلف، از سه دیدگاه مختلف دسته بندی کرد. در این بخش، به بررسی انواع نورد از نظر دما، تغییر شکل و تعداد غلتکها پرداخته میشود.
انواع نورد از نظر دما
نورد از نظر دمای انجام فرآیند به دو دسته اصلی تقسیم میشود: نورد گرم و نورد سرد. هر یک از این دو نوع نورد، ویژگیها و کاربردهای خاص خود را دارند که در انتخاب فرآیند مناسب برای تولید محصولات فلزی نقش مهمی ایفا میکند.
نورد گرم
نورد گرم به فرآیند گرم کردن فلزات تا دمایی بالاتر از دمای تبلور مجدد و سپس عبور آنها از میان غلتکهای نورد گفته میشود. دمای تبلور مجدد دمایی است که در آن دانههای فلز تغییر شکل یافته به دانههای جدید تبدیل میشوند و این امر باعث میشود تا فرآیند شکلدهی فلز راحتتر انجام شود.
نورد گرم معمولاً در دماهایی بالاتر از دمای تبلور مجدد انجام میشود تا علاوه بر افزایش انعطافپذیری فلز، مقاومت آن در برابر تغییر شکل نیز کمتر شود. دمای مورد نیاز برای فلزات و آلیاژهای مختلف متفاوت است.
به طور مثال، برای فولاد این دما بین ۱۱۰۰ تا ۱۳۰۰ درجه سانتیگراد و برای آلومینیوم بین ۳۰۰ تا ۶۰۰ درجه سانتیگراد میباشد. وقتی فلز به این دما رسید، آماده عبور از غلتکها میشود. عبور فلز از میان غلتکها به آن فشار وارد میکند تا ضخامتش کاهش یابد و شکل دلخواه را به خود بگیرد. این نوع نورد برای تولید مقاطع و صفحاتی که در صنایع مختلف به کار میروند، استفاده میشود.
نورد سرد
در فرآیند نورد سرد، عملیات شکلدهی فلزات در دماهایی پایینتر از دمای تبلور مجدد آنها انجام میشود. از آنجا که فلزات در دماهای پایینتر انعطافپذیری کمتری دارند، برای اعمال فشار و تغییر شکل فلزات از جکهای هیدرولیکی یا پنوماتیکی استفاده میشود.
به عبارت دیگر، در نورد سرد، دمای عملیات کمتر از دمای تبلور فلز است، و این باعث میشود که فرایند نیاز به انرژی و تجهیزات خاصی برای تولید تنشهای مکانیکی به جای حرارت داشته باشد.
این نوع نورد مشابه نورد گرم است، اما با تفاوتهایی در میزان پردازش و دقت ابعاد محصولات نهایی که معمولاً در نورد سرد بسیار دقیقتر است. محصولات نورد سرد نه تنها از نظر ظاهری جذابتر هستند، بلکه مقاومت بالاتری نیز دارند. از آنجا که این محصولات نیازمند فرآیندهای اضافی و دقت بیشتری هستند، هزینه تولید آنها معمولاً بیشتر از محصولات نورد گرم است.
نورد سرد در صنایع مختلفی مانند خودروسازی، تجهیزات خانگی، ساختوساز و تولید ورقهای فلزی مثل ورق گالوانیزه برای کاربردهای متنوع، نقش کلیدی دارد.
انواع نورد از نظر تغییر شکل
نورد از نظر نوع تغییر شکلی که در فلز ایجاد میکند، به سه دسته تقسیم میشود: نورد طولی، نورد عرضی و نورد شکلی یا نورد مقطعی.
نورد طولی
در نورد طولی ضخامت فلز کاهش یافته و طول آن افزایش مییابد. این فرآیند عمدتاً برای تولید محصولاتی همچون میلهها، ریلها، پروفیلهای سازهای و سایر مقاطع فلزی به کار میرود.
نورد عرضی
در نورد عرضی، برخلاف نورد طولی که هدف اصلی افزایش طول قطعه است، تمرکز بر افزایش عرض آن قرار دارد. این تفاوت عمده به چینش خاص غلطکها و نحوه اعمال نیرو در هر دو فرآیند برمیگردد.
نورد شکلی یا نورد مقطعی
نورد شکلی یک فرآیند پیشرفته در صنعت فولاد است که برای تولید قطعات فولادی با مقاطع خاص به کار میرود.
انواع نورد بر اساس تعداد غلتک ها
نورد بر اساس تعداد غلتکها به دو نوع اصلی تقسیم میشود: نورد دو غلطکی و نورد چند غلطکی. این تقسیمبندی تأثیر زیادی بر دقت فرآیند و کیفیت محصول نهایی دارد، زیرا تعداد و نحوه چیدمان غلتکها میتواند فشار و میزان تغییر شکل اعمال شده بر فلز را تغییر دهد.
نورد دو غلطکی
نورد دو غلطکی یکی از رایجترین و مؤثرترین انواع نورد است که در آن فلز از میان دو غلطک که در جهات مخالف میچرخند عبور میکند. این روش عمدتاً برای تولید محصولات تخت مانند ورقها و نوارهای فولادی، و همچنین محصولات بلند مانند میلگردها و تیرآهنها استفاده میشود.
نورد چند غلطکی (مانند نورد سه غلتکی و نورد چهار غلتکی)
در نورد چند غلطکی، فلز از میان مجموعهای از غلطکها که معمولاً تعدادشان بیش از دو عدد است، عبور میکند. این فرآیند به تولیدکنندگان امکان کنترل دقیقتری بر روی ابعاد، ضخامت و کیفیت سطحی فلز را میدهد. همچنین، با استفاده از این نوع نورد، تغییرات شکلدهی و نازکسازی فلز با دقت بیشتری انجام میشود، که موجب بهبود خواص مکانیکی و سطحی محصول نهایی میگردد..
نورد خوشه ای
روش نورد خوشهای به استفاده از دو غلطک اصلی و دو یا چند غلطک پشتیبان در فرآیند نورد گرم و سرد اشاره دارد. در این تکنیک، غلطکها با فشار مناسب به سطح فلزات وارد میشوند تا شکلدهی و صافکردن فلز بهطور یکنواخت انجام شود.
نورد چندگانه
نورد چندگانه شامل ترکیبی از غلطکهای درگیر با قطر کم، ردیفی از غلطکهای میانی و در نهایت ردیفی از غلطکهای بزرگ پشتیبان است. این سیستم بهویژه برای تولید ورقهایی با ضخامت بسیار کم و دقت بالا کاربرد دارد.
فرآیند نورد
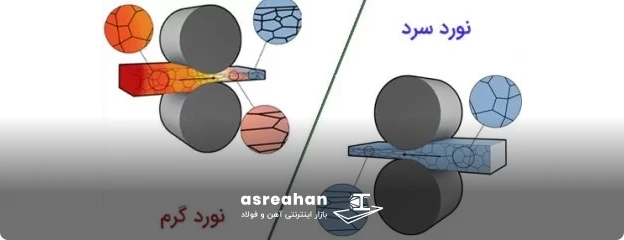
همانطور که در بخش قبلی نیز گفته شد، فرآیند نورد به دو روش نورد گرم و نورد سرد انجام میشود که در ادامه این بخش به تشریح مراحل هر کدام از روشها میپردازیم.
مراحل نورد گرم
برای تولید مقاطع به روش نورد، ابتدا لازم است که فرآیند نورد گرم روی آنها اعمال شود. مراحل نورد گرم به ترتیب زیر است:
ریختهگری پیوسته شمش
ابتدا فولاد ذوب شده را داخل غالب میریزند تا شمش تولید شود.
نورد گرم
نورد گرم، یکی از مراحل اساسی در نورد است که در آن شمش فولادی با عبور از میان دو غلتک بزرگ و انجام یک حرکت تکراری، به تدریج نازکتر شده و ضخامت آن کاهش مییابد.
کوره پیشگرمکن
در این مرحله، فولاد درون کوره پیشگرمکن قرار میگیرد و دمای آن تا سطح مطلوبی افزایش مییابد، بهگونهای که ساختار آن برای فرآیندهای بعدی آماده شود، اما به نقطه ذوب نرسد.
نورد نهایی
در این مرحله، ضخامت از طریق سیستم اتوماتیک، بررسی و کنترل میشود.
خنک کاری
در مرحله آخر، دمای فلز را در مدت زمان معین با استفاده از روشهای مشخص پایین میآورند.
مراحل نورد سرد
برای اجرای فرآیند نورد سرد بر روی مقاطع، ابتدا شمش تحت فرآیند نورد گرم قرار میگیرد. سپس، محصول اولیه حاصل از نورد گرم طبق مراحل زیر وارد فرآیند نورد سرد میشود:
اسیدشویی
در ابتدا، برای از بین بردن پوستههای اکسیدی، اسیدشویی انجام میشود.
نورد سرد
در این مرحله، شمش فولادی از میان غلطک نورد سرد عبور داده میشود تا ضخامت آن کاهش یابد.
عملیات حرارتی
این فرآیند که به آنیلینگ یا بازپخت نیز شناخته میشود، موجب بهبود خواص مکانیکی و متالورژیکی فلز شده و تنشهای داخلی آن را کاهش میدهد.
نورد پوستهای
در مرحله نهایی، نورد پوستهای برای حذف موجهای سطحی فلز، بهبود یکنواختی ضخامت و افزایش سختی سطحی انجام میشود.
معرفی انواع فرآیند نورد
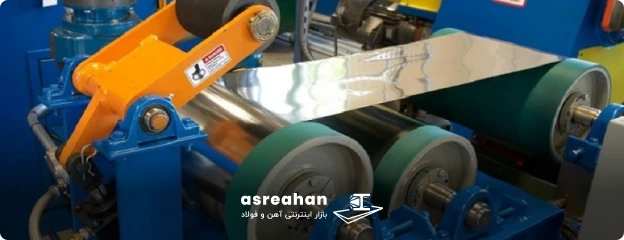
فرآیند نورد انواع مختلفی دارد که در ادامه به بررسی هر یک از آنها میپردازیم.
نورد حلقه ای
نورد حلقهای روشی برای تولید حلقههای بدون درز در ابعاد و اشکال مختلف است. در این فرآیند، یک قطعه اولیه دایرهایشکل با عبور از میان دو غلطک بهصورت کنترلشده تغییر شکل داده و به اندازه مورد نظر میرسد.
نورد رزوه
نورد رزوهای یک روش شکلدهی سرد است که در آن رزوههای صاف یا مخروطی بر روی میلگرد یا سیم ایجاد میشود. این فرآیند با حرکت رفت و برگشتی دو قالب تخت روی سطح سیم یا میلگرد انجام شده و منجر به شکلدهی رزوهها میشود.
شکل گیری یا خم رول (Roll forming)
فرآیند شکلدهی به کمک ورق یا شکلدهی غلتکی، نوعی نورد محسوب میشود که در آن یک نوار بلند فلزی بهصورت پیوسته خم شده و به مقطع دلخواه تبدیل میشود.
نورد تخت (Flat rolling)
فرآیند نورد تخت یکی از سادهترین انواع نورد محسوب میشود که در آن ماده اولیه و محصول نهایی دارای مقطع مستطیلی هستند. در این روش، ماده از میان دو غلطک که در جهت مخالف یکدیگر میچرخند، عبور داده میشود.
نورد شکل ساختاری (Structural Shape Rolling)
نورد ساختاری برای شکلدهی تیرآهنهای H، L و U رایج است. در این فرآیند، فولاد را درون کورهای تا دمای تقریبی ۱۲۰۰ درجه سانتیگراد حرارت میدهند. سپس با استفاده از غلتکها و استوانههای فشاری، آن را شکل داده و به فرم نهایی درمیآورند.
نورد کنترل شده (Controlled rolling)
این روش، یک فرآیند ترکیبی از پردازش حرارتی و تغییر شکل مکانیکی است. در این فرآیند، عملیات حرارتی بهطور همزمان با تغییر شکل انجام میشود. گرمای ایجاد شده که دمای قطعه را بالاتر از نقطه تبلور مجدد میبرد، برای عملیات حرارتی نیز به کار میرود، بهگونهای که نیاز به عملیات حرارتی جداگانه کاهش مییابد.
نورد فورج (Forge rolling)
فورجینگ فلزات فرآیندی است که در آن با اعمال نیروهای فشاری، فلزات شکلدهی شده و به فرم دلخواه در میآیند. این روش که معادل آهنگری فلزات است، یکی از اصلیترین تکنیکهای مورد استفاده در صنعت برای تولید مقاطع فولادی محسوب میشود.
مزایا و معایب نورد چیست؟
فرآیند نورد سرد و گرم در شرایط و کاربردهای متفاوت مورد استفاده قرار میگیرند و هرکدام مزایا و معایب ویژهای دارند که بر کیفیت و هزینه تولید تأثیر میگذارند.
- مزایای نورد سرد:
- دقت ابعادی بالا
- سطح صاف و یکنواخت فلزات
- استحکام بالا
- معایب نورد سرد:
- هزینه بالا
- شکلدهی محدود
- مزایای نورد گرم:
- کاهش مصرف انرژی و هزینهها
- قابلیت بهبود خواص فلزات و آلیاژها
- انعطافپذیری در تولید مقاطع مختلف
- معایب نورد گرم:
- اکسیداسیون و کیفیت سطح پایینتر
- مشکل در تنظیم ابعاد دقیق
- نیاز به خنککاری
دستگاه نورد چیست و از چه اجزایی تشکیل شده است؟
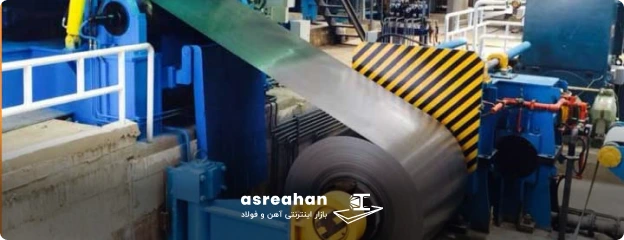
دستگاه نورد یک دستگاه مکانیکی است که برای تغییر شکل فلزات، به ویژه تبدیل شمشهای فولادی به مقاطع مختلف مانند ورقها، میلگردها و لولهها، استفاده میشود. این دستگاه با اعمال فشار به فلزات و عبور آنها از میان غلتکها، ابعاد و ویژگیهای آنها را تغییر میدهد. دستگاه نورد از اجزای مختلفی تشکیل شده است که هر کدام نقش خاصی در فرآیند نورد دارند. این اجزا شامل:
- غلتکها
- قفسه
- یاتاقانها
- نیرو محرکه
- محفظه محافظ
- سیستم هیدرولیک و کنترل
مقایسه تفاوت نورد سرد و گرم
نورد سرد و نورد گرم دو فرآیند متفاوت هستند که در تولید مقاطع فولادی به کار میروند. هرکدام از این روشها ویژگیها و کاربردهای خاص خود را دارند که انتخاب مناسب هر کدام بستگی به نوع محصول، نیاز به خواص مکانیکی خاص و شرایط تولید دارد. در این بخش، به مقایسه تفاوتهای نورد سرد و گرم خواهیم پرداخت.
تفاوت نورد گرم و سرد
تفاوت نورد گرم و سرد در این است که برای نورد گرم به تجهیزات کمتری نیاز است. در نورد گرم، نیروی کمتری به قطعه وارد میشود، بنابراین مقاومت سطح قطعه در نورد سرد بیشتر خواهد بود. علاوه بر این، استحکام قطعات در نورد گرم نسبت به نورد سرد بالاتر است. از طرف دیگر، ویژگیهایی مانند سختی کرنشی، دقت ابعاد و کیفیت سطح در نورد سرد بهتر از نورد گرم است، ولی در نورد گرم، استحکام و اندازه قطعات بیشتر از نورد سرد مشاهده میشود.
نورد گرم بهتر است یا نورد سرد؟
انتخاب بین نورد گرم و نورد سرد بستگی به نیازهای خاص محصول و کاربرد آن دارد. اگر نیاز به مقاطع با دقت بالا، سطح صاف و استحکام زیاد باشد، نورد سرد بهترین گزینه است. از طرف دیگر، اگر هدف تولید مقاطع بزرگتر با هزینه کمتر و سرعت بیشتر باشد، نورد گرم گزینهای مناسبتر خواهد بود.
چه نکاتی را باید در نورد کاری رعایت کرد؟
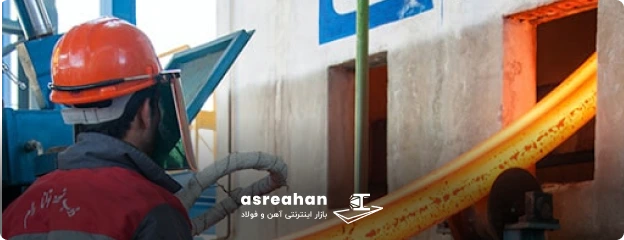
برای انجام فرآیند نورد بهصورت مؤثر و با کیفیت، رعایت نکات کلیدی ضروری است. کنترل دقیق دما، فشار و سرعت نورد، انتخاب صحیح نوع غلتکها، استفاده از روانکارهای مناسب، و نظارت مستمر بر کیفیت محصولات نهایی از جمله این نکات هستند. همچنین، توجه به ایمنی محیط کاری و استفاده از تجهیزات حفاظتی برای جلوگیری از آسیب به کارکنان نیز از اهمیت بالایی برخوردار است. رعایت این موارد باعث بهبود کیفیت، کاهش هزینهها و افزایش بهرهوری در فرآیند نورد میشود.
کاربردهای نورد در مقاطع فولادی
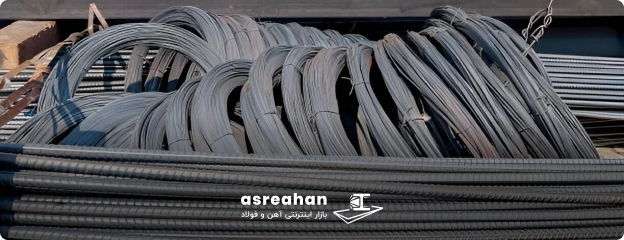
فرآیند نورد با تبدیل شمشهای فولادی به انواع مقاطع با ابعاد، ضخامت و خواص مکانیکی متفاوت، نقش حیاتی در تولید محصولات مورد نیاز در صنایع مختلف کاربردهای گستردهای دارد. در ادامه به معرفی برخی از کاربردهای عمده نورد میپردازیم:
- صنعت ساختمانسازی: نورد در تولید مقاطع فولادی مورد نیاز در صنعت ساختمانسازی، نظیر میلگرد، تیرآهن، و پروفیلهای فولادی نقش اساسی دارد. نورد میلگرد برای تغییر شکل میلگرد انجام میشود.
- صنعت خودروسازی: نورد در صنعت خودروسازی نیز کاربرد فراوانی دارد. قطعات مختلف خودرو از جمله قطعات موتور، بدنه و شاسی از فولاد نورد شده تولید میشوند.
- تجهیزات و ماشینآلات صنعتی: بسیاری از ماشینآلات صنعتی و تجهیزات مرتبط با خطوط تولید، نیاز به مقاطع فولادی با ویژگیهای خاص دارند که از طریق نورد تولید میشوند. این مقاطع در ساختار نوار نقالهها، ماشینآلات سنگین، و دیگر تجهیزات صنعتی بهکار میروند و موجب استحکام و دوام بیشتر دستگاهها و سیستمها میشوند.
- صنعت لولهکشی: لولههای فولادی که در سیستمهای لولهکشی استفاده میشوند، از طریق فرآیند نورد تولید میشوند. پس از نورد، لایههای فولادی به یکدیگر جوش داده میشوند تا لولهها بهصورت استوانهای شکل درآیند.
- تجهیزات خطوط راهآهن: مقاطع فولادی نورد شده بهعنوان پایههای اصلی خطوط راه آهن و در بخشهایی نظیر ریل استاندارد، ریل جرثقیل و ریل UIC به کار میروند. این مقاطع با استحکام و مقاومت بالای خود، ایمنی و عملکرد مطلوب در حملونقل ریلی را فراهم میکنند.
انواع محصولات تولیدی از طریق فرآیند نورد
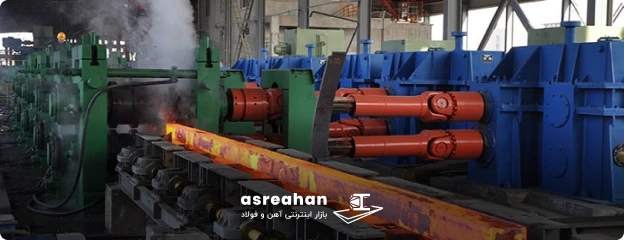
فرآیند نورد یکی از رایجترین روشهای تولید مقاطع فولادی است که طی آن، شمشهای فولادی تحت فشار و عبور از میان غلتکها تغییر شکل داده و به ابعاد و اشکال موردنظر تبدیل میشود. این فرآیند برای تولید انواع محصولات فولادی مانند تیرآهن، نبشی، ناودانی، ورق و میلگرد به کار میرود. بسته به نوع نورد فولاد، محصولات نهایی میتوانند خواص مکانیکی و ظاهری متفاوتی داشته باشند.
چنانچه قصد خرید ورق یا انواع دیگری از محصولات فولادی را دارید، میتوانید از طریق مجموعه عصرآهن اقدام کرده و محصولات مورد نظر خود را با بهترین قیمت و کیفیت تهیه کنید.
نورد میلگرد چیست؟
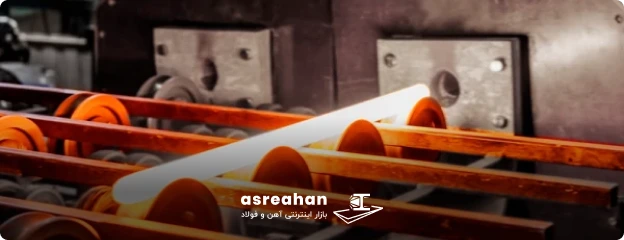
فرآیندی که طی آن شمشهای فولادی تحت فشار غلتکهای مخصوص قرار گرفته و به میلگرد تبدیل میشوند، نورد میلگرد نامیده میشود. در این روش، شمشهای فولادی، که معمولاً از نوع بیلت هستند، پس از مرحله ریختهگری وارد خط نورد شده و با عبور از چندین مرحله غلتککاری به قطر و شکل استاندارد میلگرد در میآیند.
نورد تیرآهن چیست؟
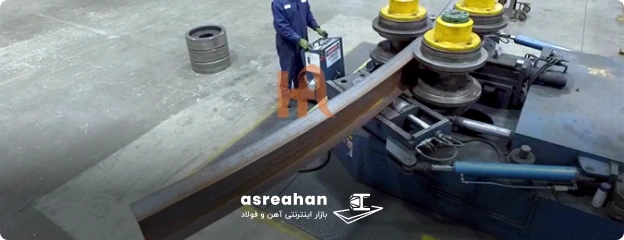
نورد تیرآهن یکی از فرآیندهای مهم فلزکاری است که در شکلدهی و اصلاح نیمرخ تیرآهن و ایجاد انحنا در آنها به کار میرود. این روش به مهندسان و طراحان اجازه میدهد تا تیرآهنها را مطابق با نیازهای خاص پروژههای عمرانی و صنعتی به اشکال منحنی یا دایرهای تبدیل کنند. نورد تیرآهن معمولاً در ساخت سازههایی مانند پلها، تونلها، سقفهای قوسی، اسکلت ساختمانها و سایر پروژههایی که نیاز به تیرآهنهای خمیده دارند، کاربرد دارد.
جمع بندی
نورد بهعنوان یکی از مهمترین فرآیندهای شکلدهی فلزات، نقش اساسی در صنعت فولاد و تولید مقاطع مختلف دارد. این فرآیند که به دو روش اصلی نورد گرم و نورد سرد انجام میشود، امکان تولید محصولاتی با ویژگیهای متنوع را فراهم میکند. هرکدام از این روشها مزایا و معایب خاص خود را دارند و بسته به نیاز صنعت، انتخاب میشوند. در نهایت، شناخت فرآیند نورد، انواع آن و تفاوتهای میان روشهای مختلف، به تولیدکنندگان و مصرفکنندگان کمک میکند تا انتخابهای بهتری در زمینه تهیه و استفاده از مقاطع فولادی داشته باشند. امیدواریم این مقاله توانسته باشد دید کاملی از این فرآیند ارائه دهد و شما را در درک بهتر این فناوری کلیدی یاری کند.